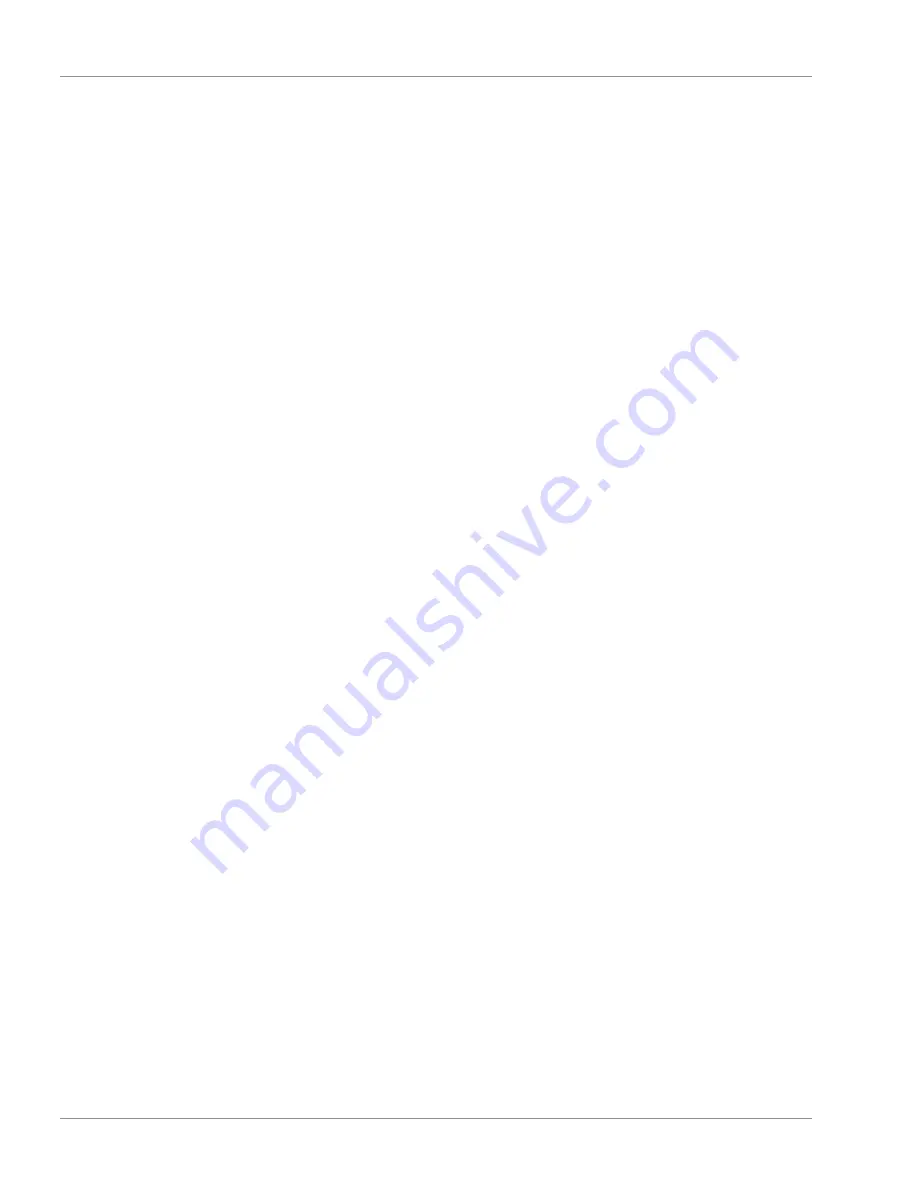
11 | Troubleshooting
INFICON
294 / 319
074-594-P1H Micro GC Fusion Operating Man-
ual
11.2.1.3 Peak Symptoms
11.2.1.3.1 No Peaks
No peaks are typically due to insufficient Sample Pump Time, low detector sensitivity,
or a short Inject (ms) time.
Verify if there is flow present by connecting a flow meter to the reference and
analytical vents on the back of each module. No flow could indicate a broken column.
The presence of flow could indicate an injector or TCD malfunction. Contact INFICON.
11.2.1.3.2 Inverted Peaks
Inverted peaks are usually caused by poor quality carrier gas. The carrier gas must be
99.995% to 99.9995% pure. Inverted peaks often indicate that the carrier gas is
contaminated, or that the incorrect carrier gas is being used or configured.
Carrier gas configuration can be checked on Micro GC Fusion through the System
Status window. Refer to Carrier Gas Requirement [
57] to change the carrier gas.
11.2.1.3.3 Extra Peaks
Extra, or ghost peaks are peaks that appear during a blank or sample run. Ghost
peaks appear even when no sample is injected (and are also found among the actual
component peaks during a sample run).
Ghost peaks appear during a blank run when:
• The column has been heated and idle for an extended period of time
• Carrier gas and plumbing contain impurities such as oils, greases, or other
materials
• There is a reaction of the stationary phase with trace levels of oxygen, water, and
other materials in the carrier gas
• The inlet is contaminated. Residues in the inlet are volatilized or pyrolyzed and
swept onto the head of the column
• The sample conditioner is contaminated. If the sample conditioner contains a filter,
replace the filter
• There is sample carryover from a previous run
Additional peaks appear when:
• Sample is not pure. Run a blank sample (carrier gas only). If the peaks persist,
they are not sample related
• Thermal degradation of one or more components occurs due to an overheated
inlet. Reduce the Sample Inlet Heater Temperature