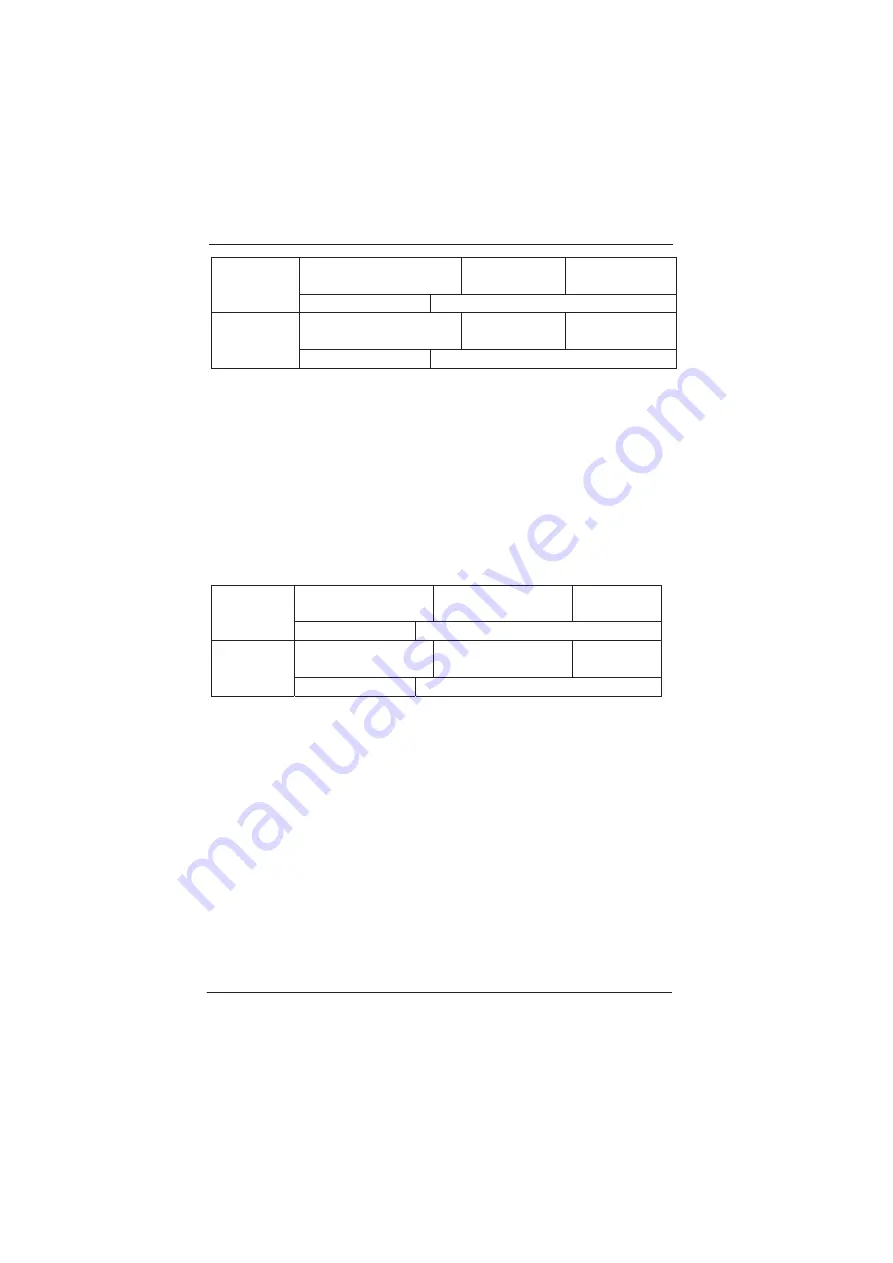
MD280/MD280N User Manual Parameter Description
- 167 -
Wing frequency
amplitude
Factory
default value
0.0%
F7-01
Setup range
0.0% to 100.0%
Kick frequency
amplitude
Factory
default value
0.0%
F7-02
Setup range
0.0% to 50.0%
It is used to determine the amplitude value and the kick frequency value.
Swing relative to the center frequency (variable swing, select F7-00 as 0):
Swing (AW) =frequency source F0-01 setup times swing amplitude F7-01.
Swing relative to the maximum frequency (fixed swing, select F7-00 as 1):
Swing (AW) = maximum frequency F0-04 times swing amplitude F7-01.
When the swing is running, the kick frequency relative to the swing= Swing
(AW) times kick frequency amplitude F7-02.
If “Swing relative to the center frequency (variable swing amplitude, select
F7-00 as 0)” is selected, the kick frequency is variable value.
If “Swing relative to the maximum frequency (fixed swing, select F7-00 as 1)”
is selected, the kick frequency is fixed value.
Swing frequency
cycle
Factory default
value
10.0s
F7-03
Setup range
0.0s to 3000.0.0s
Triangle wave boost
coefficient
Factory default
value
50.0%
F7-04
Setup range
0.0% to 100.0%
Swing frequency cycle: It defines the time of a whole cycle for rising and
falling of the swing frequency.
The triangle wave rising and falling time is as shown in Fig.6-22:
Triangle wave rising time= Swing frequency cycle F7-03 times triangle wave
rising time coefficient F7-04 (unit: s)
Triangle wave falling time= Swing frequency cycle F7-03 times (1-triangle
wave rising time coefficient F7-04) (unit: s)
Remark: When the inverter is running with swing frequency, if the center
frequency changes, it stops swinging until the inverter running from the
current center frequency to the changed center frequency.
Caution: When the inverter is running with swing frequency, if the center
frequency changes, it stops swinging until the inverter running from the
current center frequency to the changed center frequency.
efesotomasyon.com
Summary of Contents for MD280 Series
Page 4: ...Preface MD280 MD280N User Manual IV efesotomasyon com...
Page 8: ...efesotomasyon com...
Page 9: ...MD280 MD280N User Manual Safety and Precautions 9 Safety and Precautions efesotomasyon com...
Page 17: ...MD280 MD280N User Manual Safety and Precautions 17 Product Information efesotomasyon com...
Page 40: ...Product Information MD280 MD280N User Manual efesotomasyon com...
Page 60: ...Mechanical and Electrical Installation MD280 MD280N User Manual 60 efesotomasyon com...
Page 66: ...Operation and Display MD280 MD280N User Manual 66 efesotomasyon com...
Page 107: ...MD280 MD280N User Manual Function Parameter Table 107 Parameter Description efesotomasyon com...
Page 192: ...Parameter Description MD280 MD280N User Manual 192 efesotomasyon com...
Page 193: ...MD280 MD280N User Manual Parameter Description 193 EMC efesotomasyon com...
Page 198: ...EMC MD280 MD280N User Manual 198 efesotomasyon com...
Page 199: ...MD280 MD280N User Manual EMC 199 Fault Diagnosis and Countermeasures efesotomasyon com...
Page 227: ...efesotomasyon com...