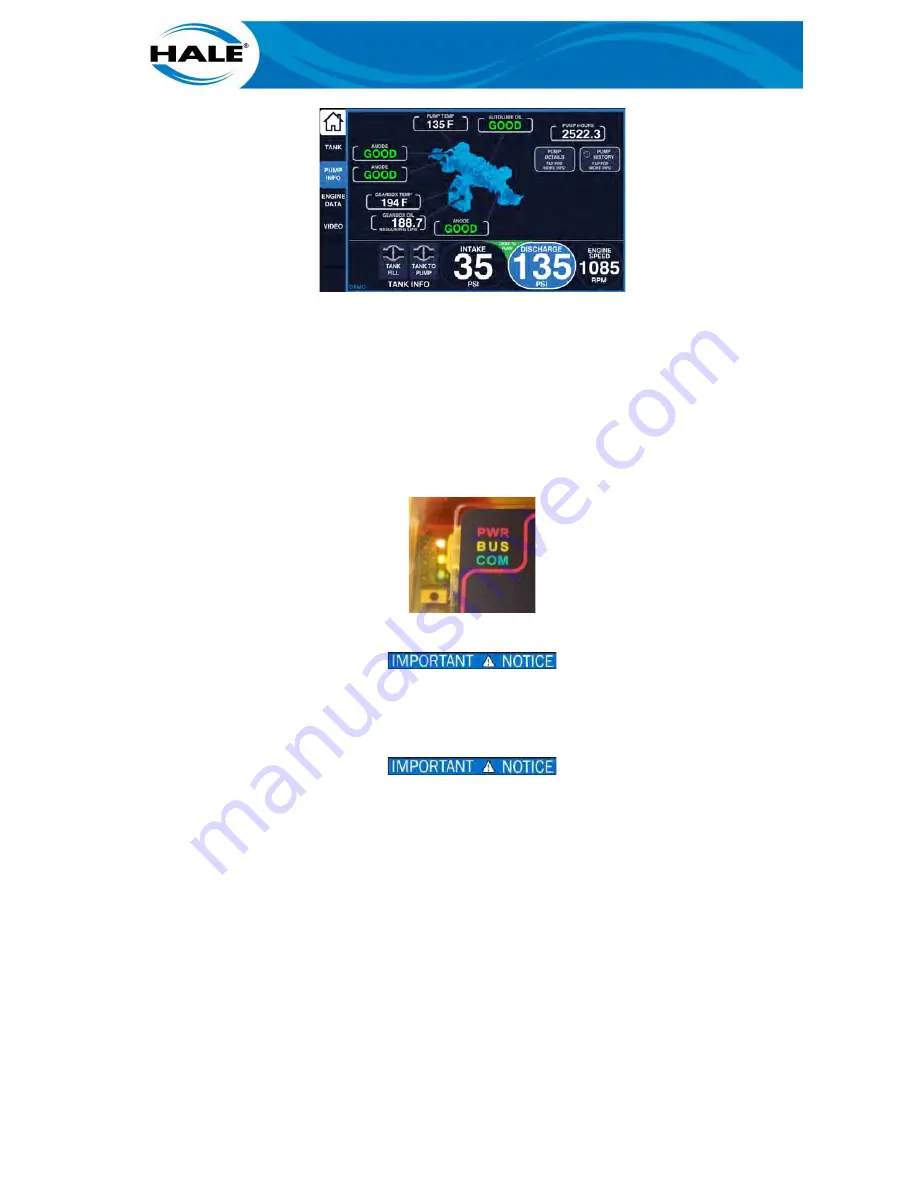
91
Figure 63. Indication Of Good Smart Anode
I.
Install cable ties cut to R&R sensor as noted.
4.8.
Removal And Replacement Of SAM Modules
All SAM modules provide a power (PWR), buss (BUS), and communication (COM) indication. See
Figure 64. Verify the red PWR, amber (BUS) and Green (COM) LEDs are illuminated steady. If the
Green (COM) LED is flashing slowly (2 Hz) the module is communicating with the CAN bus how-
ever the module is not receiving messages. If the Green (COM) LED is flashing fast (8 Hz) the
module is NOT able to communicate with the CAN bus.
Figure 64. Module Health Indicators
THE MODULE DEUTSCH CONNECTORS ARE KEYED TO PREVENT INTERCHANGE
(ON THAT MODULE) OR REVERSE DIRECTION INSERTION. DO NOT FORCE A CON-
NECTOR WITHOUT FIRST VERIFYING THE CONNECTORS ORIENTATION AND THE MAT-
ING MODULES LOCATION IS CORRECT.
THE MODULE DEUTSCH CONNECTORS ARE KEYED; HOWEVER, ALL MODULES UTILIZE
THE SAME TWO KEYS. VERIFY THE HARNESS LABEL AND THE MODULE PART NUMBER
TO ENSURE THE CORRECT MODULE AND HARNESS CONNECTOR ARE BEING CON-
NECTED.
The Class 1 modules utilized by the SAM/Sam system utilize keyed connectors. Each module has
an A keyed connector and a B keyed connector; however, all the SAM modules use the same A
and B keying. Therefore, module placement within the system (location on the mounting bracket)
is critical. See Figure 65.
Summary of Contents for Hale Sam
Page 2: ......
Page 37: ...17 Figure 14 SAM Blue CAN Buss Architecture With Three SAM Control Centers Diagram...
Page 38: ...18 Figure 15 SAM Green CAN Buss Architecture With Three SAM Control Centers Diagram...
Page 39: ...19 Figure 16 SAM Red CAN Buss Architecture With Three SAM Control Centers Diagram...
Page 40: ...20 Figure 17 SAM System Drain And Pneumatic Diagram...
Page 41: ...21 Figure 18 SAM Speaks Diagram...
Page 42: ......
Page 58: ...38 THIS PAGE INTENTIONALLY BLANK...
Page 62: ...42 THIS PAGE INTENTIONALLY BLANK...
Page 192: ...172 THIS PAGE INTENTIONALLY BLANK...
Page 206: ...186 THIS PAGE INTENTIONALLY BLANK...
Page 220: ...200 THIS PAGE INTENTIONALLY BLANK...