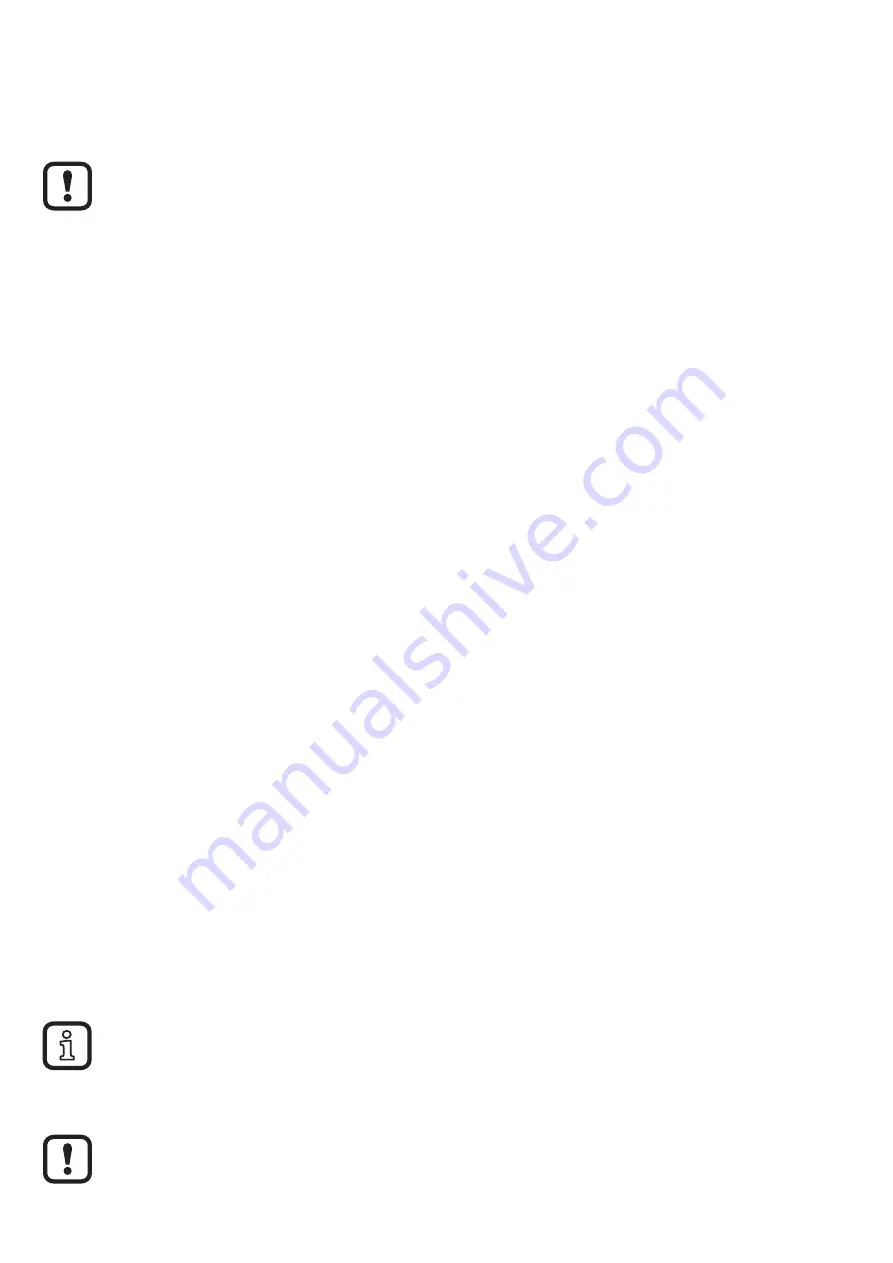
14
8 Parameter setting
A PC with USB IO-Link master
or a programmed memory plug
a configured IO-Link environment
is required to set the parameters�
Changing parameters during operation can influence the function of the
plant�
►
Make sure that there will be no malfunctions or dangerous operation in
your plant�
8.1 Parameter setting using PC and USB IO-Link master
► Prepare PC, software and master. → Observe the operating instructions of the
�
► Connect the unit to the USB IO-Link master (→ Accessories).
►
Follow the menu of the IO-Link software�
► Set the parameters; adjustable parameters (→ 8.4)
►
Check if the parameter setting was accepted by the unit� If necessary, read
sensor again�
►
Remove USB IO-Link master and put the unit into operation
�
8.2 Parameter setting via the memory plug
Via a memory plug (→ Accessories), a parameter set can be written/transferred to
�
► Load suitable parameter set (e.g. using a PC) to the memory plug.
→ Observe the operating instructions of the memory plug.
►
Make sure that the sensor has the original factory settings�
►
Connect the memory plug between sensor and socket�
> When voltage is supplied, the parameter set is transferred from the memory
plug to the sensor�
►
Remove the memory plug and put the unit into operation
�
The memory plug can also be used to save the current parameter setting of
a unit and to transfer it to other units of the same type�
8.3 Parameter setting during operation
Parameter setting during operation is only possible with an
IO-Link-capable module (master).