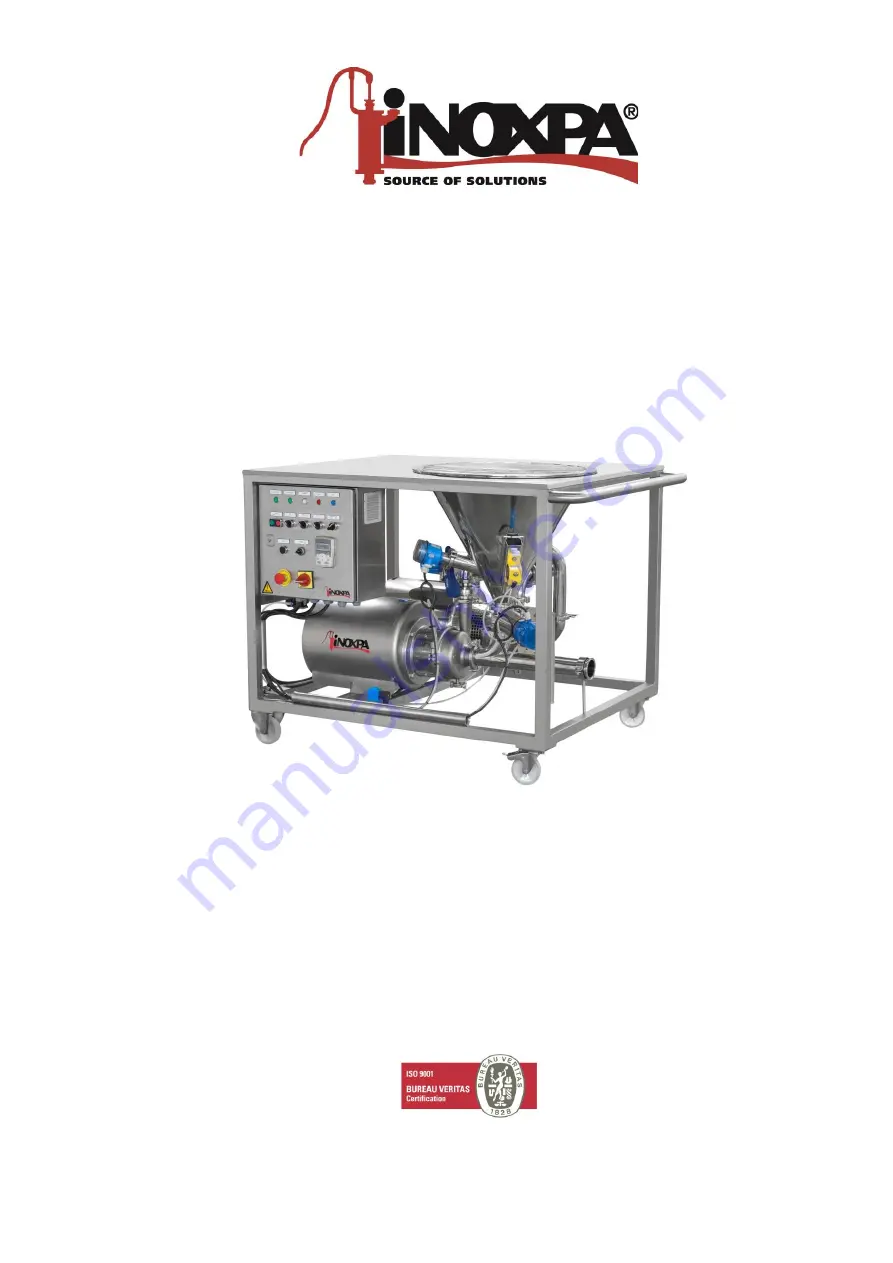
INSTALLATION, SERVICE AND
MAINTENANCE INSTRUCTIONS
Table blender
MM-1, MM-2, MM-3
INOXPA, S.A.
c/Telers, 54 Aptdo. 174
E-17820 Banyoles
Girona (Spain)
Tel. : (34) 972 - 57 52 00
Fax. : (34) 972 - 57 55 02
email: [email protected]
www.inoxpa.com
Original Manual
02.100.30.01EN
2021/11
(A)