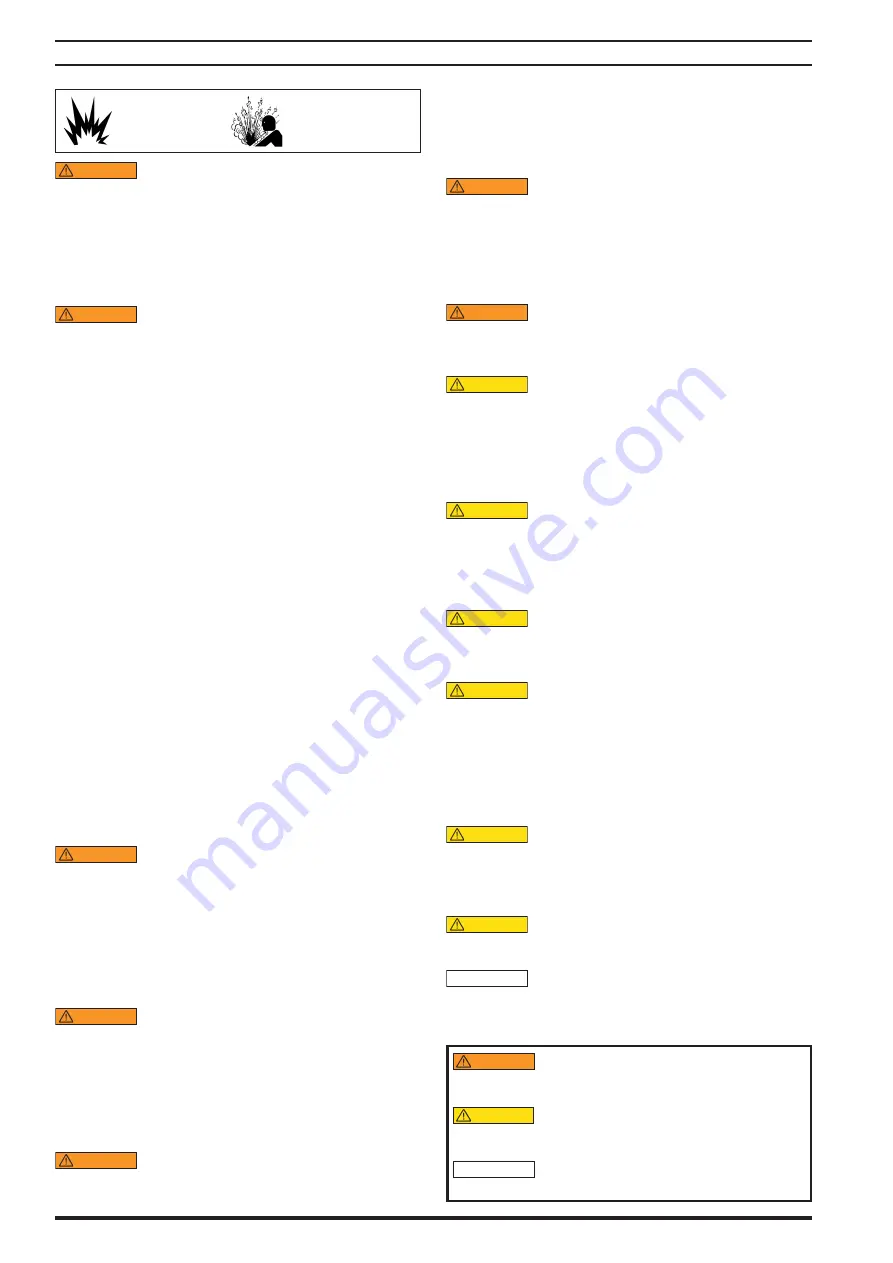
Page 2 of 8
PW10A-XXX-XXX-A (en)
WARNING
EXCESSIVE AIR PRESSURE. Can cause per-
sonal injury, pump damage or property damage.
y
Do not exceed the maximum inlet air pressure as
stated on the pump model plate.
y
Be sure material hoses and other components are able
to withstand fluid pressures developed by this pump.
Check all hoses for damage or wear. Be certain dispens-
ing device is clean and in proper working condition.
WARNING
STATIC SPARK. Can cause explosion re-
sulting in severe injury or death. Ground pump and
pumping system.
y
Sparks can ignite flammable material and vapors.
y
The pumping system and object being sprayed must
be grounded when it is pumping, flushing, recirculat-
ing or spraying flammable materials such as paints,
solvents, lacquers, etc. or used in a location where
surrounding atmosphere is conducive to spontaneous
combustion. Ground the dispensing valve or device,
containers, hoses and any object to which material is
being pumped.
y
Secure pump, connections and all contact points to
avoid vibration and generation of contact or static
spark.
y
Consult local building codes and electrical codes for
specific grounding requirements.
y
After grounding, periodically verify continuity of
electrical path to ground. Test with an ohmmeter from
each component (e.g., hoses, pump, clamps, contain-
er, spray gun, etc.) to ground, to ensure continuity.
Ohmmeter should show 0.1 ohms or less.
y
Submerse the outlet hose end, dispensing valve or
device in the material being dispensed if possible.
(Avoid free streaming of material being dispensed.)
y
Use hoses incorporating a static wire.
y
Use proper ventilation.
y
Keep inflammables away from heat, open flames and
sparks.
y
Keep containers closed when not in use.
WARNING
Pump exhaust may contain contaminants.
Can cause severe injury. Pipe exhaust away from work
area and personnel.
y
In the event of a diaphragm rupture, material can be
forced out of the air exhaust muffler.
y
Pipe the exhaust to a safe remote location when
pumping hazardous or inflammable materials.
y
Use a grounded 3/8” minimum ID hose between the
pump and the muffler.
WARNING
HAZARDOUS PRESSURE. Can result in se-
rious injury or property damage. Do not service or
clean pump, hoses or dispensing valve while the sys-
tem is pressurized.
y
Disconnect air supply line and relieve pressure from
the system by opening dispensing valve or device and
/ or carefully and slowly loosening and removing out-
let hose or piping from pump.
WARNING
HAZARDOUS MATERIALS. Can cause serious
injury or property damage. Do not attempt to return
a pump to the factory or service center that contains
OPERATING AND SAFETY PRECAUTIONS
READ, UNDERSTAND AND FOLLOW THIS INFORMATION TO AVOID INJURY AND PROPERTY DAMAGE.
hazardous material. Safe handling practices must
comply with local and national laws and safety code
requirements.
y
Obtain Material Safety Data Sheets on all materials
from the supplier for proper handling instructions.
WARNING
EXPLOSION HAZARD. Models containing alu-
minum wetted parts cannot be used with 1,1,1-trichlo-
roethane, methylene chloride or other halogenated
hydrocarbon solvents which may react and explode.
y
Check pump motor section, fluid caps, manifolds and
all wetted parts to assure compatibility before using
with solvents of this type.
WARNING
MISAPPLICATION HAZARD. Do not use mod-
els containing aluminum wetted parts with food prod-
ucts for human consumption. Plated parts can contain
trace amounts of lead.
CAUTION
Verify the chemical compatibility of the
pump wetted parts and the substance being pumped,
flushed or recirculated. Chemical compatibility may
change with temperature and concentration of the
chemical(s) within the substances being pumped,
flushed or circulated. For specific fluid compatibility,
consult the chemical manufacturer.
CAUTION
Maximum temperatures are based on me-
chanical stress only. Certain chemicals will signifi-
cantly reduce maximum safe operating temperature.
Consult the chemical manufacturer for chemical com-
patibility and temperature limits. Refer to PUMP DATA
on page 1 of this manual.
CAUTION
Be certain all operators of this equipment
have been trained for safe working practices, under-
stand it’s limitations, and wear safety goggles / equip-
ment when required.
CAUTION
Do not use the pump for the structural sup-
port of the piping system. Be certain the system com-
ponents are properly supported to prevent stress on
the pump parts.
y
Suction and discharge connections should be flex-
ible connections (such as hose), not rigid piped,
and should be compatible with the substance being
pumped.
CAUTION
Prevent unnecessary damage to the pump.
Do not allow pump to operate when out of material
for long periods of time.
y
Disconnect air line from pump when system sits idle
for long periods of time.
CAUTION
Use only genuine ARO replacement parts to
assure compatible pressure rating and longest service
life.
NOTICE
RE-TORQUE ALL FASTENERS BEFOREOPER-
ATION. Creep of housing and gasket materials may
cause fasteners to loosen.Re-torque all fasteners to
ensure against fluid or air leakage
WARNING
= Hazards or unsafe practices which
could result in severe personal injury,
death or substantial property damage.
CAUTION
= Hazards or unsafe practices which
could result in minor personal injury,
product or property damage.
NOTICE
= Important installation, operation or
maintenance information.
EXCESSIVE AIR PRESSURE
STATIC SPARK
HAZARDOUS MATERIALS
HAZARDOUS PRESSURE