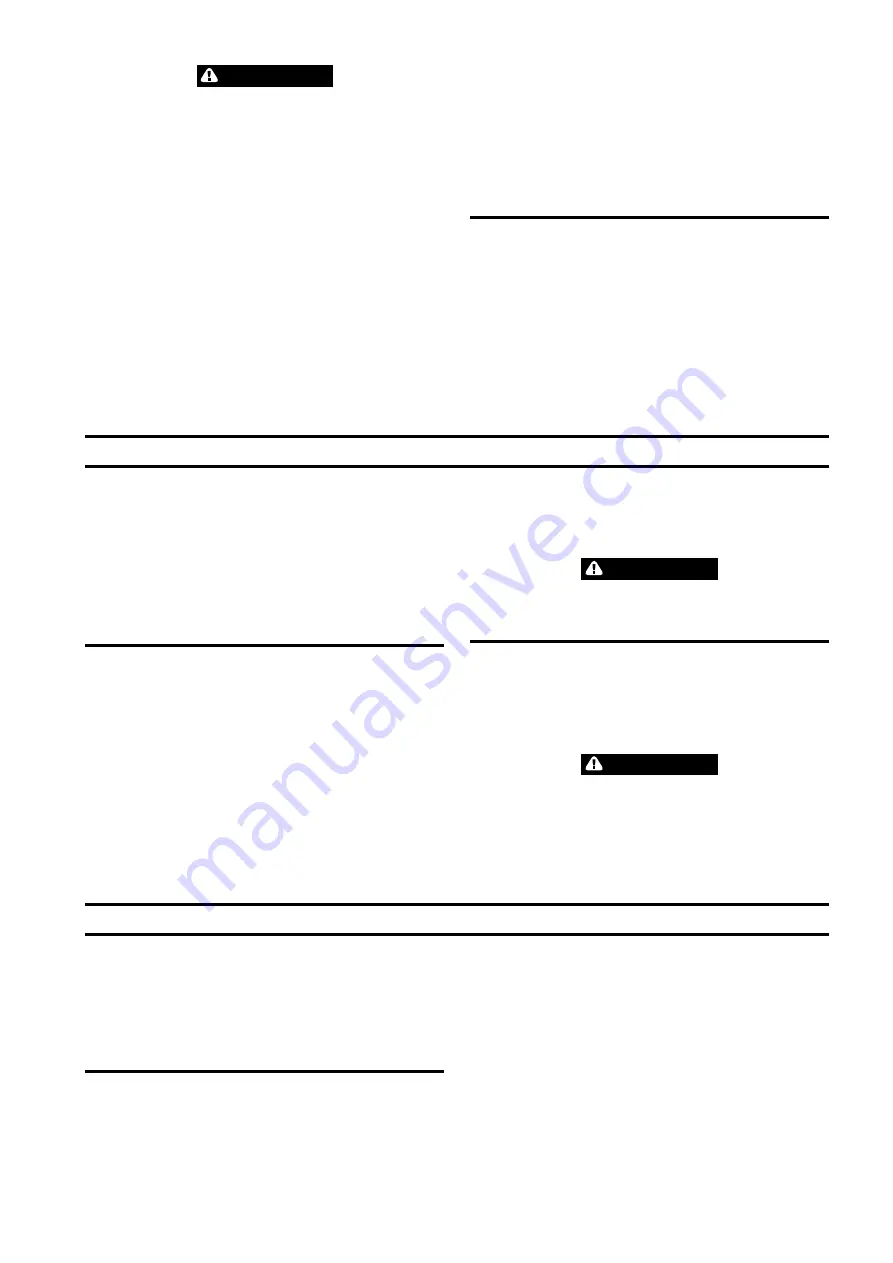
CAUTION
•
Shut off air supply before filling air line lubricator.
•
Lubricator must be located no more than 10 ft (3 m) from the motor.
•
The air line lubricator should be replenished daily and set to provide
lubrication at a minimum rate of 1 to 3 drops per minute, and adjusted at
maximum hoist speed. Use of SAE 10W oil or a good grade of hydraulic oil
is recommended. A fine mist will be exhausted from the throttle control
valve when the air line lubricator is functioning properly.
•
Do not use automotive type detergent oil. Detergents will delaminate the
motor vanes and cause premature failure.
n
Air Line Filter
It is recommended that an air line strainer/filter be installed as close as practical to
the motor air inlet port to prevent dirt from entering the motor. The strainer/filter
should provide 10 micron filtration and include a moisture trap. Clean the strainer/
filter monthly to maintain its operating efficiency.
n
Moisture in Air Lines
Moisture that reaches the air motor through the supply lines is a primary factor in
determining the length of time between service overhauls. Moisture traps can help
to eliminate moisture. Other methods, such as an air receiver which collects moisture
before it reaches the motor or an aftercooler at the compressor that cools the air
prior to distribution through the supply lines, are also helpful.
The inlet strainer (42) must be installed on the hoist. Failure to do so may result in a
hoist malfunction. The bleed adjustment screws (35 or 336) used on hoists with a
pendent control are factory adjusted to provide optimum control at 90 psig
(6.3 bar/630 kPa) air pressure. If the hoist is used with other air supply pressures, the
bleed adjustment screws may require readjustment.
n
Adjustment of Bleed Screws on Pendent Control Models
For maximum performance and control, adjust the bleed screws (35 or 336) as
follows:
1. Loosen the adjustment screw locknut (36 or 337).
2. Back out the adjustment screw (35 or 336) approximately one third (1/3) of a
turn.
3. While fully depressing the pendent throttle lever (205) and holding it in that
position, turn in the adjustment screw until the piston rod fully retracts. This
adjustment will provide a good balance of spotting control and maximum hoist
speed. If better spotting control is desired, slowly back out the adjustment screw
a little at a time until the spotting control is suitable.
4. Tighten the adjustment screw locknut (36 or 337).
n
Storing the Hoist
1. Always store the hoist in a no load condition.
2. Wipe off all dirt and water.
3. Oil the chain, hook pins and hook latch.
4. Place in a dry location.
5. Plug hoist air inlet port.
6. Before returning hoist to service, follow instructions for ‘Hoists Not In Regular
Use‘. Refer to the “INSPECTION” section on page 5.
OPERATION
The four most important aspects of hoist operation are:
1. Follow all safety instructions when operating hoist.
2. Allow only people trained in safety and operation on this product to operate
hoist.
3. Subject each hoist to a regular inspection and maintenance program.
4. Be aware of hoist capacity and weight of load at all times. Ensure load does not
exceed hoist or rigging ratings.
Operators must be physically competent. Operators must have no health condition
which might affect their ability to act, and they must have good hearing, vision and
depth perception. The hoist operator must be carefully instructed in his duties and
must understand the operation of the hoist, including a study of the manufacturer’s
literature. The operator must thoroughly understand proper methods of hitching
loads and should have a good attitude regarding safety. It is the operator’s
responsibility to refuse to operate the hoist under unsafe conditions.
n
Initial Operating Checks
Hoists are tested for proper operation prior to leaving the factory. Before the hoist
is placed into service the following initial operating checks should be performed.
1. After installation of trolley mounted hoists, check to ensure the hoist is centered
below the trolley.
2. Check for air leaks in the supply hose and fittings to pendant, and from pendant
to manifold.
3. When first running the hoist or trolley motors some light oil should be injected
into the inlet connection to allow good lubrication.
4. When first operating the hoist and trolley it is recommended that the motors be
driven slowly in both directions for a few minutes.
5. Operate the trolley along the entire length of the beam.
6. Inspect hoist and trolley performance when raising, moving and lowering test
load(s). Hoist and trolley must operate smoothly and at rated specifications prior
to being placed in service.
7. Check that trolley (if equipped) and hook movement is the same direction as
arrows or information on the pendant control.
8. Raise and lower a light load to check operation of the hoist brake.
9. Check hoist operation by raising and lowering a load equal to the rated capacity
of the hoist a few inches (cm) off the floor.
10. Check operation of limit devices.
11. Check to see that the hoist is directly over the load. Do not lift the load at an
angle (side pull or “ yard ”).
12. Check to see that the hoist is securely connected to the overhead crane,
monorail, trolley or supporting member.
13. Check to see that the load is securely inserted in the hook, and that the hook
latch is engaged.
WARNING
•
Only allow personnel trained in safety and operation of this product to
operate the hoist and trolley.
•
This Hoist is not designed or suitable for lifting, lowering or moving
persons. Never lift loads over people.
n
Hoist Controls
n
Two Lever Pendant
Refer to Dwg. MHP0427 on page 7, A. Lower Load; B. Raise Load;
A two lever pendant provides operation of the hoist. For units with powered trolleys
a four lever pendant is required.
WARNING
•
The hook latch is intended to retain loose slings or devices under slack
conditions. Hook latches are not intended to be an anti-fouling device, so
caution must be used to prevent the latch from supporting any of the load.
Refer to Form P6778 for information on Pendant Throttle Handle Assemblies for two
and three motor functions.
INSPECTION
There are two types of inspection, the frequent inspection performed by the
operator and periodic inspections performed by personnel trained in the operation
and repair of this hoist.
Careful inspection on a regular basis will reveal potentially dangerous conditions
while still in the early stages, allowing corrective actions to be taken before the
condition becomes dangerous.
Any deficiency revealed through inspection must be reported to an appointed
person. A determination must be made as to whether a deficiency constitutes a
safety hazard before resuming operation of the hoist.
n
Frequent Inspection
On hoists in continuous service, frequent inspection should be made at the
beginning of each shift. In addition, visual inspections should be conducted during
regular service for any damage or evidence of malfunction.
1.
Operation. Check for visual signs or abnormal noises (grinding etc.) which could
indicate a potential problem. Make sure all controls function properly and return
to neutral when released. Check chain feed through the hoist and bottom block.
If chain binds, jumps, is excessively noisy or “clicks”, clean and lubricate the chain.
If problem persists, replace the chain. Do not operate the hoist until all problems
have been corrected.
2.
Hooks. Check for wear or damage, increased throat width, bent shank or twisting
of the hook. Check hooks swivel freely. Replace hooks which exceed the throat
opening. Refer to Dwg. MHP0040 on page 7, A. Throat Width. Replace hooks
which exceed a 10° twist. Refer to Dwg. MHP0111 on page 7, A. Twisted DO
NOT USE; B. Normal Can Be Used. Refer to the latest edition of ASME B30.10
‘HOOKS‘ for additional information. Refer to Product Maintenance Information
Manual.
Form 47112677 Edition 2
5