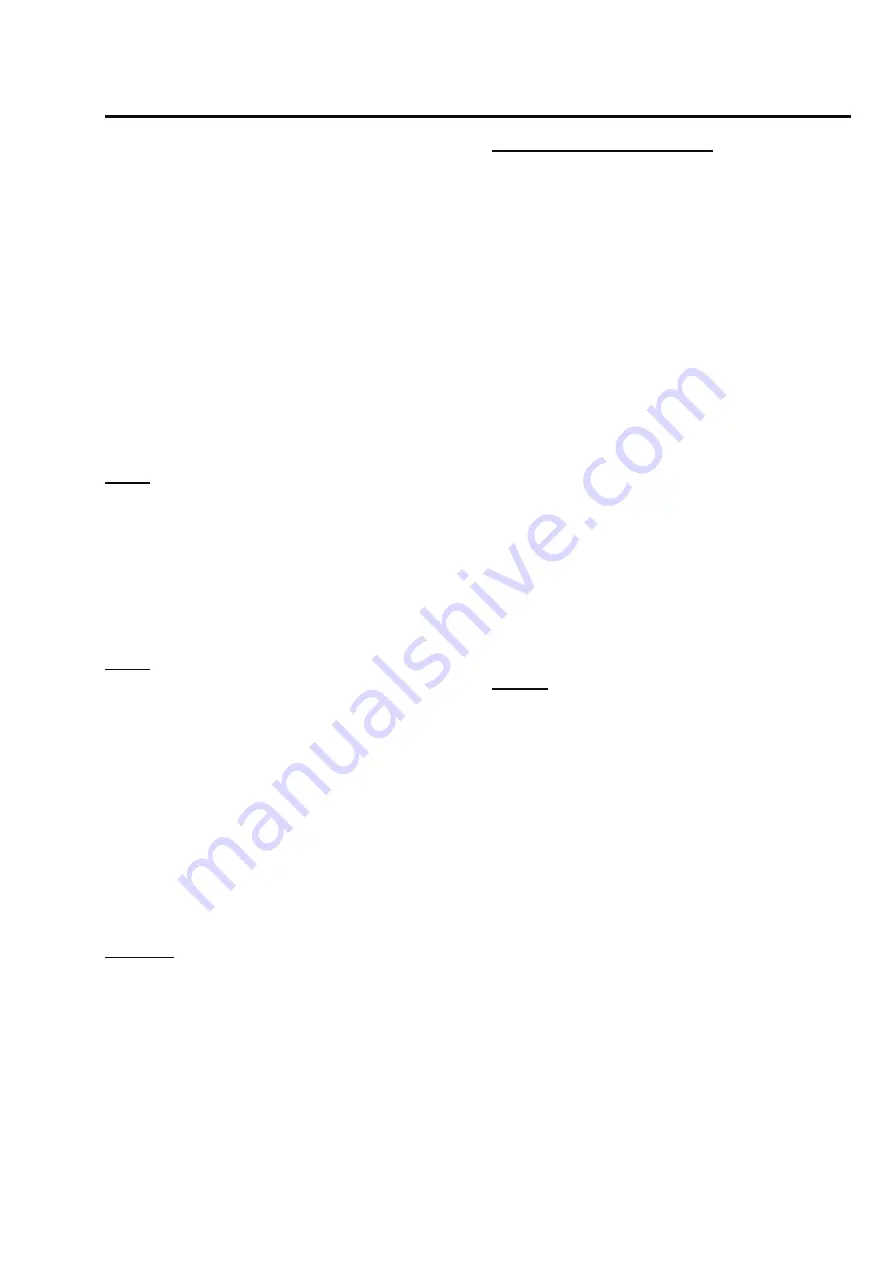
Manual No. 54771142 (7/01)
(
28
)
07/18/01
6.
Install cleaned or new elements in the
reverse order to the above. Tighten wing
nuts firmly and replace cotter pin.
7.
Inspect to ensure that the end cap seals
tightly 360 degrees around the air cleaner
body.
In the event that the filter element must be reused
immediately, compressed air cleaning (as follows)
is recommended since the element must be
thoroughly dry. Direct compressed air through the
element in the direction opposite to the normal
airflow through the element.
Move the nozzle up and down while rotating the
element. Be sure to keep the nozzle at least one
inch (25.4mm) from the pleated paper.
NOTE: To prevent damage to the element,
never exceed a maximum air pressure of 100
psi (700 kPa).
In the event the element is contaminated with dry
dirt, oil or greasy dirt deposits, and a new element
is not available, cleaning can be accomplished by
washing,
using
the
air
cleaner
element
manufacturer’s recommendations.
NOTE: It is recommended that replacement
elements be installed in the unit. The elements
just removed for cleaning can be washed and
stored as future replacement elements.
In addition, the air cleaner system (housing and
piping) should be inspected every month for any
leakage paths or inlet obstructions. Make sure the
air cleaner mounting bolts and clamps are tight.
Check the air cleaner housing for dents or
damage which could lead to a leak. Inspect the air
transfer tubing from the air cleaner to the
compressor and the engine for leaks.
Make sure that all clamps and flange joints are
tight.
GAUGES
The instruments or gauges are essential for
safety, maximum productivity and long service life
of the machine. Inspect the gauges prior to start-
up. During operation observe the gauges for
proper
functioning.
Refer
to
Operating
Instructions, for the normal readings.
COMPRESSOR OIL COOLER
The compressor lubricating and cooling oil is
cooled by means of a fin and tube-type oil cooler.
The lubricating and cooling oil, flowing internally
through the core section, is cooled by the air
stream from the cooling fan flowing past the core
section. When grease, oil and dirt accumulate on
the exterior surfaces of the oil cooler, its efficiency
is impaired.
Each month it is recommended that the oil
coolers be cleaned by directing compressed air
which contains a nonflammable safety solvent
through the core of the oil cooler. This should
remove the accumulation of grease, oil and dirt
from the exterior surfaces of the oil cooler cores
so that the entire cooling area can transmit the
heat of the lubricating and cooling oil to the air
stream.
In the event foreign deposits, such as sludge and
lacquer, accumulate in the oil coolers to the
extent that cooling efficiency is impaired, a
resulting high discharge air temperature is likely
to occur, causing shut down of the unit.
To correct this situation it will be necessary to
clean the coolers using a cleaning compound in
accordance
with
the
manufacturer’s
recommendations.
HOSES
Each month it is recommended that all of the intake
lines to and from the air cleaners and flexible hoses
used for air and oil be inspected.
To ensure freedom from air leaks, all rubber hose
joints and the screw-type hose clamps must be
absolutely tight. Regular inspection of these
connections for wear or deterioration is necessary.
Premature wear of the compressor is ASSURED
whenever dust-laden air is permitted to enter the
compressor intake.
The flexible hoses used in the oil and air lines on
these units are primarily used for their ability to
accommodate
relative
movement
between
components. It is important they be periodically
inspected for wear and deterioration. It is also
important the operator does not use the hoses as
convenient hand holds or steps. Such use can cause
early cover wear and hose failure.
Summary of Contents for XHP900CM
Page 9: ...Manual No 54771142 7 01 9 07 18 01 SAFETY CARD...
Page 15: ...Manual No 54771142 7 01 15 07 18 01 fold...
Page 42: ...xhp900cm doc 42 7 18 2001...
Page 48: ...xhp900cm doc 48 7 18 2001...
Page 49: ...xhp900cm doc 49 7 18 2001...
Page 50: ...xhp900cm doc 50 7 18 2001...
Page 62: ...xhp900cm doc 62 7 18 2001...
Page 63: ...xhp900cm doc 63 7 18 2001...
Page 64: ...xhp900cm doc 64 7 18 2001...
Page 72: ...xhp900cm doc 72 7 18 2001 ITEM PART NUMBER DESCRIPTION A 36527810 I R Signature 1 ea Side A...
Page 76: ......
Page 77: ...xhp900cm doc 77 07 18 01...