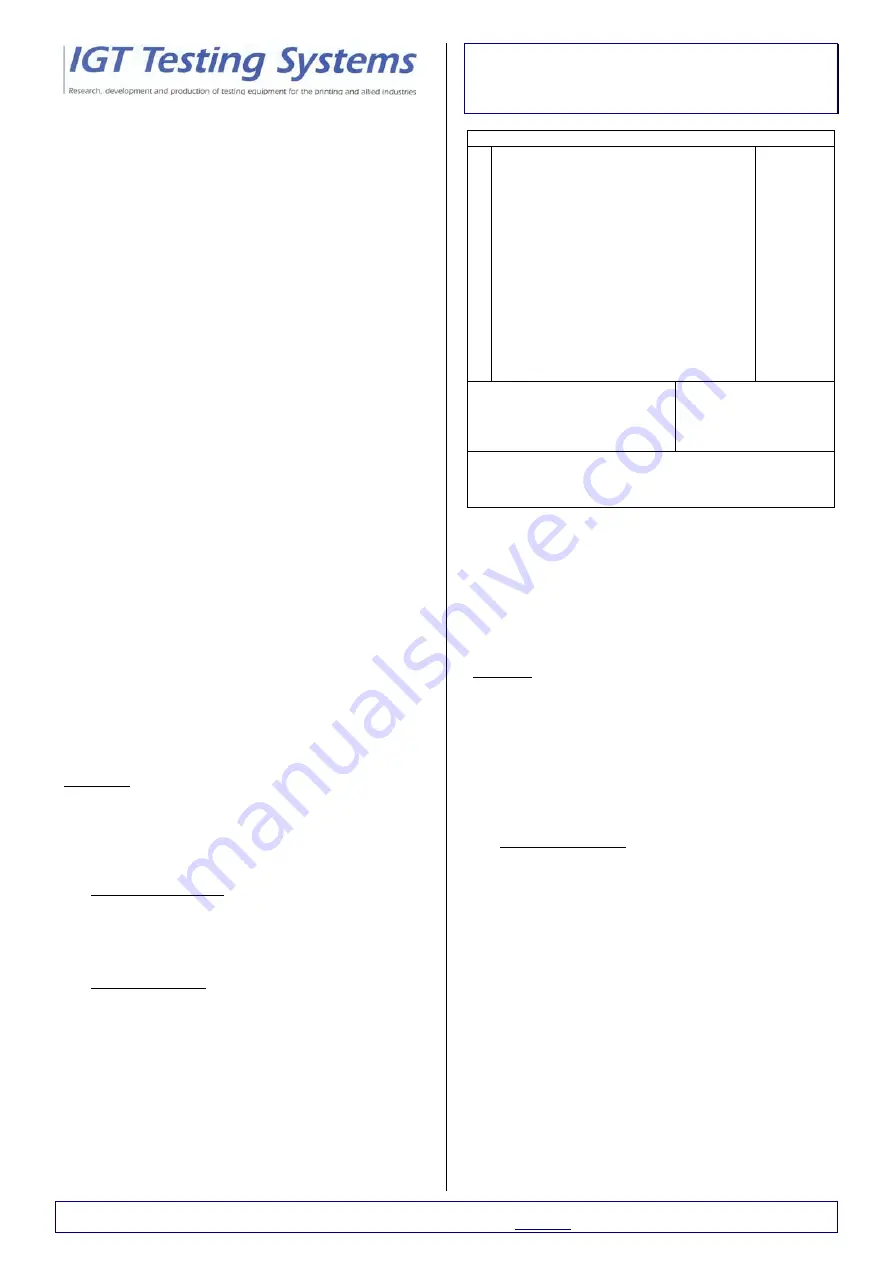
IGT Testing Systems, P.O.Box 12688, 1100 AR Amsterdam, The Netherlands / Keienbergweg 25, 1101 EX Amsterdam, The Netherlands
Phone +31 (0)20 409 9300, Fax +31 (0)20 697 4842, E-mail: [email protected] Internet: www.igt.nl
Introduction:
Mottling is the uneven appearance, mostly in solid areas: small
dark and light areas appearing in the surface of paper (board)
caused by ink, paper or press work.
As this definition says mottle is influenced by many parameters:
type of ink, colour sequence, construction of printing press,
speed, rubber blanket, damping water and the most important
one: the type of paper. Variations in the surface characteristics as
absorption and smoothness play an important role in the mottle
and are caused by the production process and the components in
the paper.
There can be three kinds of mottle:
•
Back trap (print) mottle: an uneven printing result, caused by
uneven ink absorption of the paper. A testing method is described
in this information leaflet. An alternative and easier, but
sometimes less accurate method has been described in IGT
information leaflet W58.
•
Water interference mottle: an uneven printing result, caused by
insufficient and uneven water absorption of the paper, followed
by uneven ink absorption. This testing method has been
described in IGT information leaflet W59.
•
Ink trap mottle: an uneven printing result, caused by a wrong
trapping of the ink in tack and/or viscosity and is also influenced
by an uneven absorption of the ink by the paper. This method has
been described in IGT information leaflet W69 (rubber 65 Shore
A) and W 46 (rubber 85 Shore A).
Principle:
A paper is printed several times under standard conditions with
an IGT printability tester. The result is observed as a degree of
unevenness in the print quality. This can be done visually in
comparison with a self made scale or other papers and with an
analysing system.
Method of operation:
•
It is recommended to execute the test in the standard atmosphere; to
most standards it is 23.0 ± 1.0 °C (73.4 ± 1.8 °F) and 50 ± 2% rh.
•
For the operation of the AIC2-5T2000, Global Standard Tester, High
Speed Inking Unit 4 and ink pipette follow the instructions of the
manuals, IGT information leaflet W100 and the displays accurately.
•
Handle the samples carefully.
Preparation:
1.
Condition the papers, the ink and the equipment during >6
hours in the standard atmosphere.
2.
Cut the paper strips (preferable 55 x 340 mm, 3 strips per
sample) and mark them with top and/or bottom side,
machine and/or cross direction and a code for the type of
paper.
3.
For AIC2-5T2000 only:
3.1.
Adjust the printing force of the upper printing disc
shaft to 625 N and pay attention for the right backlash.
See W100.
3.2.
Adjust the printing speed to 0.2 m/s in the constant
speed mode (
).
4.
For GST2/3/3H only: Select the menu “Print mottle” in the
display.
5.
Take off the brush from the tester.
6.
Check the functioning of the tester following the
instructions in the chapter “Execution”.
7.
Fill the ink pipette with the mottle test ink.
8.
Adjust the High Speed Inking Unit with the following
settings:
IGT Information leaflet W58
PRINT MOTTLE
IGT AIC2-5T2000, Global Standard Tester 2/3/3H
Version: July 2006
Materials / testing conditions
1
2
3
4
5
6
7
8
9
10
11
12
IGT AIC2-5T2000
or IGT Global Standard Tester 2
or IGT Global Standard Tester 3
or IGT Global Standard Tester 3H
IGT High Speed Inking Unit 4
(Top roller with 4 segments for conventional inks)
IGT ink pipette
Printing disc, covered with rubber blanket, 50 mm
wide, ø 68 mm
Huber mottle test ink
DOMAS Analyzing System (if desired)
Strips of paper to be tested, preferable 55 x 340 mm,
3 strips per sample
Reference mottle scale (if desired)
Lint free rags
Cleaning naphtha
710.000.000
412.000.000
416.000.000
467.000.000
466.000.710
(466.003.003)
408.000.200
402.362
404.800.010
520.100
Printing force
Printing speed
Time between printing and set off’s
Number of set off’s
Ink film thickness (volume)
625 N
Constant, 0.2 m/s
10 s
4x
2.4 µm (0.10 cm
3
)
►
The numbers 1 thru 7 are available at IGT Testing Systems.
►
The numbers 5 and 6 can be obtained as Mottle Test Set (print
method) for AIC2-5T2000, GST 2/3/3H, article number 487.000.710.058.
►
This leaflet contains article numbers per January 1st, 2006
◄
.
Water bath: 23.0º C (73.4º F)
Top roller: 4-segmented, rubber for conventional inks
Mode:
2
Starting time: 5 s
Distribution time: 10 s
Distribution speed: 1.2 m/s
Inking time printing discs: 5 s
9. Check the functioning of the High Speed Inking Unit.
Execution:
1.
Attach a test strip on the sector and fasten the end of the test
strip on the sector with tape.
2.
Apply 0.10 cm³ of ink to the inking unit and distribute the
ink. NOTE: It is not advised to add some ink after a test
3.
Place a printing disc on the printing disc shaft of the inking
unit and ink the printing disc during the preset time.
4.
Take the printing disc from the inking unit and place it on
the (top) printing disc shaft of the tester and turn it into the
position that the seam in the rubber blanket is toward the
sector.
5.
For AIC2-5T2000 only:
5.1.
Turn the sector into starting position.
5.2.
Start the stopwatch.
5.3.
Press one of the side buttons to start the motor.
5.4.
Move the printing disc into printing position against
the test strip.
5.5.
At a certain time, e.g. 10 s after having started the
stopwatch, press the other button to make a print.
5.6.
Directly move the printing disc out of printing
position.
5.7.
Directly move the sector into starting position.
5.8.
Directly turn the disc into the position that the seam
of the blanket is toward the sector.
5.9.
Directly press one of the side buttons to start the
motor.
5.10.
Directly move the printing disc into printing position
against the test strip.
5.11.
After 10 s after having made the print, make a print.
5.12.
Repeat the points 5.6 thru 5.11 for the next three
times.
►