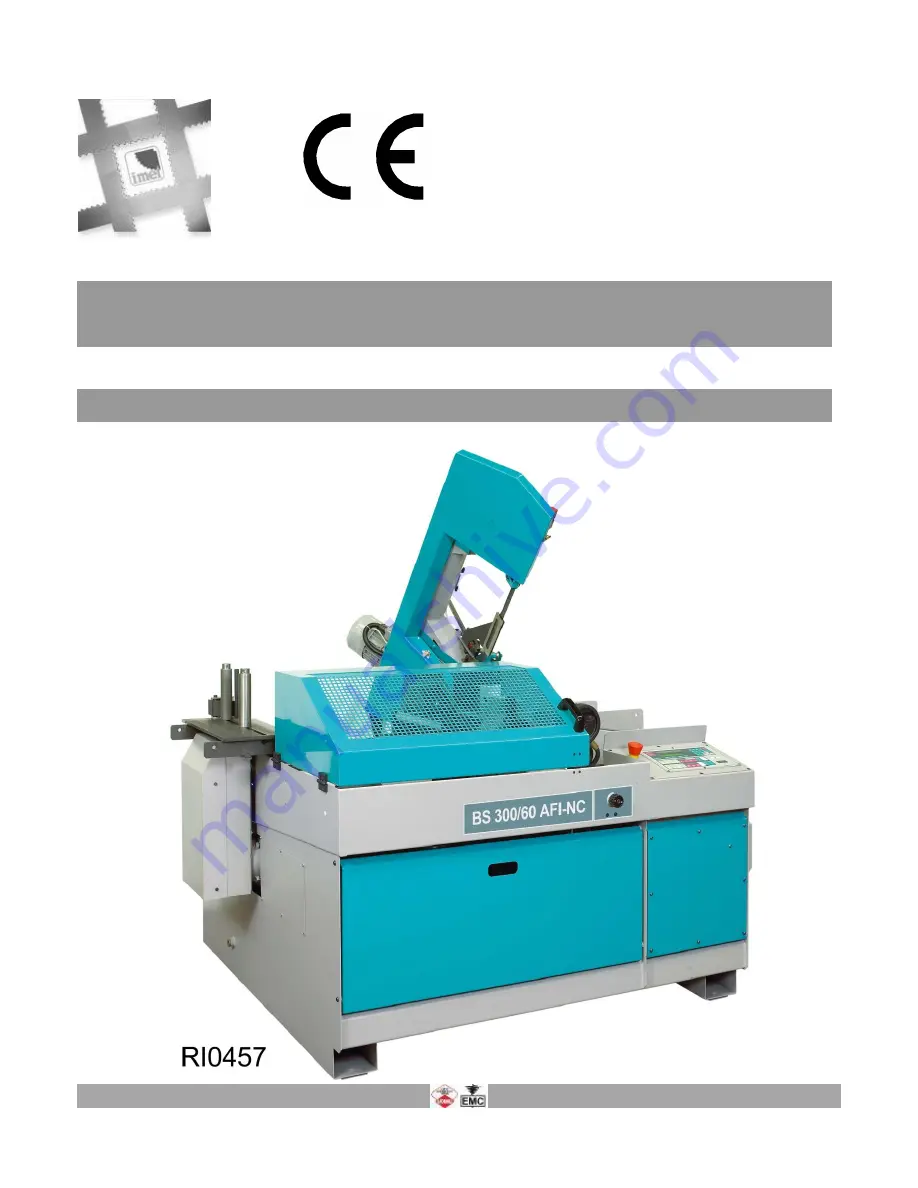
TRADUCTION OF THE ORIGINAL INSTRUCTIONS FOR USE
BS 300/60 AFI-NC ED.2010 rev.00
1/59
IMET Spa
Loc. Tre Fontane - Cisano Bergamasco
Tel. 035/4387911 - Fax. 035/787066
Web site: www.imetsaws.com
E-mail: [email protected]
Automatic, hydraulic bandsaw BS300/60 AFI-NC
with Numeric Control
USER’S INSTRUCTIONS
Summary of Contents for BS300/60 AFI-NC
Page 37: ...ISTRUZIONI PER L USO BS 300 60 AFI NC ED 2010 rev 00 37 59...
Page 38: ...ISTRUZIONI PER L USO BS 300 60 AFI NC ED 2010 rev 00 38 59...
Page 39: ...ISTRUZIONI PER L USO BS 300 60 AFI NC ED 2010 rev 00 39 59...
Page 40: ...ISTRUZIONI PER L USO BS 300 60 AFI NC ED 2010 rev 00 40 59...
Page 41: ...ISTRUZIONI PER L USO BS 300 60 AFI NC ED 2010 rev 00 41 59...
Page 42: ...ISTRUZIONI PER L USO BS 300 60 AFI NC ED 2010 rev 00 42 59...
Page 43: ...ISTRUZIONI PER L USO BS 300 60 AFI NC ED 2010 rev 00 43 59...
Page 44: ...ISTRUZIONI PER L USO BS 300 60 AFI NC ED 2010 rev 00 44 59...
Page 45: ...ISTRUZIONI PER L USO BS 300 60 AFI NC ED 2010 rev 00 45 59...
Page 46: ...ISTRUZIONI PER L USO BS 300 60 AFI NC ED 2010 rev 00 46 59...
Page 47: ...ISTRUZIONI PER L USO BS 300 60 AFI NC ED 2010 rev 00 47 59...
Page 48: ...ISTRUZIONI PER L USO BS 300 60 AFI NC ED 2010 rev 00 48 59...
Page 49: ...ISTRUZIONI PER L USO BS 300 60 AFI NC ED 2010 rev 00 49 59...
Page 59: ...ISTRUZIONI PER L USO BS 300 60 AFI NC ED 2010 rev 00 59 59...