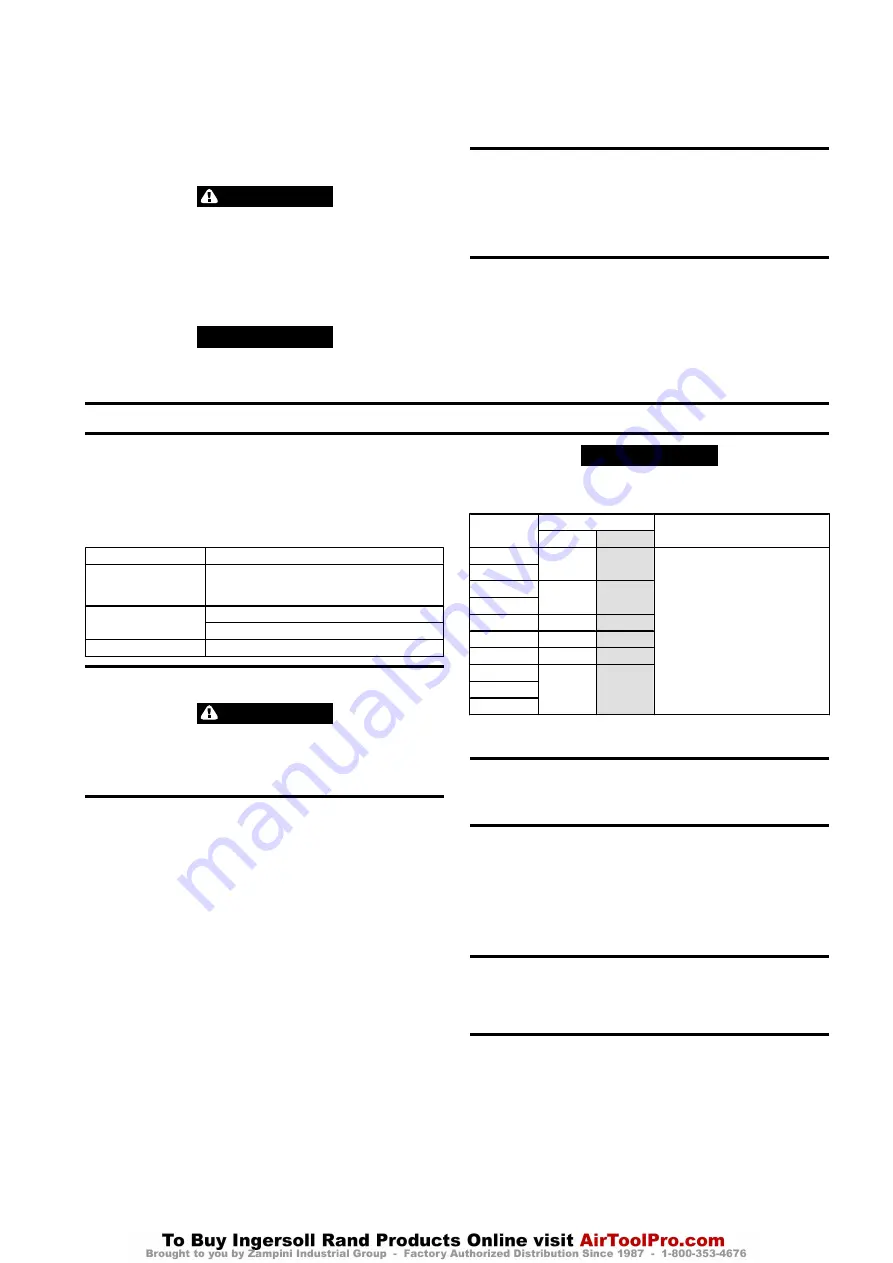
8.
Hooks. Check for wear or damage, increased throat width, bent shank or twisting
of the hook. Replace if hook latch snaps past tip of hook. Check hooks swivel
freely. Replace hooks which exceed the throat opening. Refer to Dwg. MHP0040
on page 11, A. Throat Width. Replace hooks which exceed a 10° twist. Refer to
Dwg. MHP0111 on page 11, A. Twisted DO NOT USE; B. Normal Can Be Used.
If hook latch snaps past tip of hook, the hook is sprung and must be replaced.
Refer to the latest edition of ASME B30.10 ‘HOOKS‘ for additional information.
Check hook support bearings for lubrication or damage. Ensure that they swivel
easily and smoothly. Refer to Product Maintenance Information Manual.
9.
Hook Latch. Make sure hook latch is present and not damaged. Replace if
necessary.
CAUTION
•
Do not use hoist if hook latch is missing or damaged.
10.
Load Chain. Examine each of the links for bending, cracks in weld areas or
shoulders, traverse nicks and gouges, weld splatter, corrosion pits, striation
(minute parallel lines) and chain wear, including bearing surfaces between chain
links. Refer to Dwg. MHP0102 on page 11, A. Diameter; B. Welded Area; C. Wear
in these areas. Visually inspect as much of the chain as is possible. Inspect for
wear, damage and corrosion. If damage is evident, do not operate hoist until the
damage has been reviewed and inspected further by an Ingersoll Rand trained
inspector. Refer to Product Maintenance Information Manual.
NOTICE
•
The full extent of chain wear cannot be determined by visual inspection. At
any indication of wear inspect chain in accordance with instructions in
‘Periodic Inspection‘. Refer to Product Maintenance Information Manual.
11.
Load Chain Reeving. Ensure welds on standing links are away from load sheave.
Reinstall chain if necessary. Refer to Product Maintenance Information Manual.
Make sure chain is not capsized, twisted or kinked. Adjust as required. Refer to
Dwg. MHP0043 in Product Safety Information Manual.
12.
Labels and Tags. Check for present and legibility of labels. Refer to Product Parts
information manual for correct labels and placement. Replace if damaged or
missing.
n
Load Chain Reports
Records should be maintained documenting condition of load chain removed from
service as part of a long-range chain inspection program. Accurate records will
establish a relationship between visual observations noted during ‘Frequent
Inspections‘ and actual condition of load chain as determined by ‘Periodic
Inspections‘. Refer to Product Maintenance Information Manual for chain
specifications.
n
Hoists Not in Regular Use
1. Equipment which has been idle for a period of one month or more, but less than
six months, shall be given an inspection conforming to the requirements of
“Frequent Inspection” section on page 6 before being placed in service.
2. Equipment which has been idle for a period of over six months shall be given a
complete inspection conforming with requirements of ‘Periodic
Inspection‘ before being placed in service. Refer to Product Maintenance
Information Manual.
3. Standby equipment shall be inspected at least semiannually in accordance with
requirements of ‘Frequent Inspection‘.
LUBRICATION
To ensure continued satisfactory operation of hoist, all points requiring lubrication
must be serviced with correct lubricant at proper time interval as indicated for each
assembly.
Refer to ‘Maintenance Interval’ chart in Product Maintenance Information Manual
for recommended lubrication intervals. Use only those lubricants recommended.
Other lubricants may affect product performance. Approval for use of other
lubricants must be obtained from your Ingersoll Rand distributor. Failure to observe
this precaution may result in damage to winch and/or its associated components.
INTERVAL
LUBRICATION CHECKS
Start of each shift
If used, check flow and level of air line lubricator
(approximately 2 to 3 drops per minute required at
maximum motor speed).
Monthly
Lubricate components supplied by grease fittings.
Inspect and clean or replace air line filter.
Yearly
Drain and refill hoist reduction gear oil.
n
General Lubrication
WARNING
•
Pneumatic Hoists use oil to prevent excessive heat build up and to prevent
wear that could cause sparks. Oil levels must be properly maintained.
Always collect lubricants in suitable containers and dispose of in an environmentally
safe manner.
n
Reduction Gear Assembly
Refer to Dwg. MHP3066 on page 11, A. Fill Plug; B. Drain Plug; C. Oil Level Plug.
Refer to Dwg. MHP3067 on page 11, A. Oil Fill / Level Plug.
Replace the oil in the reduction housing once every year. If the hoist is used at a
normal frequency, the oil in the reduction housing is suitable for one year's operation
without being changed. However, when the hoist is used at a high frequency, the
oil may need to be changed more often.
To ensure correct performance, highest efficiency and long life, it is essential that
the lubricating oil be maintained at the correct level. The recommended grade of
oil must be used at all times since the use of unsuitable oil may result in excessive
temperature rise, loss of efficiency and possible damage to the gears.
NOTICE
•
Only use synthetic oil.
Table 5: Reduction Gear Assembly Oil Type
Models
Capacity
Oil
oz
litres
LC2A015S
4.05
0.12
Mobil SHC629 ISO VG 150
LC2A030D
LC2A035S
10.82
0.32
LC2A040S
LC2A060S
10.14
0.30
LC2A060Q
4.05
0.12
LC2A080D
10.82
0.32
LC2A120D
10.14
0.30
LC2A180T
LC2A250Q
To replace oil remove fill plug and add oil to the reduction gear assembly, replace
plug. Refer to Product Parts Information Manual.
n
Seals and Bearings
If hoist is disassembled, clean all parts thoroughly and coat bearings and seals with
clean grease. Use sufficient grease to provide a good protective coat.
n
Hook Assemblies
Hoist top and bottom hooks are supported by thrust bearings. These bearings must
be packed with Ingersoll Rand No. 68 Grease or a standard No. 2 multi-purpose
grease at regular intervals. Neglect of proper lubrication can lead to bearing failure.
1. Lubricate hook and latch pivot points. Refer to Dwg. MHP1300 on page 11,
A. Hook latch pivot point. Hook and latch should swivel/pivot freely.
2. Use Ingersoll Rand LUBRI-LINK-GREEN® or ISO VG220 (SAE 50W) lubricant.
3. Lubricate hook bearings by applying several shots of grease from a grease gun
to the grease fittings provided on the hook blocks.
n
Air Line Lubricator
If an air line lubricator is used, set to provide 2 to 3 drops per minute and replenish
daily using ISO VG100 (SAE 30W) lubricant [minimum viscosity 135 Cst at 104°F
(40°C)].
n
Trolley (optional feature)
Grease wheel bearings and wheel drive gear with Ingersoll Rand No. 68 Grease or
a standard No. 2 multi-purpose grease periodically. Refer to manufacturer’s literature
for additional lubrication information.
Form MHD56296 Edition 5
7