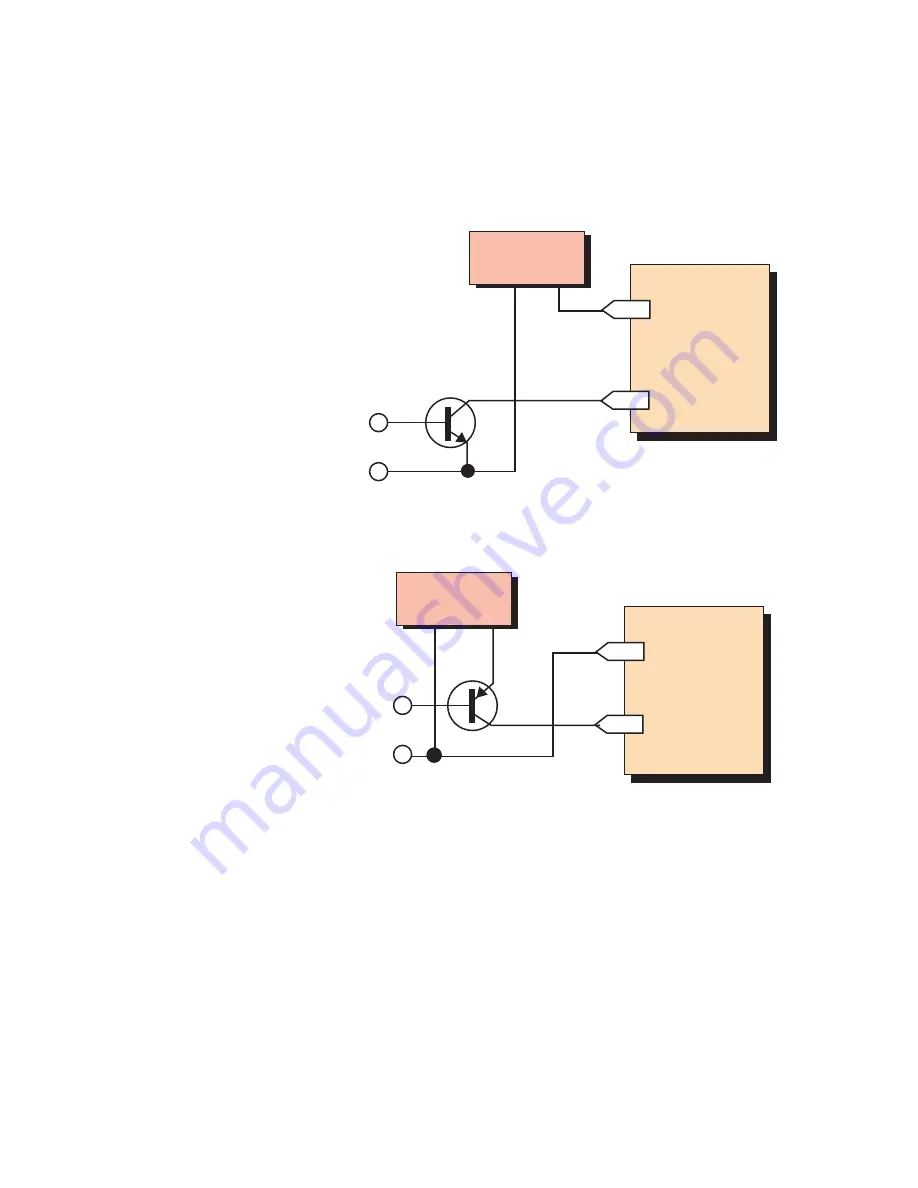
2-18
MDrive 34Plus Microstepping Hardware - Revision R071108
Relevant to Firmware Version 3.0.02
+
+5 to +24VDC
Optocoupler Reference
Input
Controller Output
Controller Ground
+
+5 to +24VDC
Optocoupler Reference
Input
Controller Output
Controller Ground
NPN Open Collector Interface
(Sinking)
PNP Open Collector Interface
(Sourcing)
MDrivePlus
Microstepping
MDrivePlus
Microstepping
Input Connection Examples
The following diagrams illustrate possible connection/application of the MDrivePlus Microstepping Logic
Inputs.
Open Collector Interface Example
Figure 2.3.6: Open Collector Interface Example