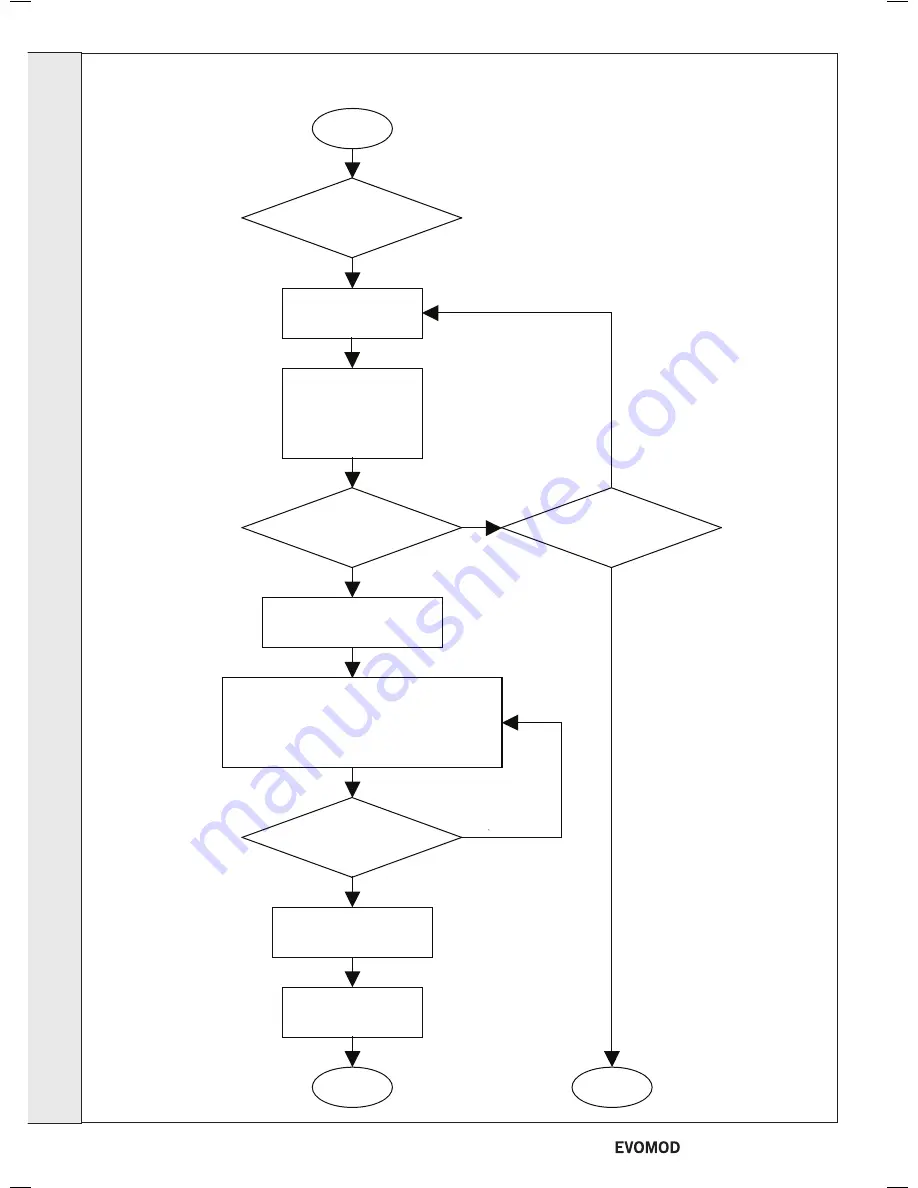
35 EVOMOD MODULE OPERATING SEQUENCE
out
Standby
Heat
Demand from Master
PCB On
Yes
Fan On
2 m ins Fan P r e-P u rge
Module Pump On
Spark Generator On
Gas Valve On
5s Ignition Per iod
Spark Generator Off
5s Stabi lisatio n Per iod
Burner Output controlled relative to
Heat Demand from Master PCB by
varying Fan Speed
Bur ner On
Heat
Demand from Master
PCB Off
Gas Valve Off
120s Pump Over r un
Fan Off
Module Pump Off
Yes
Standby
Flame Detected
Yes
Less
than 5 Ignition
Attempts
No
Yes
Lockout
No
Standby
Heat
Demand from Master
PCB On
Yes
Fan On
2 m ins Fan P r e-P u rge
Module Pump On
Spark Generator On
Gas Valve On
5s Ignition Per iod
Spark Generator Off
5s Stabi lisatio n Per iod
Burner Output controlled relative to
Heat Demand from Master PCB by
varying Fan Speed
Bur ner On
Heat
Demand from Master
PCB Off
Gas Valve Off
120s Pump Over r un
Fan Off
Module Pump Off
Yes
Standby
Flame Detected
Yes
Less
than 5 Ignition
Attempts
No
Yes
Lockout
No
INST
ALLA
TION
32
-
Installation & Servicing
INSTALLATION
Summary of Contents for EVOMOD 250
Page 59: ...59 Installation Servicing NOTES...
Page 60: ...60 Installation Servicing NOTES...