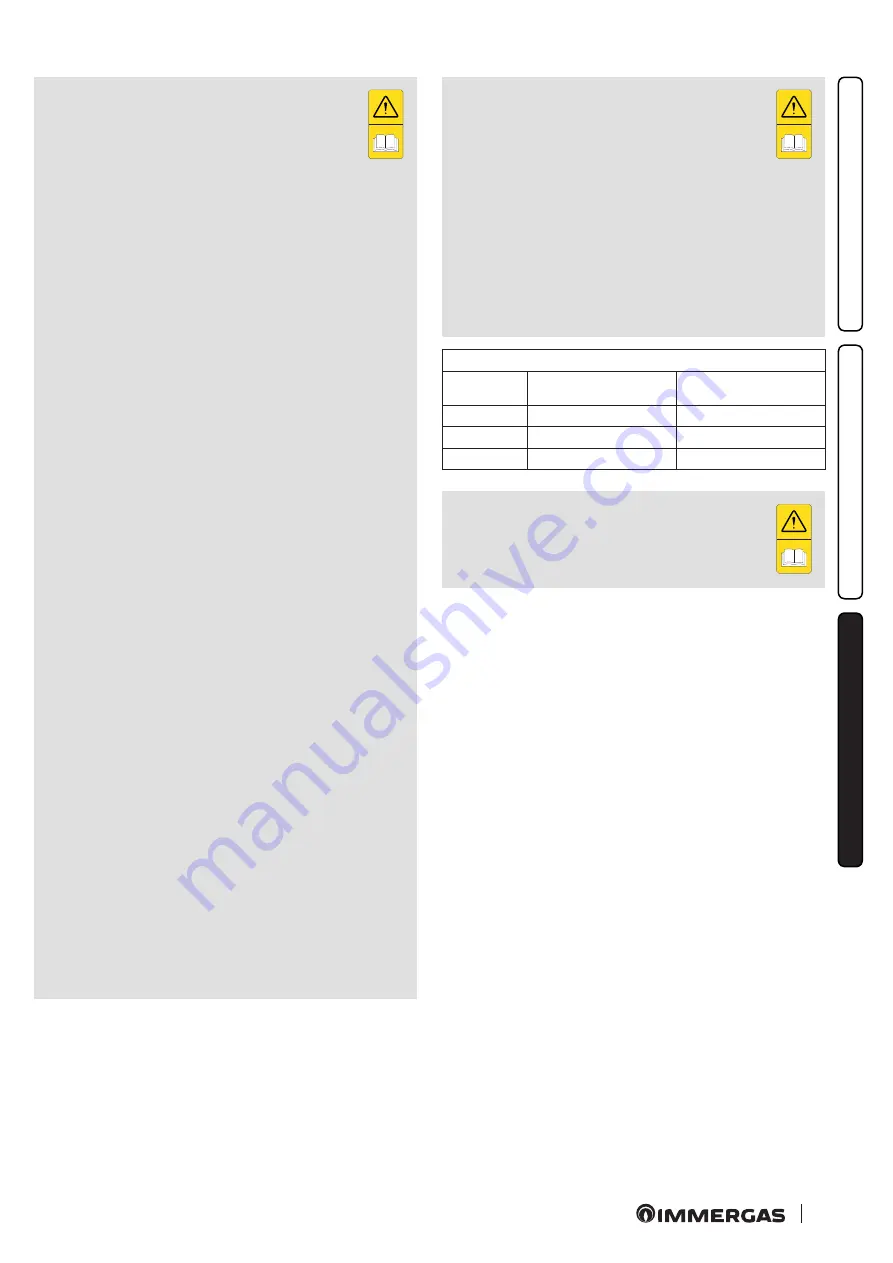
45
INS
TALLER
US
ER
MAINTEN
AN
CE TECHNI
CI
AN
3.3 YEARLY APPLIANCE CHECK AND
MAINTENANCE.
The following checks and maintenance should be
performed at least once a year to ensure operation,
safety and efficiency of the appliance over time.
- Clean the flue side of the heat exchanger.
- Clean the main burner.
- Check the correct positioning, integrity and cleanliness of the
detection and ignition electrode; remove any oxide present.
- If deposits are detected in the combustion chamber they must
be removed and the heat exchanger coils must be cleaned
using nylon or broomcorn brushes; it is forbidden to use
brushes made of metal or other materials that may damage
the combustion chamber. It is also forbidden to use alkaline
or acid detergents.
- Check the integrity of the insulating panels inside the com-
bustion chamber and if damaged replace them.
- Visually check for water leaks or oxidation from/on fittings
and traces of condensate residues inside the sealed chamber.
- Check the contents of the condensate drain trap.
- Check that there are no material residues in the condensate
drain siphon clogging the condensate passage; also check that
the entire condensate drainage circuit is clear and efficient.
In the event of obstructions (dirt, sediment, etc.) with con-
sequent leakage of condensate in the combustion chamber,
one must replace the insulating panels.
- Check that the burner and gas manifold seal gaskets are intact
and perfectly efficient, otherwise replace them. In any case the
gaskets must be replaced at least every two years, regardless
of their state of wear.
- Check that the burner is intact, that it has no deformations or
cuts and that it is properly fixed to the combustion chamber
lid; otherwise it must be replaced.
- Visually check that the drain of the water safety valve is not
clogged.
- Check that, after discharging system pressure and bringing it
to zero (read on boiler pressure gauge), the expansion vessel
pressure is at 1.0 bar.
- Check that the system static pressure (with system cold and
after refilling the system by means of the filling valve) is be-
tween 1 and 1.2 bar.
- Visually check that the safety and control devices have not
been tampered with and/or shorted, in particular:
- Check the condition and integrity of the electrical system and
in particular:
- the power cables must be inside the cable fixings;
- there must be no traces of blackening or burning.
- Check correct lighting and functioning.
- Check the CO
2
by using the chimney sweep function
at the reference heat outputs, using the parameters
in the table below. Should values out of the indicated
tolerance range be detected, check the calibration
again (Ref. Par. CO
2
adjustment).
- Check correct operation of control and adjustment
devices of the appliance. and in particular:
- system regulation probes intervention;
- domestic hot water control thermostat interven-
tion.
- Check tightness of gas circuit and the internal system.
- Check the intervention of the device against no gas ionisation
flame control. Intervention time must be less than 10 seconds.
Victrix Tera Vip
CO
2
at nominal
output
CO
2
at minimum
output
G 20
9,70 % - 0,2 / + 0,5
8,80 % - 0,3 / + 0,2
G 31
11,40 % - 0,3 / + 0,1
10,60 % - 0,1 / + 0,3
G 230
11,00 % - 0,3 / + 0,1
10,00 % - 0,1 / + 0,3
In addition to yearly maintenance, one must also
check the energy efficiency of the thermal system,
with frequency and procedures that comply with the
indications of the technical regulations in force.