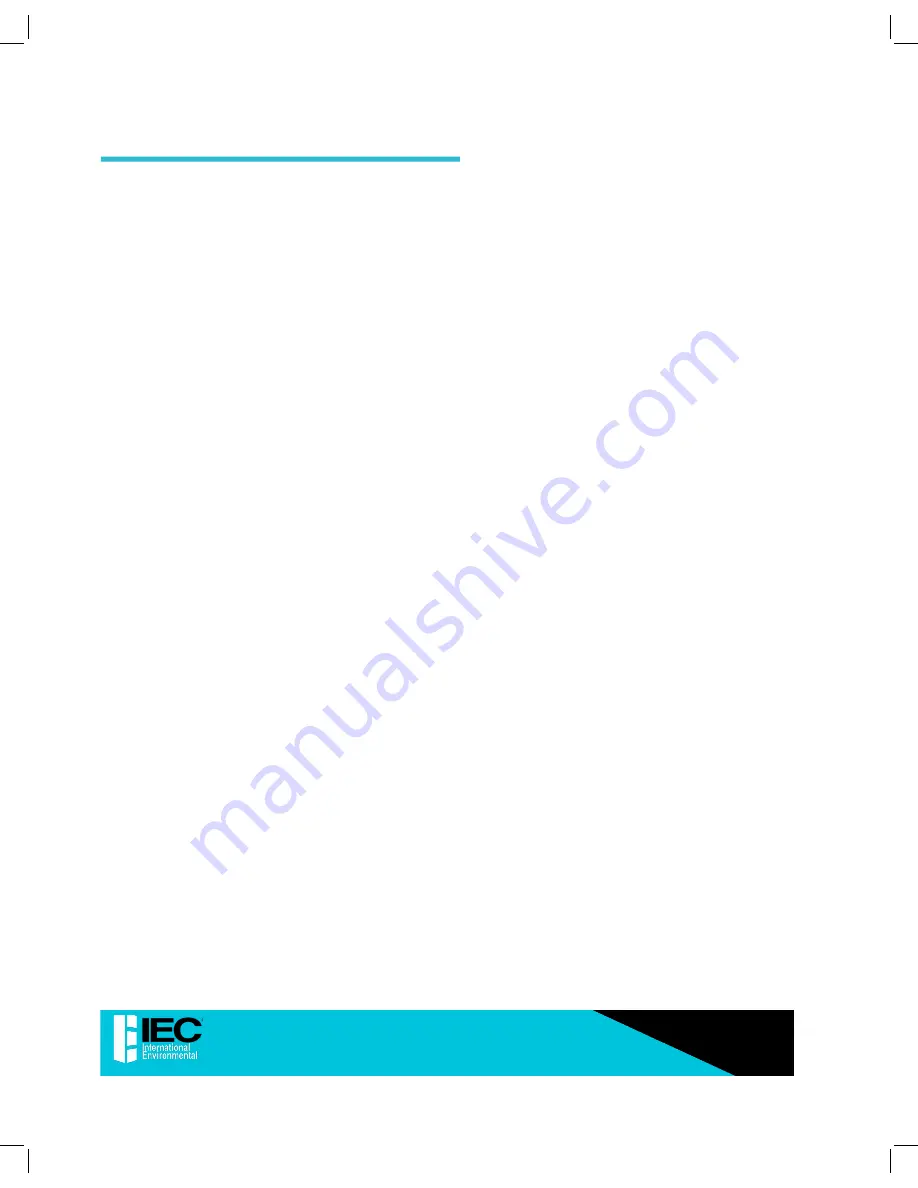
Replacement Parts
Factory replacement parts should be used wherever
possible to maintain unit performance, its normal operating
characteristics, and the testing agency listings. Replacement
parts may be purchased through a local sales representative.
Should replacement parts not be purchased from the factory,
use only parts duplicating the exact type, size, voltage, and
other operating characteristics of the original part.
Contact the local sales representative or the factory before
attempting any unit modifications. Any modifications not
authorized by the factory could result in personal injury,
damage to the unit, and could void all factory warranties.
When ordering parts, the following information must be
supplied to ensure proper part identification:
(1) Complete unit model number
(2) Unit serial number
(3) Unit hand connection (right or left hand)
(4) Complete part description including any numbers
On warranty replacements, in addition to the information
previously listed, the unit shipping code which appears on
the upper right-hand corner of the serial plate is required.
Contact the factory for authorization to return any parts
such as defective parts replaced in warranty. All shipments
returned to the factory must be marked with a Return
Authorization Number which is provided by the factory.
All equipment and components sold through the Parts
Department are warranted under the same conditions as
the standard manufacturer’s warranty with the exception
that the warranty period is twelve (12) months unless the
component is furnished as a warranty replacement. Parts
furnished as warranty replacements are warranted for the
remaining term of the original unit warranty, or not less than
thirty (30) days.
24
24
Modular Hi-Rise Series Fan Coils
INSTALLATION, OPERATION, & MAINTENANCE MANUAL