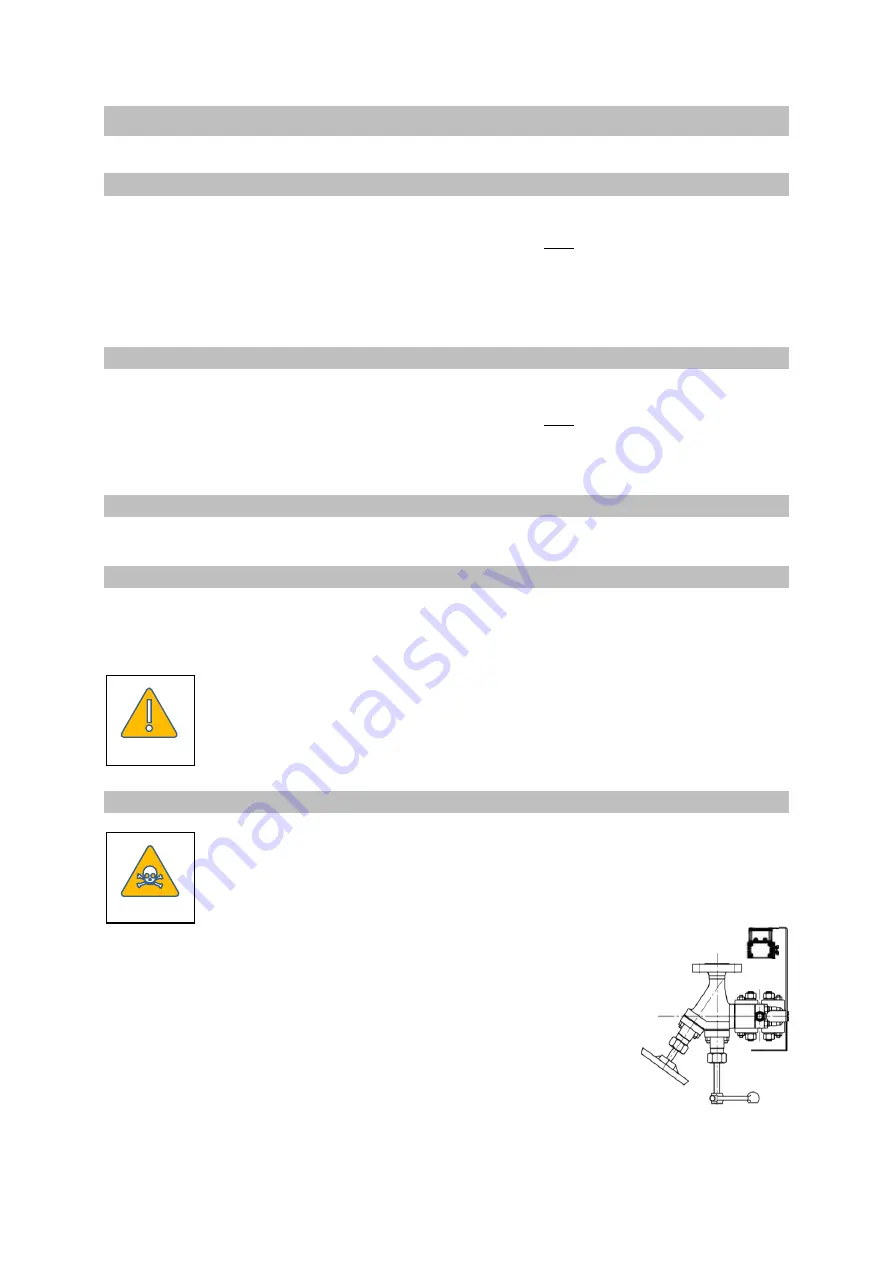
16
7. Assembly
7.1 Version with flange
•
Respect installation position!
•
Remove protection caps from connection flanges. Caps
only
serve as transport
protection.
•
Ensure that sealing surfaces are clean and undamaged.
•
Mount transparent level gauge.
7.2 Version with welding end
•
Respect installation position!
•
Remove protection caps from connection flanges. Caps
only
serve as transport
protection.
•
Assembly only by using welding process 111 and 141.
7.3 Heat treatment of weldseams
Supplementary temper tests of weldseams are not required.
7.4 Drain piping
•
Close valves (D1, D2, W1, W2) after mounting
.
•
Mount drain piping on drain valve (4) (to be provided by the customer).
Ensure that drain piping has free outlet to atmosphere and is protected
from pressure peaks!
7.5 Illumination device
Only use the lamp in explosion-proofed rooms!
Only skilled and qualified electricians may carry out assembly and
connection of the lamps!
Never insulate illumination devices!
Mount the illumination device with the fixing elements on the level gauge.
Caution
Danger