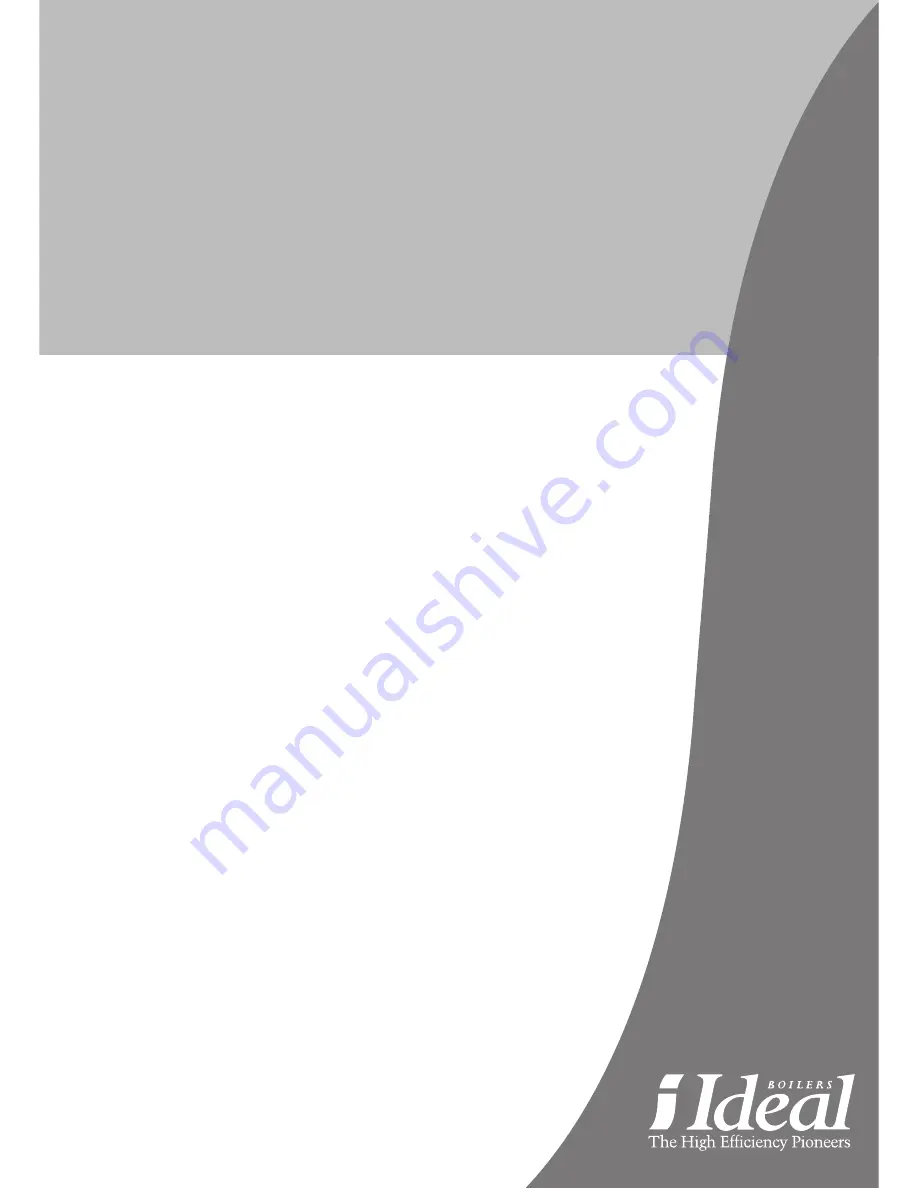
installation and
servicing
Your Ideal installation and servicing guide
When replacing any part on this appliance, use only spare parts that you can be
assured conform to the safety and performance specification that we require. Do not
use reconditioned or copy parts that have not been clearly authorised by Ideal Boilers.
Falcon GTS
GTS 4, GTS 5, GTS 6, GTS 7 & GTS 8
300013368-001-D