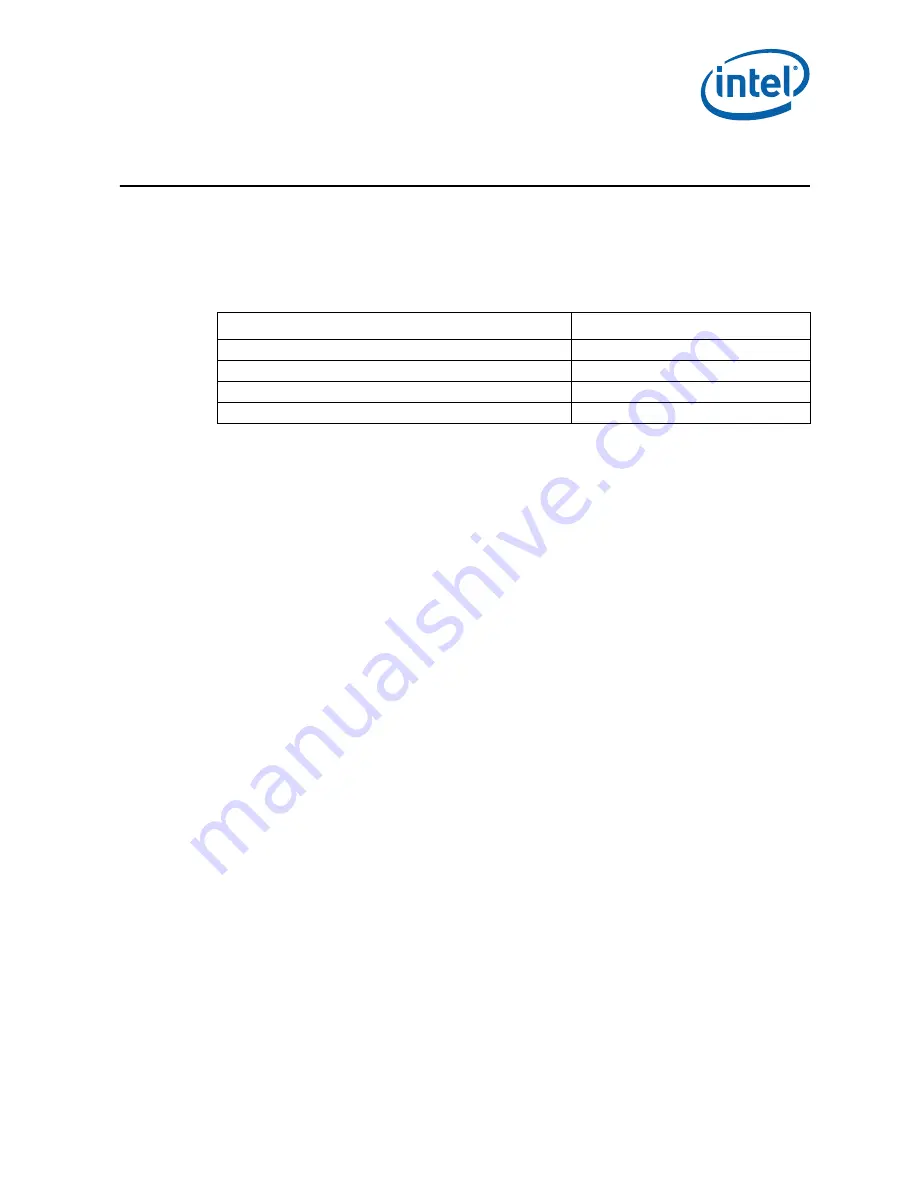
Intel® Xeon® Processor E5-2400 Product Family
85
Thermal/Mechanical Design Guide
Socket Mechanical Drawings
C
Socket Mechanical Drawings
lists the mechanical drawings included in this appendix.
Table C-1.
Mechanical Drawing List
Drawing Description
Figure Number
“Socket Mechanical Drawing (Sheet 1 of 4)”
“Socket Mechanical Drawing (Sheet 2 of 4)”
“Socket Mechanical Drawing (Sheet 3 of 4)”
Summary of Contents for Xeon E5-2400
Page 8: ...8 Intel Xeon Processor E5 2400 Product Family Thermal Mechanical Design Guide ...
Page 12: ...Introduction 12 Intel Xeon Processor E5 2400 Product Family Thermal Mechanical Design Guide ...
Page 22: ...LGA1356 Socket 22 Intel Xeon Processor E5 2400 Product Family Thermal Mechanical Design Guide ...