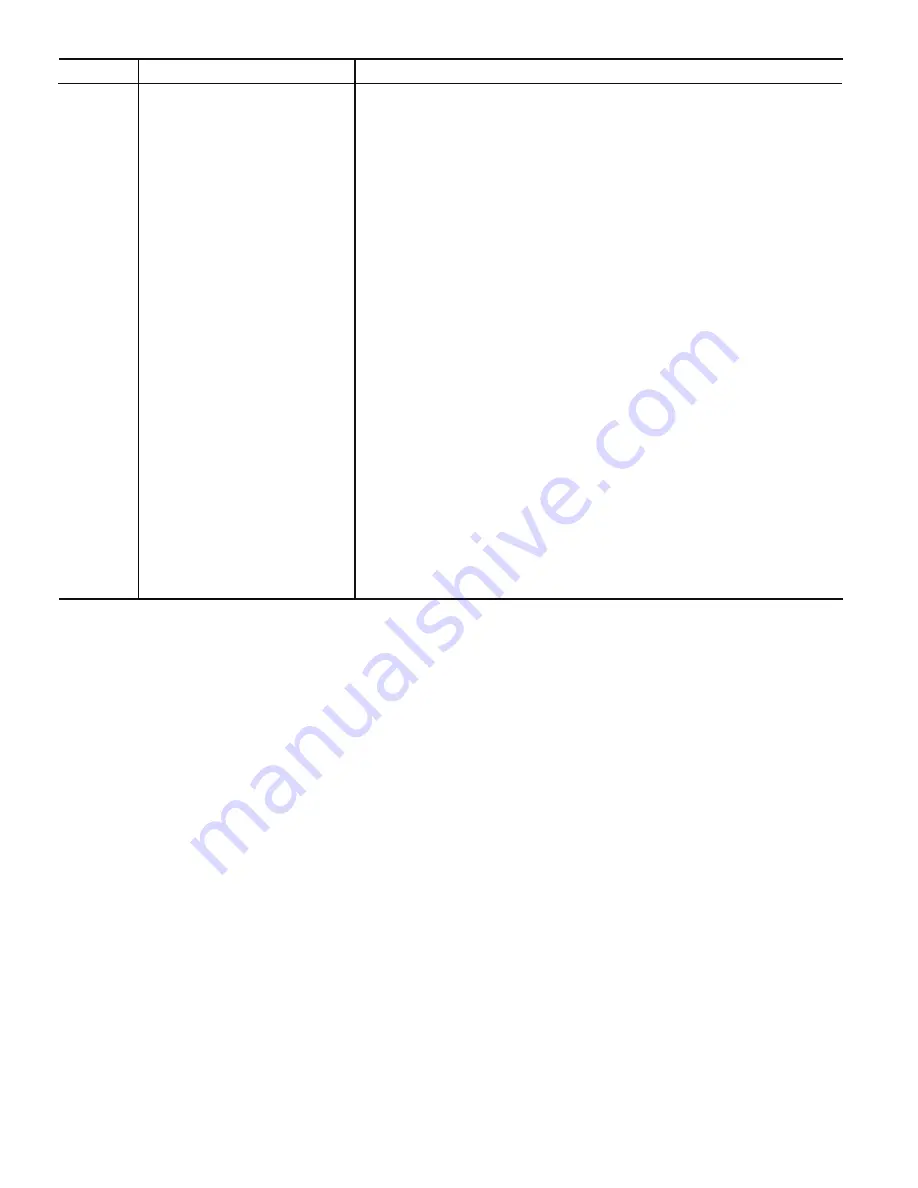
Inspection
Nomenclature
Ref. No.
INSPECTION OF INDIVIDUAL PARTS AND COMPONENTS (Cont)
33
35
36
37
38
40
41
42
44
All
All
Sleeve bearings
Worm
Key
Countershaft drive end
Pin
Spacer
Shaft
Ratchet handle
Lower half housing
Screws and nuts
Pins
Check for wear by trying the bearing on its respective shaft
journal. If more than 0. 002 inch clearance exists, replace
the bearing.
Check for cracks and worn thread. Replace for either con-
dition.
Check for wear caused by keyway "biting" into the sides of the
key. Replace if worn or broken.
Replace if cracked or if square shank is worn.
Check for compression marks and indentations. Replace if
damaged.
Replace if broken, worn or scored.
Check for bends, cracks and scored bearing journal. Replace
for any of these conditions.
Check for proper operation of ratchet mechanism.
Check for cracks and distortion. Distortion can be detected
by placing the parting surface on a surface plate. Contact
should be made throughout the surface with the plate.
Check for damaged threads and other visible damage. Replace
all damaged parts.
Replace if damaged.
25. REPAIR OR REPLACEMENT.
27. REASSEMBLY. (See figure 12.)
NOTE
26. Repairs consist essentially of replacing worn or
damaged parts. Refer to instructions in the inspection table
for checks which determine when parts should be replaced.
a. Press the ball bearing (43) into the recess of the lower
half housing (44).
b. Slide the spacer (40) on the small diameter end of the
shaft (41). Insert key (36) into the keyway. Press the ball
bearing (39) into place against the spacer. Slide the
countershaft end (37) on the shaft (41), rotate the end until
holes are aligned, and press the pin (38) into place. Swell
each end of the pin (38) slightly with a center punch to
prevent it from becoming loose during service.
c. Press the worm (35) on the shaft (41) until the end of the
worm contacts the spacer (40). Place the spacer (34) and
sleeve bearing (33) on the bearing journal of the shaft (41).
Sleeve bearings should be soaked in hot oil
before inserting shaft journals.
d. Place the shaft (41), with parts attached, into the lower
half housing (44). If the ball bearing (39) and sleeve
bearing (33) fail to fit into their respective recesses, recheck
for proper installation of parts on the shaft (41).
e. Place the drive gear (32) into position on top of the ball
bearing (43). Insert the lower end of one of the drive shafts
(31) through the drive gear (32) and into the inner race of
the ball bearing (43). The drive shaft (31) can be lifted out
after reassembly, but when placed in position during
reassembly it will hold the drive gear (32) in proper position,
thus facilitating installation of the upper half housing (28).
f. Pack grease into all gear teeth as outlined in paragraph 19.
g. Press the ball bearing (23) into the recess of the upper
half housing (28) and carefully place the upper half housing
(28) on the lower half housing (44). If all parts have been
properly assembled, the housing will fit together without
excessive resistance. It may be necessary to tap the top
housing lightly with a soft faced mallet in order to assist in
settling all bearings into their recesses.
h. Install screws (29) and lock washers (30), and tighten
securely.
i. Install the slide block support (24) on the upper half
housing (28) with screws (25). Tighten screws securely.
j. Install the pressure plate (15) on the form shoe slide block
(19) with screws (16); if the plate was removed during
disassembly. Slide the form shoe slide block (19) on the slide
block support (24).
k. Thread the feed screw (18) into the screw post (20),
engage the end of the feed screw (18) into the form shoe
slide block (19), and drive the two pins (17) into their holes.
Attach the screw post (20) to the upper half housing (28)
with the cap screw (21) and lock washer (22).
9