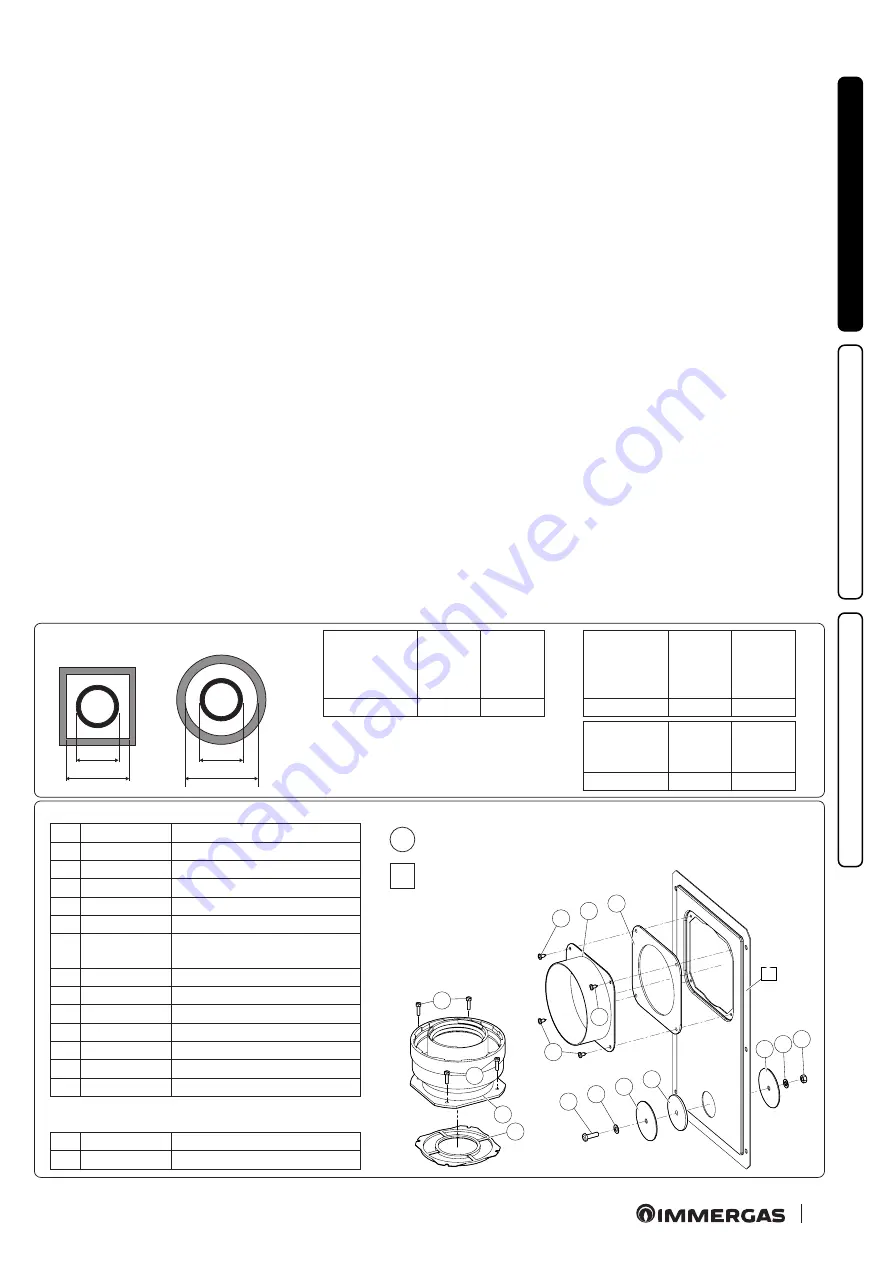
1
2
3
3
3
4
5
6
7
6 8
9
A
10
11
12
12
24
A
B
A
C
25
27
INS
TALLER
US
ER
MAINTEN
AN
CE TECHNI
CI
AN
1.17 ADAPTOR C9 KIT INSTALLATION.
This kit allows an Immergas boiler to be installed in “C
93
” config-
uration, with combustion air intake directly from the shaft where
the flue gas exhaust is, obtained by means of a ducting system.
System composition.
The system must be combined with the following components
(sold separately) to be functional and complete:
- kit C
93
Ø 100 or Ø125 version;
- rigid ducting Ø 60 and Ø 80 and flexible Ø 50 and Ø 80 kit;
- flue exhaust kit Ø 60/100 or Ø 80/125 configured according to
the installation and type of boiler.
Kit Assembly.
- Mount the components of kit “C9” on the door (A) of the ducting
system (Fig. 25).
- (Version Ø 125 only) mount the flanged adaptor (11) interposing
the concentric gasket (10) on the boiler, fitting it with the screws
(12).
- Mount the ducting system as described in the relative instruc-
tions fiche.
- Calculate the distances between the boiler drain and the bend
of the ducting system.
- Prepare the boiler flue system, making sure that the internal pipe
of the concentric kit is fitted up to the end stop in the ducting
system curve (Quota “X” Fig. 26), whereas the external pipe must
reach the end stop of the adapter (1).
N.B.:
to encourage the removal of possible condensate forming
in the exhaust pipe, tilt the pipes towards the boiler with a min-
imum slope of 1.5%.
- Mount the cover (A) complete with adaptor (1) and caps (6) on
the wall and assemble the flue system to the ducting system.
N.B.:
(version Ø 125 only) before assembly check the gaskets are
in the right position. In the event component lubrication (already
carried out by the manufacturer) is not sufficient, remove the
residual lubricant using a dry cloth, then to ease fitting coat the
parts with common or industrial talc.
Once all components have been assembled properly, the exhaust
fumes will be expelled via the ducting system; the combustion
air for normal boiler operation will be aspirated directly by the
shaft (Fig. 26).
Kit composition:
Ref.
Qty
Description
1
1
Door adaptor Ø 100 or Ø 125
2
1
Door gasket made of neoprene
3
4
Screws 4.2 x 9 AF
4
1
Hex headed screw M6 x 20
5
1
Flat nylon washer M6
6
2
Door hole closure metal-sheet
plate plug
7
1
Plug gasket made of neoprene
8
1
Toothed washer M6
9
1
Nut M6
10 1 (kit 80/125) Concentric gasket Ø 60-100
11 1 (kit 80/125) Flanged adapter Ø 80-125)
12
4 (kit80/125) Hex headed screws M4 x 16 slotted
-
1 (kit 80/125) Bag of lubricating talc
Installation drawings key:
Unique identification of the component in
the kit
Identification of the component not supplied
in this kit
1
A
Supplied separately:
Ref.
Qty
Description
A
1
Ducting kit door
Rigid Ø 80
ducting
(A) mm
SHAFT
(B) mm
SHAFT
(C) mm
86
126
146
Flexible Ø 80
ducting
(A) mm
SHAFT
(B) mm
SHAFT
(C) mm
90
130
150
Ducting
Ø 60 Rigid and
Ø 50 Flexible
(A) mm
SHAFT
(B) mm
SHAFT
(C) mm
66
106
126