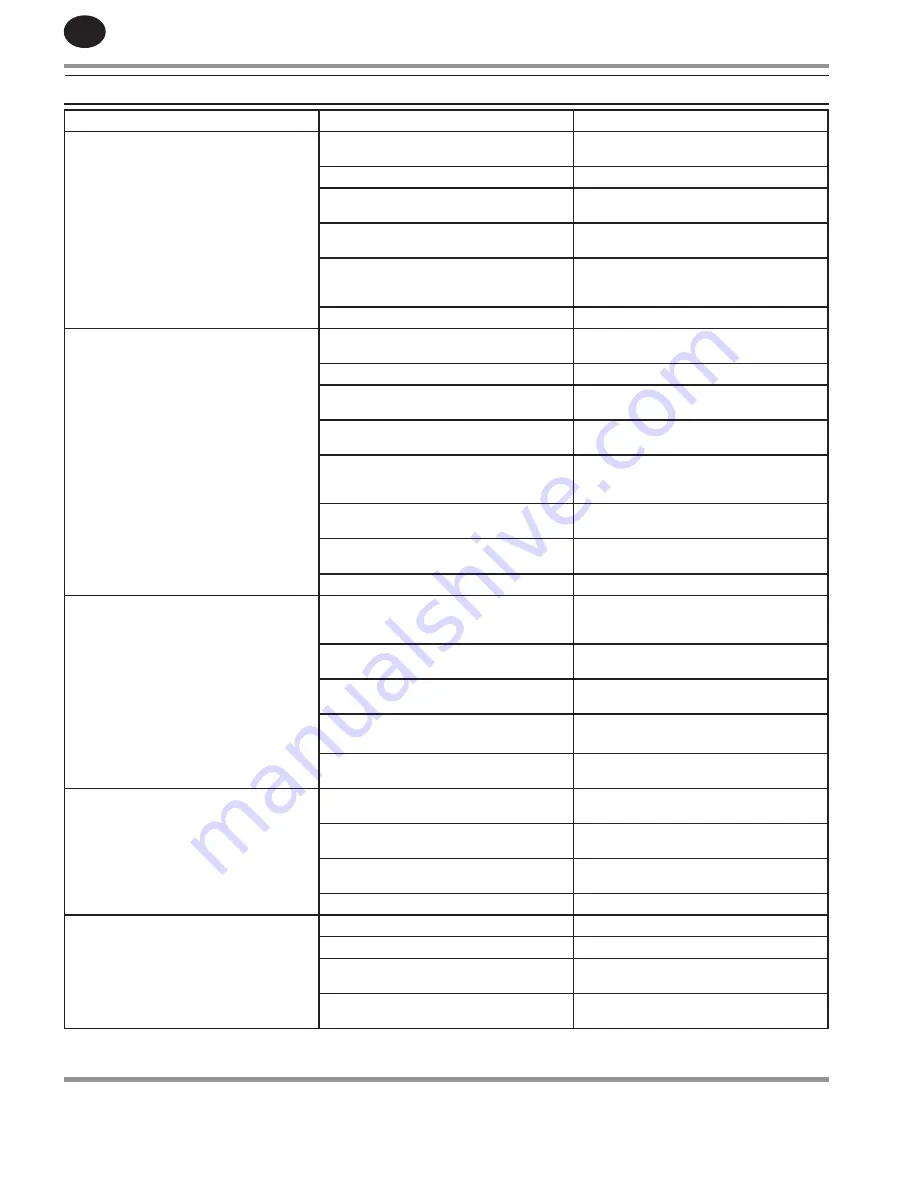
EN-12 22204945 Rev C
EN
TROUBLESHOOTING
PROBLEM
POSSIBLE CAUSE
POSSIBLE SOLUTION
Abnormal piston, ring or cylinder wear.
Lubricant viscosity too low
Drain existing lubricant and refill with proper
lubricant.
Lubricant level too low
Add lubricant to crankcase to proper level.
Detergent type lubricant being used
Drain existing lubricant and refill with proper
lubricant
Cylinder(s) or piston(s) scratched worn or
scored.
Repair or replace as required
Extremely dusty atmosphere.
Install remote air inlet piping and route to
source of cleaner air. Install more effective
filtration.
Worn cylinder finish
Deglaze cylinder with 180 grit flex-hone.
Air delivery drops off
Clogged or dirty inlet and / or discharge line
filter
Clean or replace
Air leaks in air discharge piping.
Check tubing and connections.
Lubricant viscosity too high.
Drain existing lubricant and refill with proper
lubricant.
Compressor valves leaky, broken, carbonized
or loose.
Inspect valves. Clean or replace as required.
Install valve kit.
Piston rings damaged or worn (broken, rough
or scratched). Excessive end gap or side
clearance.
Install ring kit.
Piston rings not seated, are stuck in grooves
or end gaps not staggered.
Adjust piston rings
Cylinder(s) or piston(s) scratched, worn or
scored.
Repair or replace as required
Defective safety/relief valve.
Replace
Unit does not come up to speed
Loose beltwheel or motor pulley, excessive
end play in motor shaft or loose drive belts.
Check beltwheel, motor pulley, crankshaft,
drive belt tension and alignment. Repair or
replace as required.
Lubricant viscosity too high
Drain existing lubricant and refill with proper
lubricant.
Improper line voltage
Check line voltage and upgrade lines as
required. Contact electrician.
Compressor valves leaky, broken, carbonized
or loose.
Inspect valves. Clean or replace as required.
Install valve kit.
Defective ball bearings on crankshaft or
motor shaft.
Inspect bearings and replace crankshaft
assembly if required.
Unit is slow to come up to speed
Lubricant viscosity too high
Drain existing lubricant and refill with proper
lubricant.
Leaking check valve or check valve seat
blown out.
Replace check valve.
Ambient temperature too low.
Relocate unit to warmer environment. Install
crankcase heater kit.
Bad motor.
Replace.
Unit runs excessively hot
Inadequate ventilation around beltwheel.
Relocate unit for better air flow
Drive belts too tight or misaligned
Adjust belts to proper tension and alignment.
Compressor valves leaky, broken, carbonized
or loose
Inspect valves. Clean or replace as required.
Install valve kit.
Wrong beltwheel direction of rotation
Check motor wiring for proper connections.
Reverse two leads on three-phase motors.
RELEASED 05/Apr/2018 15:16:08 GMT