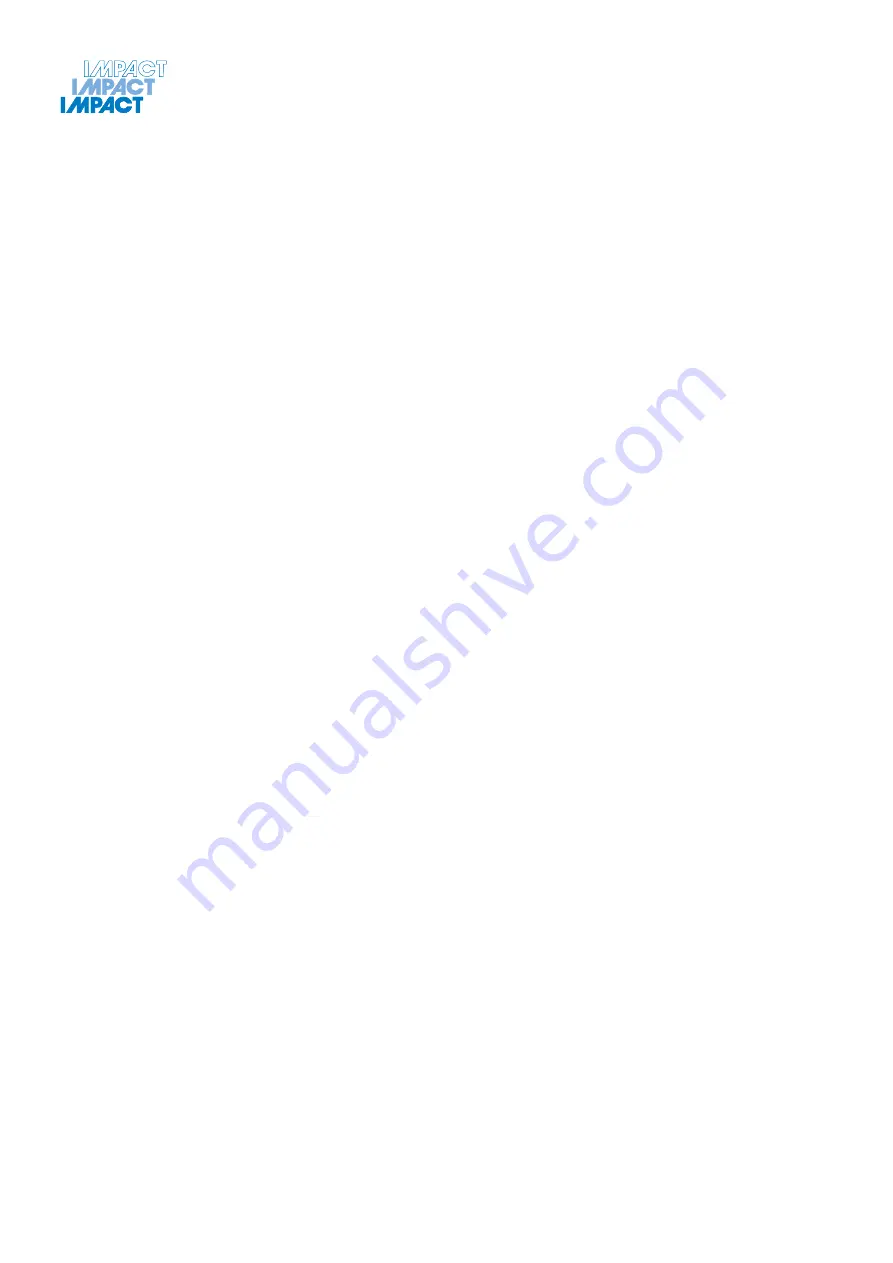
6.7
On completion of the timed run, raise the pivoted arm clear of the Road
Wheel. Disconnect the machine from the supply voltage. Release the
safety cover and remove the Road Wheel from the machine. Thoroughly
clean out the spent abrasives.
6.8
It is essential to clean the feeder thoroughly at the end of each run.
7.
FLOUR EMERY FEED.
7.1
Lift the Tyred Wheel Cover and change the Corn Emery Tyre for the Flour
Emery Tyre by unscrewing and withdrawing the Locating Screw. Remove the
black Blanking Plate from the cover.
7.2
Locate the Flour Emery Powder Spreader on to the Tyred Wheel Cover (2
Hexagonal Socket Cap Head Screws). Check that the spreader is set level
and at the correct height to allow the tip of the felt pad to just clear the
running face of the tyre.
7.3
Locate the Flour Emery Feeder into its Mounting Block on top of the
mainframe and align with the Flour Spreader aperture. Insert the plug
originally located in the Corn Emery Feeder into the Flour Emery Feeder.
Switch on and check the free rotation of the feeder (i.e. the Drive Pulley is
rotating at its nominal speed of 1½ RPM). The Feeder Unit is factory set to
operate within the limits of 2 to 4 gms/min. (Nominally 3 gms/min). The rate of
feed may be finely adjusted by setting the slide plate on the front of the
hopper. Varying the hopper height using the 4 M5 screws carries out coarse
adjustment.
7.4
Fill the Hopper with Flour Emery Powder. Switch on and check the feed over
a short period of time, check that the powder flows freely into the powder
spreader at all times.
7.5
Adjust the water feed to within the limits required. Ideally the water/powder
mix should produce slurry which will just adhere to the running surface of the
tyre. A dry mix will produce a hard crust and a wet mix will tend to wash the
wheel clean.
7.6
Reset the Timer to zero before starting the timed test.
7.7
Adjust the Road Wheel rotation speed to 320-rpm ±5 with the Speed Control
on the Control Unit.
7.8
On completion of the timed run, raise the pivoted arm clear of the Road
Wheel. Disconnect the machine from the supply voltage. Release the
- 10 -
Summary of Contents for AG 139
Page 16: ... 14 ...