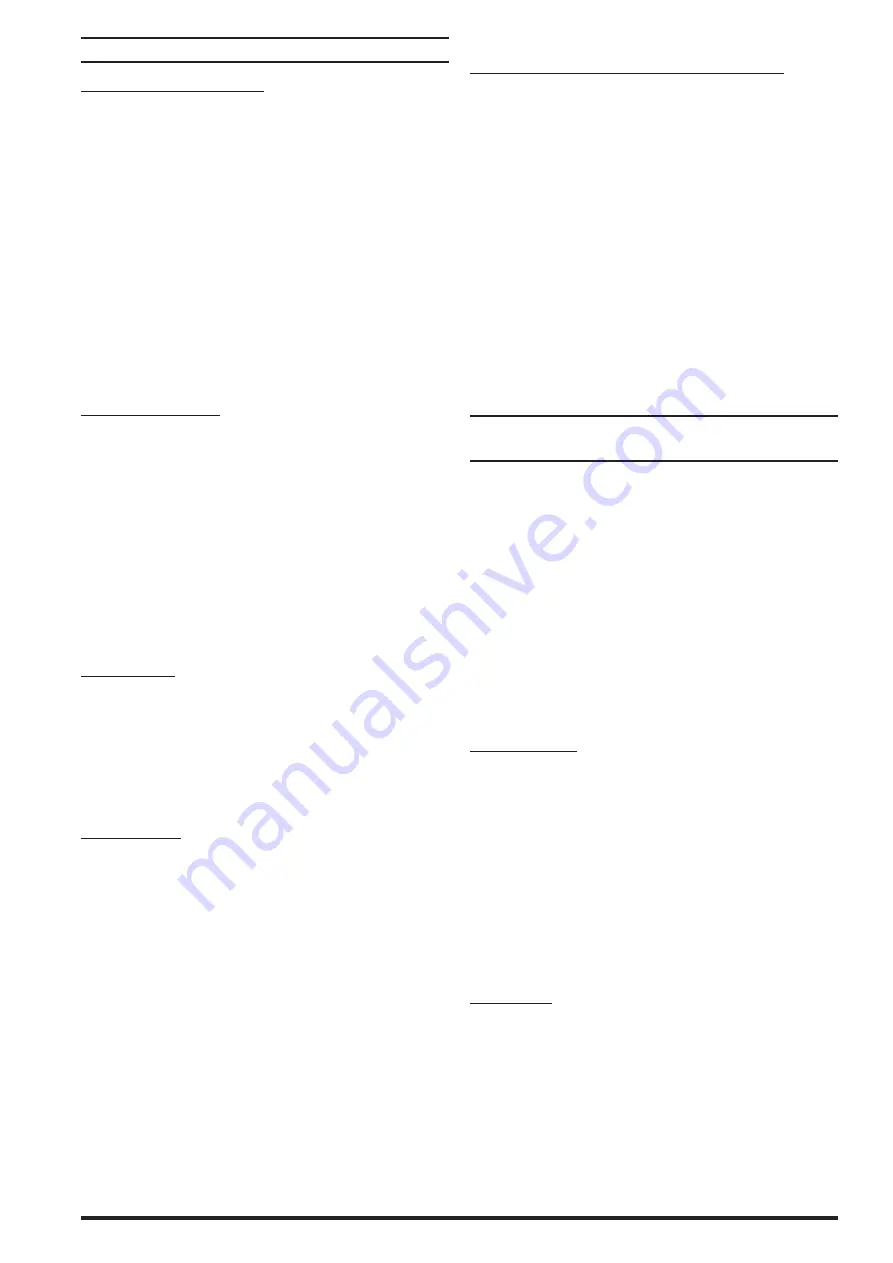
CHEMFLO 8 (en)
Page 7 of 16
SEAL REPLACEMENT INSTRUCTIONS
DISASSEMBLE THE PUMP:
Drain the system of liquid, break suction and discharge pipe
unions, and, if necessary, remove all piping from the suction
and discharge openings. Remove the fasteners holding the
pump adaptor to the driver, loosen the drive clamp assembly,
and remove the PUMPAK.
To disassemble, remove the washers and hexnuts holding the
motor adaptor to the housing. Remove the housing. The im-
peller, drive sleeve, seal bellows, and the spring assembly will
now slide forward Free of the pump adapter.
The seal seat and seat cup will remain in the pump adaptor.
If not damaged or worn, do not remove. If necessary, remove
from the adaptor counter bore with a piece of wood or a
screwdriver handle inserted through the adaptor from the
drive end. A sharp tap or two is usually sufficient to knock out
the seal seat. Use caution in removing the seal seat so as not
to crack a ceramic seat.
REMOVE IMPELLER
Remove seal bellows and spring assembly. On some models,
spring keeper can also be removed now before removing im-
peller.
NOTE
: The seal bellows will be bonded to the shaft sleeve
and will require some patience and caution in removal in or-
der not to damage the seal bellow and cage.
MP Pumps rebuild kits include a new drive sleeve to avoid the
possibility of damaging the drive sleeve. See back of manual
for list of seal kits and corresponding rebuild kits. Impellers
are also available if wear or damage is present.
Remove locknut from shaft; unscrew the impeller from the
shaft sleeve counter-clockwise from the impeller end.
INSPECTION:
Check all parts for wear. For ease of reassembly shaft sleeve
should have all nicks and burrs removed. Clean with light cro-
cus cloth. Replace damaged parts with new parts.
Inspect the seal seat and washer, seat cup, and seal bellows
for grooves, cuts, scuffmarks, or other deterioration. If any of
the parts are damaged, a complete new assembly should be
installed.
REASSEMBLY:
All dirt and foreign matter should be removed. Recommend
only using new seals and elastomers when reassembling a
pump.
Lubricate seal seat cup with liquid soap (P-80 emulsifier) or
clean grease and press seal seat into adaptor counter bore,
seating it firmly and squarely. Use caution so as not to mar
the lapped face of the seal seat.
Assemble shaft sleeve; seal spring keeper, impeller and im-
peller nut. Before installing seal bellows and spring assembly,
lubricate the shaft sleeve and rubber bellows with liquid soap
(P-80 emulsifier) or clean grease and press bellows and spring
assembly onto the shaft sleeve. The spring should engage
the spring keeper at the impeller end of the shaft sleeve.
To be properly positioned the washer must be firmly against
the rubber bellows member and the driving lugs of the wash-
er properly engaged. The raised shoulder on the seal wash-
er should be facing away from the impeller to contact the
lapped surface of the seal seat in the adaptor.
Slide impeller and seal assembly into the adaptor. Install drive
clamp assembly on the shaft sleeve but do not tighten.
INSTRUCTIONS FOR SET SCREW TYPE SEAL:
Do not remove the seal retaining clips. Slide the seal into
place on the shaft. The end of the shaft will be recessed ap-
proximately .080” ±.020” from the end of the seal. The proper
seal working height is achieved when the seal faces are set
flush with the seal clips in place.
With the seal clips still in place tighten the seal fasteners with
a ball end allen wrench. It is important that the allen wrench
not rest upon the seal housing during tightening as this may
affect the position of the seal on the shaft. After the seal fas-
teners have been tightened the seal clips should be removed
and saved.
Do not use the seal shim with setscrew type seal.
For bellows seal install the seal spacer on the backside of the
impeller. Use a light grease or similar tacky material. Thread
impeller onto shaft. Install jam nut. Place o-ring onto seal
plate. Install impeller/bearing housing assembly into pump
housing. Install lock washers and hex nuts. Rotate the shaft
several times to check for rubbing or binding.
BEARING REPLACEMENT INSTRUCTIONS
(PEDESTAL MODELS)
The pump utilizes a single self-adjusting type mechanical seal
that is lubricated and cooled by the liquid in the pump.
THE PUMP MUST NEVER BE OPERATED WITHOUT LIQUID
IN THE HOUSING.
Check rotation of the driver to be sure it coincides with the
required rotation of the pump. When viewed from the driver
end the rotation of the pump is CLOCKWISE.
The pump’s grease lubricated bearings are sealed. They have
been pre-lubricated at the factory and require no further
lubrication or maintenance for the life of the bearing. Electric
motors or other rotating equipment used to drive the pump
should be lubricated in accordance with the manufacturer’s
instructions.
DISASSEMBLY:
Drain the housing by removing the drain plug. Remove the
hex nuts and lock washers from the housing studs. Slide the
bearing housing/impeller assembly out of the housing, it
may be necessary to rotate the driver shaft out of the way.
With the bearing /impeller assembly on a bench secure shaft,
unthread impeller nut then unthread impeller. Remove the
seal from the shaft. Lift off the seal plate. Place the seal plate
face down on the bench and press the seal seat out. Remove
the snap ring from the backside of the bearing housing. With
a soft mallet, loosen the shaft assembly by tapping the impel-
ler end then slide the bearing assembly from the housing.
Press the bearings from the shaft.
ASSEMBLY:
Press bearings onto the shaft. Slide the shaft / bearing assem-
bly into the bearing housing and install the snap ring. Place
seal housing face up on bench. Lubricate non-PTFE seal seat
with water-soluble lubricant and gently press into seal hous-
ing. If pinned seat is used be certain that pin is in place, lined
up with groove in seal seat. Place seal housing onto pilot of
bearing housing. Lubricate shaft with water-soluble lubricant.
Slide seal onto shaft.
RELEASED 03/Sep/2021 12:38:59 GMT