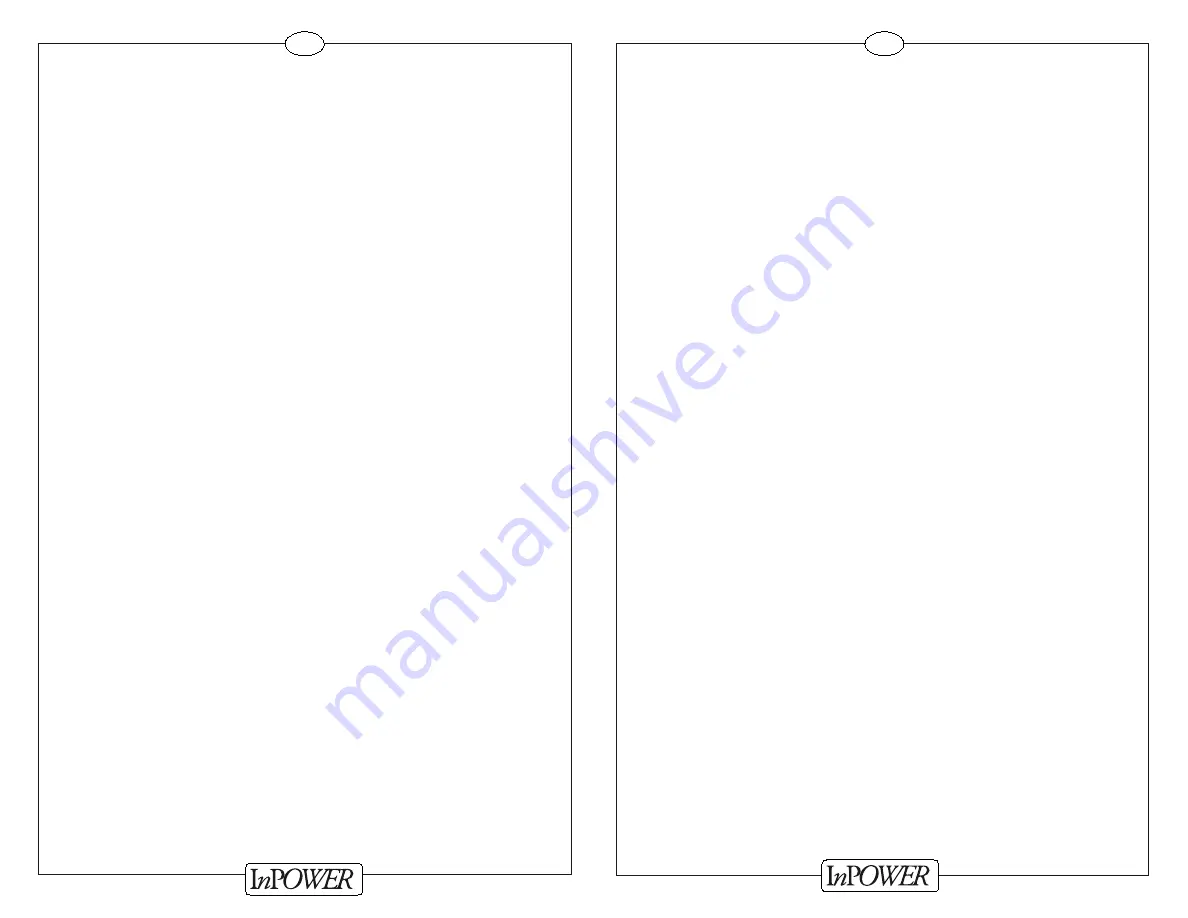
3
6
2. Mode Priorities:
A mode priority selection scheme is provided that will eliminate conflicts if
more than one mode is selected at a time. In the case of one or more
modes being selected, the following priorities will be established:
RPM1 Highest - Will override all other modes
RPM2 Second - Will override lower modes
RPM3
Third - Will override lower mode
CHRG
Fourth
3. Charge Protect Mode (Only on ETM67A):
Function: Varies rpm to maintain battery charge
voltage
Control Terminal: CHRG
Activation: Apply +12V to CHRG terminal
RPM Range: 900 to 1700 rpm
Battery Voltage Levels:
13.3 Vdc Increase rpm; 13.5 Vdc
Decrease rpm
Status Indicators
A 10 segment LED provides status and problem detection information.
Refer to the following table for coding of these functions. NOTE - These
LED indicators will only be powered when a Mode (RPM1, RPM2,
RPM3, CHRG) is selected.
LED Status Indication
BUSS On Solid Module ON and functioning
BUSS Flashing Module ON, but a problem was
Detected with Data Buss
GEAR On Solid Transmission in PARK position
GEAR Flashing Transmission not in PARK position
PK BRK
On Solid Park Brake set
PK BRK
Flashing Park Brake not set
SR BRK
On Solid Service Brake off
SR BRK
Flashing Service Brake applied
VSPEED
On Solid Vehicle is stationary
VSPEED
Flashing Vehicle is moving
Continued...
5. PTO Enable Wiring - Diesel Engines Only (Continued)
On 2009-2010 Gvans there is no PTO Enable function so the following
procedure must be used when going to high idle:
Step 1
Turn on the Cruise Control
Step 2
Turn on the ETM67A/68A
Step 3
Press the Cruise Control Set button
6. Wire the Mode Selection Controls
The following wiring is required by the customer to select the operating
modes required to run the ETM system. You will need to supply contact
closures such as a toggle switch or relay contact to 12 volts at the
ETM module’s terminals for the required preset rpm modes (RPM1,
RPM2, RPM3 or CHRG). It is important that the +12 volts used to feed the
mode select terminals is from the Ignition Switch power source, and it
should be properly fused. That is, it must be +12 volts when the Ignition
Switch is On, and zero volts when the Ignition Switch is Off.
7. Wire the Power and Ground
Install a wire from a good ground (battery negative) to the GND terminal
on the ETM67A/68A module. Install a Fast Idle Switch (not supplied with
ETM system) and wire one side of the switch to a source of +12 volts that
is fused and only powered when the ignition switch is in the On position.
Wire the other side of the switch to the +12V terminal on the ETM module
and to the contacts that select the RPM1, RPM2 & RPM3 modes (see
diagram on page 4).
E. Setup and Calibration
The only calibration required is the speed rpm setting for the three preset
rpm modes (RPM1, RPM2 & RPM3). To perform the calibration activate
the desired preset mode, then adjust the respective speed calibration
potentiometer (RPM1, RPM2 or RPM3) for the required speed. NOTE -
The calibration potentiometers are located on the top of the module in
recessed holes. Take care to use a proper size screwdriver (3/64” /
1.5mm) or damage to the potentiometers may result, voiding the warranty.
D. Installation (Continued)
C. Operation (Continued)
OM-64G ETM67A & ETM068A
OM-64G ETM67A & ETM068A