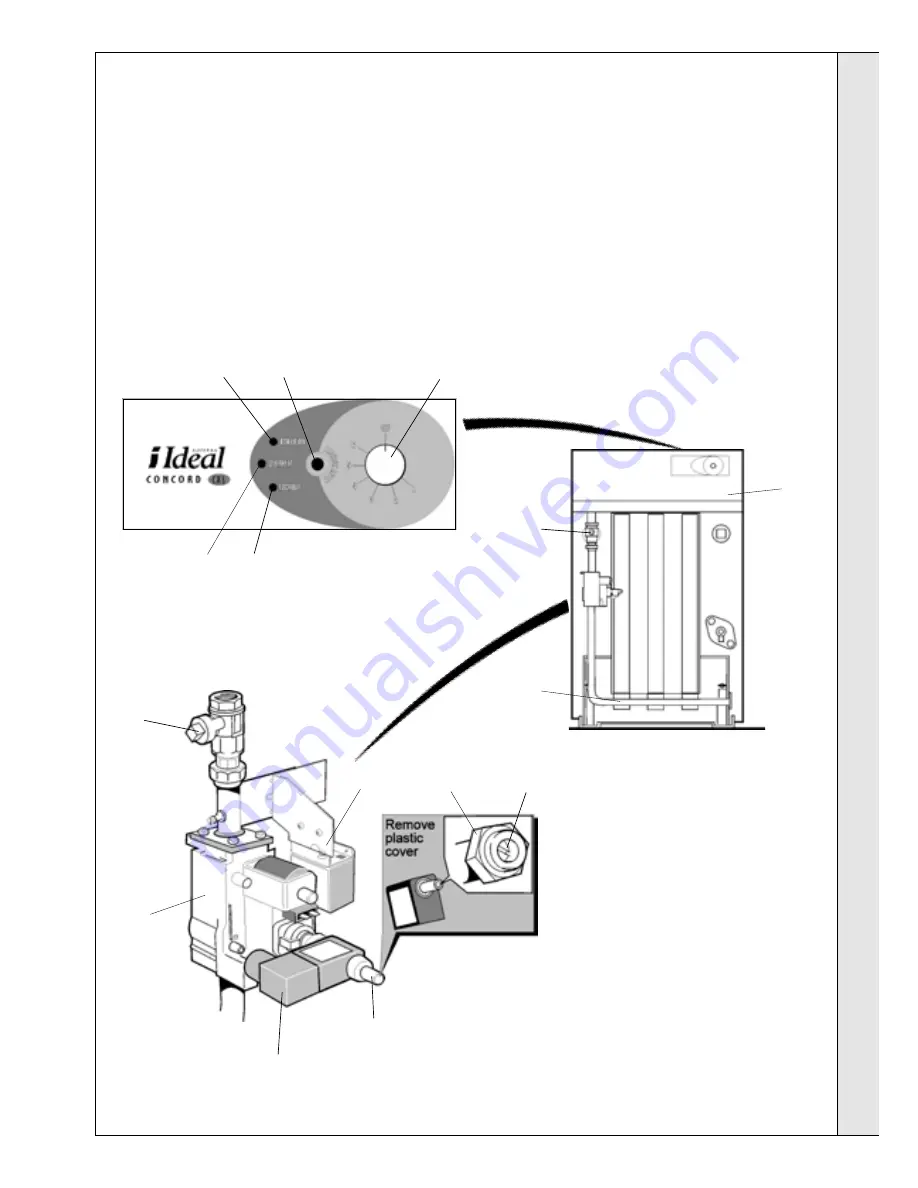
19
Concord CXS -
Installation & Servicing
LEGEND
1.
Thermostat knob
2.
Control box
3.
Mains inlet gas cock
4.
Overheat thermostat reset button
5.
Boiler on light
6.
Lockout light
7.
Lockout reset button
8.
Manifold pressure adjuster
9.
Gas control valve
10.
High burner pressure adjuster
11.
High/low solenoid electrical plug
12.
Low burner pressure adjuster
13.
Manifold pressure test point
14.
Overheat light
1.
Check that the boiler thermostat knob (1) on the control
box (2) is OFF.
2
. Ensure that the mains gas inlet cock (3) is open (groove in
the square head in line with the gas pipe).
3.
Press in and release the overheat thermostat button (4).
4.
Switch on the electrical supply to the boiler.
5.
Ensure that all system controls (time switch, system
controls etc.) are calling for heat.
6.
Turn the boiler thermostat knob (1) to position 6.
20 INITIAL LIGHTING
INSTALLATION
INST
ALLA
TION
CXS 40 - 90 boilers shown
7
. The boiler will light at Low rate and the Boiler-on light (5)
will be illuminated. If it does not light the Lockout light (6)
will be illuminated. Press in and release the Lockout
button (7). The controls will reset and attempt to relight.
8.
The burner will remain at Low rate for about 3 minutes
before going to High rate.
9.
Check all connections for gas soundness, using leak
detection fluid.
10.
Set the boiler thermostat knob and the system controls to
the required settings.
11.
Turn off the electrical supply to the boiler.
1
5
7
6
2
3
8
11
3
10
12
13
9
3
4
2
14