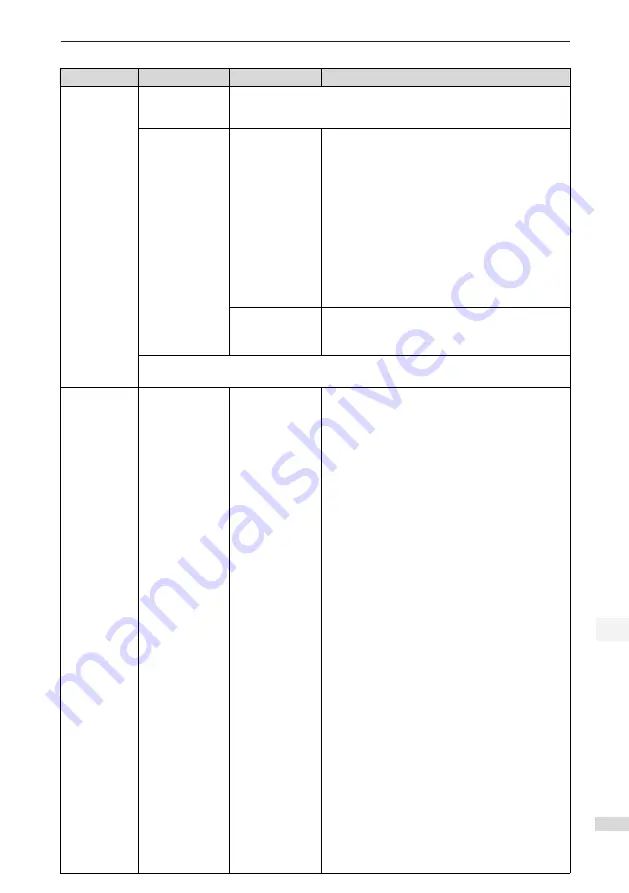
5 Troubleshooting
5
- 45 -
During Startup
Fault Symptom
Cause
Confirming Methods
Set the S-ON
signal to ON.
The operation
panel displays "Er.
xxx".
Remove the fault.
Shaft of the servo
motor is in free
running status.
1. The S-ON
signal is invalid.
Set operation panel to servo status display and view
whether the operation panel displays "rdy" rather than
"run".
Check whether any parameter in groups H03 and
H17 is set for FunIN1(S-ON). If yes, check that the
corresponding DI is set to ON. If not, allocate the
function and set the corresponding DI to ON. See
group H03 in Chapter 7 for details on setting of input
terminal parameters.
If a parameter in group H03 has been set for
FunIN1(S-ON) and logic of corresponding DI is logic,
but the operation panel still displays "rdy". In this case,
check whether the DI terminal is connected correctly
by referring to Chapter 3 in the IS620P User Manual.
2. Selection of
control mode is
incorrect.
Check whether H02-00 is set to 0. If it is set to 2
(torque mode), motor shaft must be in free running
status because default torque reference is 0.
After the preceding causes are removed, the operation panel should display "run".
Input speed
reference
Servo motor does
not rotate or the
motor speed is
abnormal.
Speed reference
(H0B-01) is 0.
AI wiring is incorrect.
When speed reference is input from AI, check whether
the analog input channel is selected correctly and
check whether the selected AI terminal is wired
correctly by referring to Chapter 3 in the IS620P User
Manual.
Speed reference selection is incorrect.
Check whether H06-02 (speed reference selection) is
set correctly.
Speed reference is not input or is abnormal.
1. When AI is selected to input speed reference,
check whether AI related parameters in group H03 are
set correctly first. Then check whether input voltage
is correct by observing voltage on oscilloscope or
viewing AI sampling voltage in H0B-21 or H0B-22.
2. When digital setting is used to set speed reference,
check whether H06-03 (keypad setting value of speed
reference) is set correctly.
3. When multi-speed is used to set speed reference,
check whether the parameters in group H12 are set
correctly.
4. When serial comms. is used to set speed reference,
check whether H31-09 (speed reference set via
communication is set correctly.
5. When jog speed reference is used to set speed
reference, check whether H06-04 (jog speed setting
value) is set correctly, whether DI functions FunIN.18:
(forward jog) and FunIN.19: JOGCMD-
(reverse jog) have been allocated and whether logic of
corresponding DIs is valid.
6. Check whether H06-05 (acceleration ramp time
constant of speed reference) and H06-06 (deceleration
ramp time constant of speed reference) are set
correctly.
7. Check whether the DI function FunIN.12: ZCLAMP
(zero speed clamp function) is misallocated and
whether valid logic of corresponding DI is corrected.