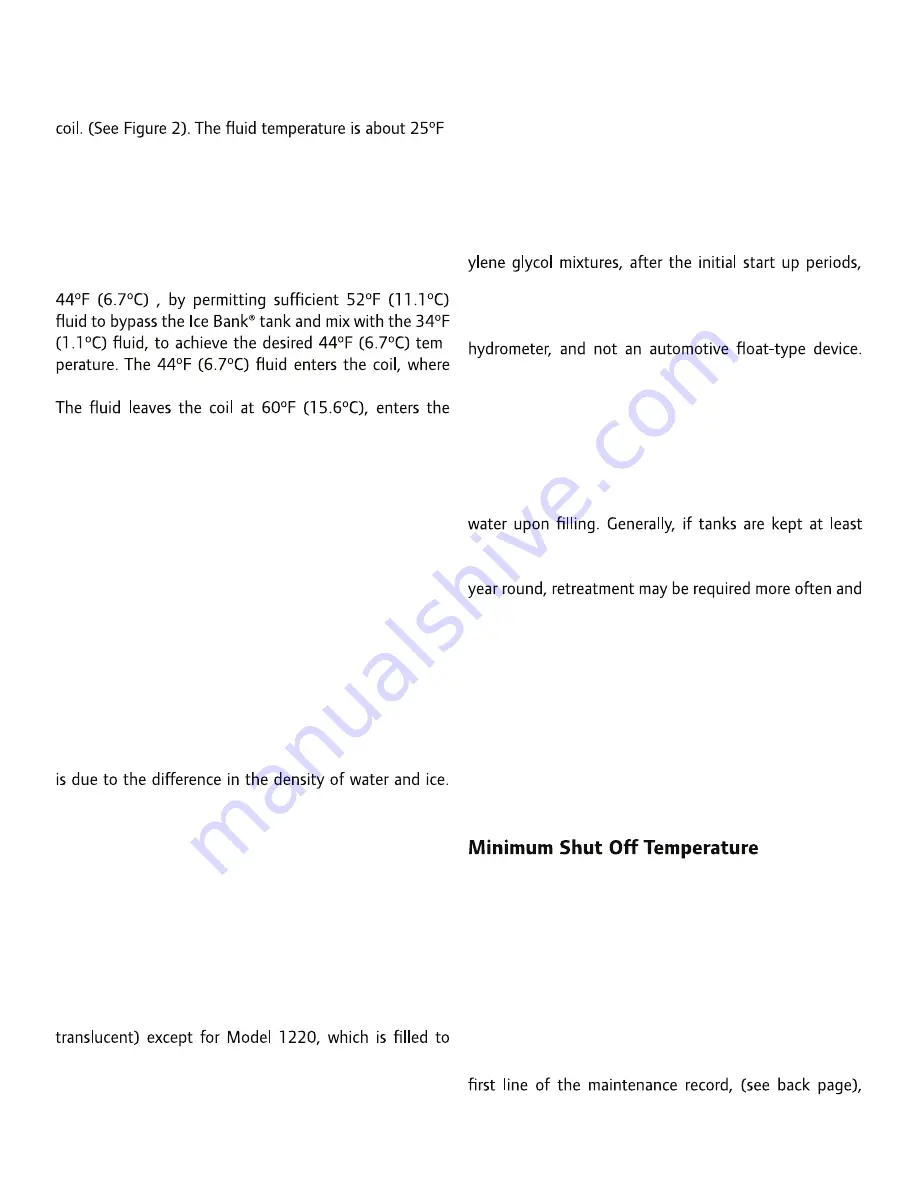
In a standard installation, ice is made at night. The
water-glycol solution circulates through the chiller and
the Ice Bank® heat exchanger, bypassing the air handler
(-3.9ºC) and the water surrounding the heat exchanger
freezes.
During the day, the glycol solution is cooled by the
IceBank® tank from approximately 52ºF to 34ºF (11ºC to
1ºC). (See Figure 3). A temperature modulating valve is
used to maintain a blended supply temperature typically
-
it cools air ordinarily from 75ºF to 55ºF (24ºC to 13ºC).
chiller and is cooled to 52ºF (11.1ºC). In some systems,
the ice will handle the entire day time load (Full Storage)
and in others, the ice will help a smaller than full size
chiller meet the load (Partial Storage).
MAINTENANCE
Since there are no moving parts in our standard thermal
storage tanks, the list of maintenance items is short. The
items we do list are important and should be done at
regular intervals as indicated. The inspection port cover
must always be replaced.
Water Level
The water level in the tank will rise and fall 2.5 to 7.8
inches (63 to 195mm) (depending on Model No. of
tank) during the charge and discharge cycle. This change
Water expands approximately 9% when changing to ice
at 32ºF (0ºC); therefore, during the freezing process,
the level will rise. (More about this in later sections).
The water stays in the tank (it is NOT pumped through
the system) and the amount of water/ice in the tank
remains constant except for possibly a slight amount of
evaporation, which normally occurs in outdoor, very hot,
dry climates.
The water level should be just covering the top heat
exchanger tube, (which is
5/8
" (16mm) diameter and
the bottom of the top HX tube. This measurement must
be done with no ice in the tank. The water level should
be checked every year except in hot, dry climates when
every three months is recommended.
Inventory Meter Calibration
During operation the only time to accurately check that
the the inventory meter probe level is correct is when
the tank is 100% charged. (See Ice Inventory Meter
Manual IB-153 for more information.)
Coolant Concentration
The coolant should be checked regularly in accordance
with the manufacturer’s recommendations. For eth-
a sample should be sent once a year to the manufac-
turer for analysis. Checking the coolant’s freeze point
is recommended twice a year using a refractometer or
The maximum freezing point for our system is normally
12ºF (-11.1ºC) (25%EG/H2O); however, some jobs
require lower freeze points because of particular oper-
ating conditions.
Storage Tank Water Treatment
Pour in the initial treatment of biocide into the tank
partially frozen year round, provide retreatment with
biocide as needed. However, if tanks are not kept frozen
the tanks should be checked for slime or odor season-
ally. At the end of the cooling season, you should fully
charge the tanks and leave them frozen until the start of
your next air-conditioning season. This will help to con-
trol biological growth. CALMAC® recommends a 20%
Tetrakis hydroxymethyl phosphonium sulfate solution
such as Aquacar PS20. All tank models require 16 oz. of
biocide solution per tank.
The CAS number is 555-66-30-8
In most systems, the termination of the charge cycle is
determined by the temperature of the coolant leaving
the storage tanks. Typically this temperature is in the
range of 27-28ºF (-2.7 to -2.2ºC). However, it is imper-
ative that the actual temperature be calculated for each
system using CALMAC Performance Data (IB-102).
This temperature is calculated by adding Coolant
Temperature Rise to the minimum Charging Coolant
Temperature. This temperature should be entered in the
and checked once every six months.