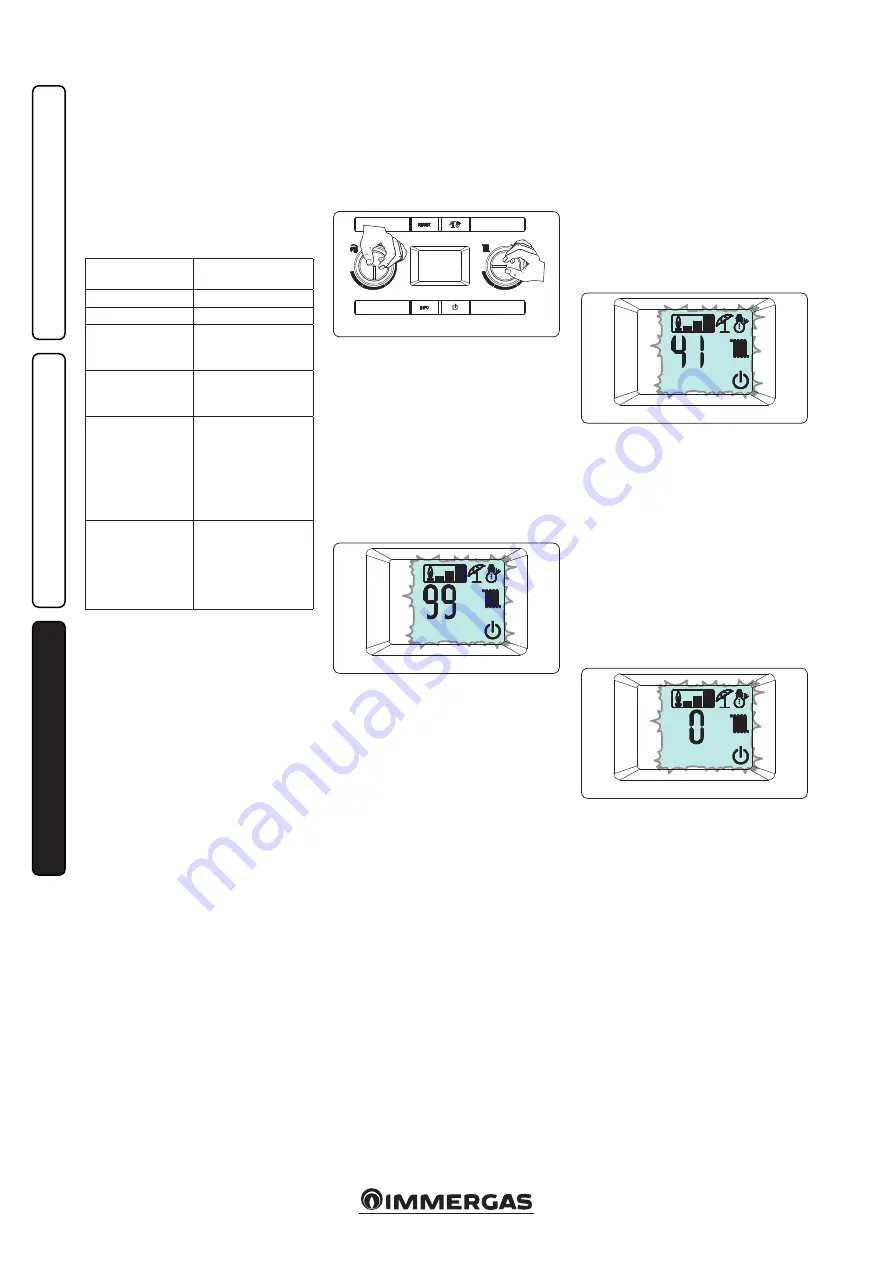
30
INS
TALLER
US
ER
MAINTEN
AN
CE TECHNI
CI
AN
3.
7
CALIBRATION TYPE INVOLVING
THE REPLACEMENT OF A
COMPONENT.
When performing extraordinary maintenance
on the boiler, involving the replacement of a
component, such as the P.C.B. (if the removable
memory is not put into the replacement board)
or components in the air, gas and flame control
circuits, the boiler will need to be calibrated.
Select the type of calibration to be carried out
according to the table below.
Replaced
component
Type of calibration
required
Gas valve
Q
uick calibration
Fan
Q
uick calibration
Burner
Complete calibra-
tion with air-gas ratio
check
Ignition/detection
electrodes
Complete calibra-
tion with air-gas ratio
check
P.C.B.
(New virgin P.C.B.
without removable
memory recovery)
Restore the param-
eters as described in
the paragraph "P.C.B.
programming"
Complete calibra-
tion with air-gas ratio
check
P.C.B.
(Recovery of the
removable memory
with the boiler
parameters set from
the replaced board)
No calibration re-
quired.
3.8 COMPLETE CALIBRATION
FUNCTION.
N.B.:
before carrying out complete calibration,
ensure that all the requirements indicated in
paragraphs 1.23 and 1.24 have been fulfilled.
IMPORTANT NOTE:
to access this function
it is crucial that there are no active requests for
central heating or DHW production.
In the event of anomaly “62” or “72” (see parag.
2.5) the boiler cancels any requests by itself.
N.B.:
during the various calibration stages, the
air - gas ratio can be checked and possibly cor-
rected as described in par. 3.9.
The energy produced is dissipated via the heat-
ing circuit; alternatively, the energy can be
released from the DHW circuit by opening any
hot water tap.
Caution:
in this case the only active temperature
control is the flow probe that limits the maximum
temperature exiting the boiler at 90°C, therefore
be careful not to get burned.
- The calibration procedure involves various
stages:
- nominal heat output calibration;
- intermediate heat output ignition calibration;
- minimum heat output calibration;
- calibration self-check.
Each calibration procedure, if carried out without
altering the parameters, lasts 5 minutes at the
most, after which it switches automatically to
the next parameter until the calibration process
is complete.
In order to access the complete calibration
stage, you must switch the boiler on, set the
DHW selector in the “6 o' clock” position and
the heating selector in the “9 o' clock” position,
(Fig. 3-5) and press the “Reset” button for about
8 seconds until the “chimney sweep” function
is activated; then press the “summer / winter”
button within 3 seconds.
•
Nominal heat output:
with the function active,
the boiler carries out the procedures required
to calibrate the appliance at the nominal heat
output.
At this stage the display features flashing
icons: “summer”, “winter”, “stand-by” and the
operating temperature alternated with the
current operating heat output (99%); once the
parameters are detected and stabilised, the
frame of the flame presence symbol (ref. 10 fig.
2-1) will start flashing (this procedure may last
a few minutes), meaning that the nominal heat
output parameters have been set.
The air - gas ratio can only be corrected after
the flame presence frame has flashed (see parag.
3.9) or switch to the next heat output parameter
by pressing the “info” button.
3-5
3-6
•
Intermediate heat output ignition:
once the
nominal heat output calibration is confirmed,
the boiler is calibrated with the intermediate
heat output (or ignition heat output).
At this stage the display features flashing
icons: “summer”, “winter”, “stand-by” and the
operating temperature alternated with the cur-
rent operating heat output (typically 41% but
variable according to the boiler model); once
the parameters are detected and stabilised, the
frame of the flame presence symbol will start
flashing, meaning that the intermediate heat
output parameters have been set.
The air - gas ratio can only be corrected after
the flame presence frame has flashed (see parag.
3.9) or switch to the next heat output parameter
by pressing the “info” button.
•
Minimum heat output:
after having calibrated
the boiler with the intermediate heat output, it
is calibrated with the minimum heat output.
At this stage the display features flashing
icons: “summer”, “winter”, “stand-by” and the
operating temperature alternated with the
current operating heat output (0%); once the
parameters are detected and stabilised, the
frame of the flame presence symbol will start
flashing, meaning that the minimum heat
output parameters have been set.
The air - gas ratio can only be corrected after
the flame presence frame has flashed (see parag.
3.9) or exit the calibration mode by pressing the
“summer / winter” button.
•
Calibration self-check:
once calibration opera-
tions are complete, the boiler runs a self-check
for about one minute. During this check, the
boiler can run at different powers and it is not
possible to apply modifications to the operat-
ing parameters or to delete the operation in
progress. Moreover, it is important not to cut
the boiler’s power.
3-7
3-8
Summary of Contents for Victrix Maior 28 TT 1 ErP
Page 1: ...VICTRIX MAIOR 28 35 TT 1 ERP IE Instruction and recommendation booklet 1 038659ENG...
Page 2: ......
Page 49: ...49...
Page 50: ...50...
Page 51: ...51...