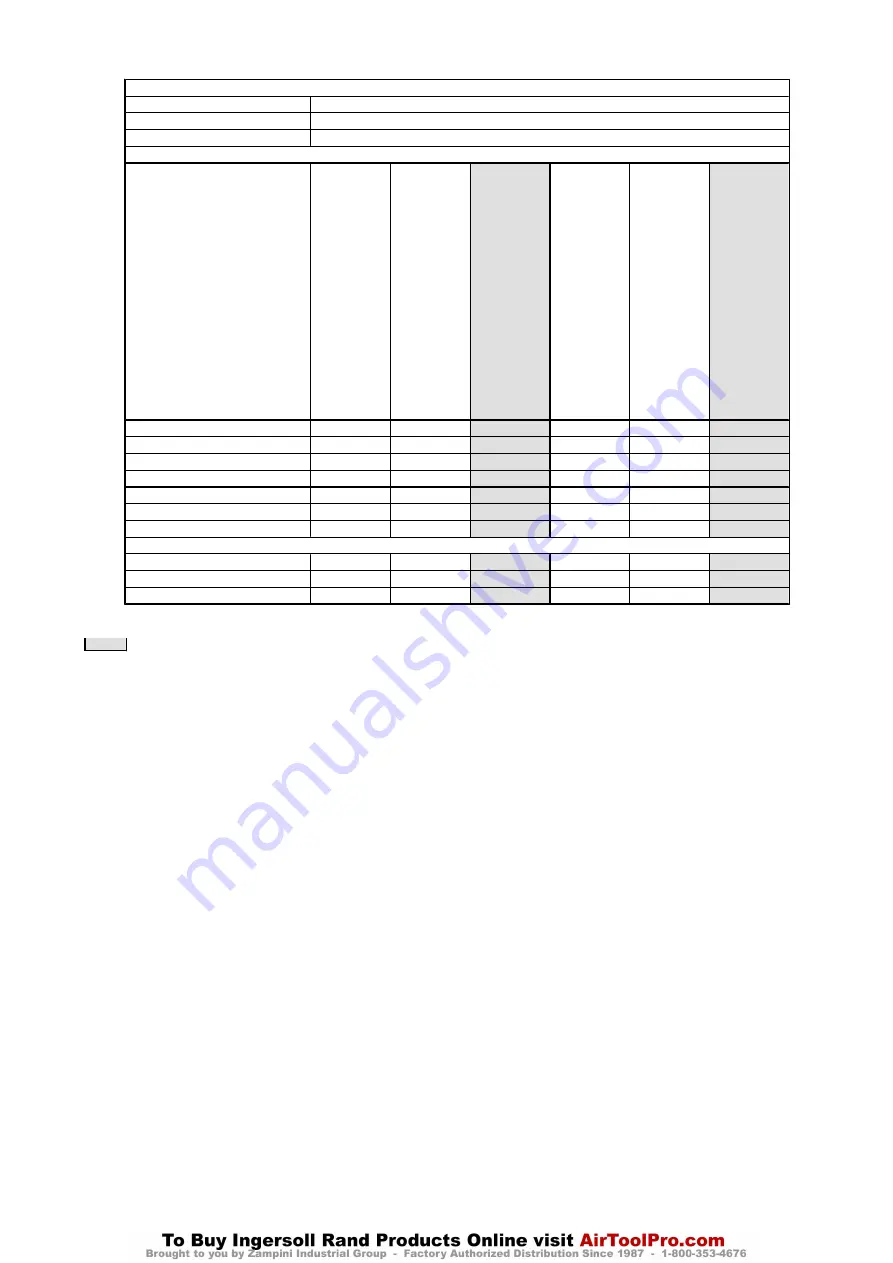
Table 3: Decoking Winch Maintenance Interval Chart
The following work can be completed by owner maintenance personnel
System Air Filter
Inspect system air filter every 30 days or 100 hours
Grease Fittings
Lubricate grease fittings every 90 days or 250 hours
Gearbox Oil Level
Check oil level in gearbox every 90 days or 250 hours
It is recommended that the following work be completed by a trained Ingersoll Rand trained service technician.
Standard Components
1 year or
1,000 hrs
2 years or
2,000 hrs
3 years or
3,000 hrs
4 years or
4,000 hrs
5 years or
5,000 hrs
6 years or
6,000 hrs
Inspect Motor
X
X
Inspect Manual Band Brake
X
X
X
X
X
X
Inspect Disc Brake
X
X
Inspect Gearbox
X
X
Replace Winch Anchor Bolts
X
X
Rebuild Control Valve
X
X
Inspect Drum, Housings and Main Frames
X
X
X
X
X
X
Optional Components
Emergency Shut-Off Valve
X
X
X
X
X
X
Limit Switches
X
X
X
X
X
X
Automatic Band Brake *
X
X
X
X
X
X
*
Do not disassemble band brake air cylinder unless brake operation or visual inspection indicates a requirement.
NOTE: Hours are for actual winch drum rotation.
Recommend complete general overhaul.
Form MHD56375 Edition 2
3
Summary of Contents for FH5i-DCOKER
Page 11: ...Form MHD56375 Edition 2 11...
Page 12: ...www ingersollrandproducts com...