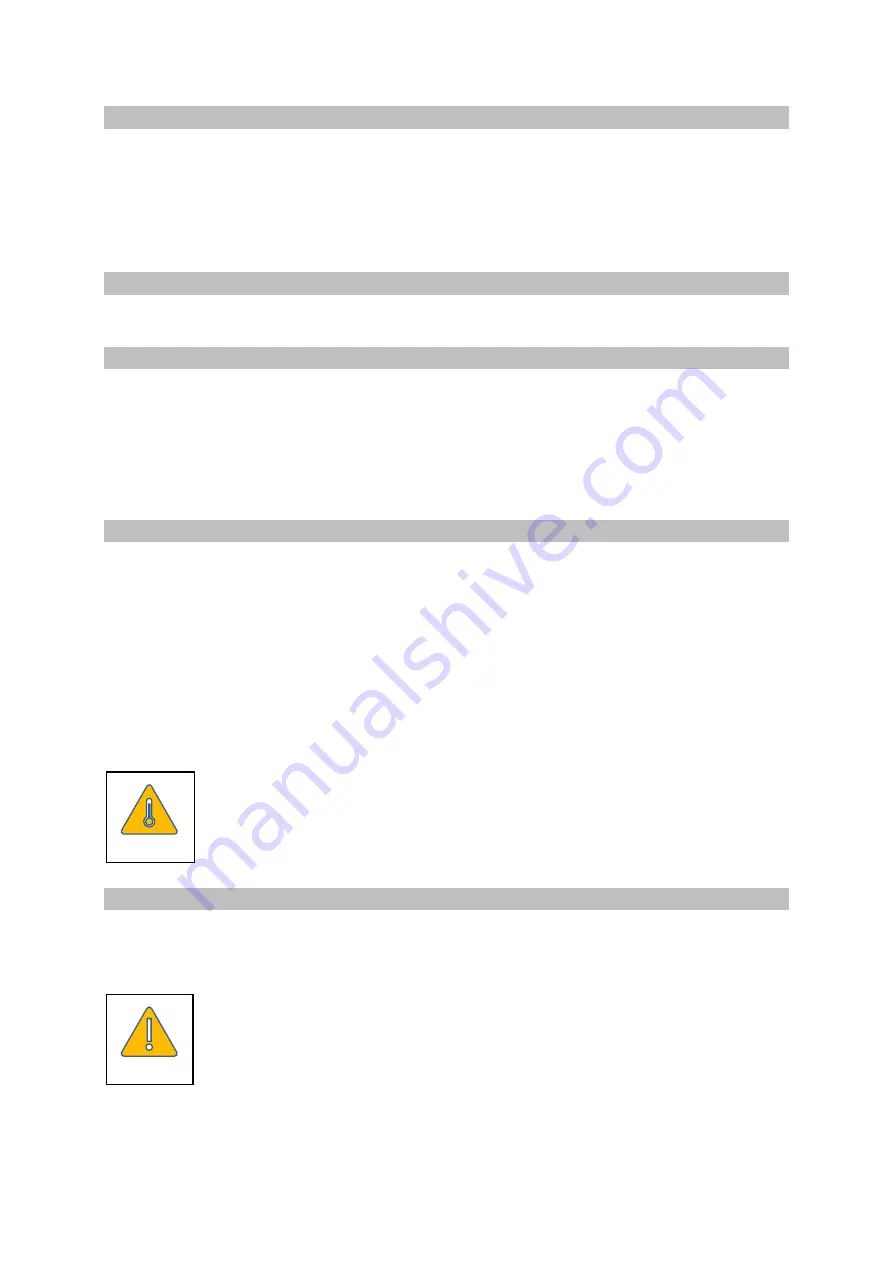
14
7.2 Version with welding end
•
Observe installation position!
•
Remove protection caps from connection flanges. Caps only serve as transport protection.
•
Assembly only by using welding process 111 (manual arc welding) and 141 (tungsten inert
gas welding).
7.3 Heat treatment of weld seams
Supplementary temper tests of weld seams are not required.
7.4 Flap indicator
•
The centre of the lower process connection is the reference point for the zero mark of the
flap indicator (3).
•
The flap indicator fixed by bolt springs (3.1) with stop clamp (3.2) to the standpipe (factory-
made) can be turned into desired position.
Also turn stop clamp!
7.5 Float installation
•
The float (2.1) with inner magnetic system and the new gasket (2.2) are packed and fixed
outside of the standpipe (2) when the unit is supplied.
•
Open cover flange (2.3)
•
Carefully remove float packing
•
Insert float with top-heavy side upwards into standpipe (top-heavy side with colour marking)
•
Tighten cover flange (2.3) and associated gaskets (2.2) with standpipe using successively
opposite diagonal tightening (see chapter 9.2)
The pressure test of the tank must be carried out without the float!
The float may remain in the standpipe if there are valves between the
boiler and the standpipe which are shut off during the test.
7.6 Drain piping
•
Check bolting drain valve (A) / standpipe (2) and retighten if necessary.
•
Mount drain piping on drain valve (A) (to be provided by the customer).
Ensure that drain piping has free outlet to atmosphere and is protected
from pressure peaks!
•
Close valves.
Caution
Caution
Summary of Contents for NA7-130
Page 24: ...24 15 Manufacturer s Declaration...
Page 25: ...25...
Page 26: ...26...
Page 27: ...27...