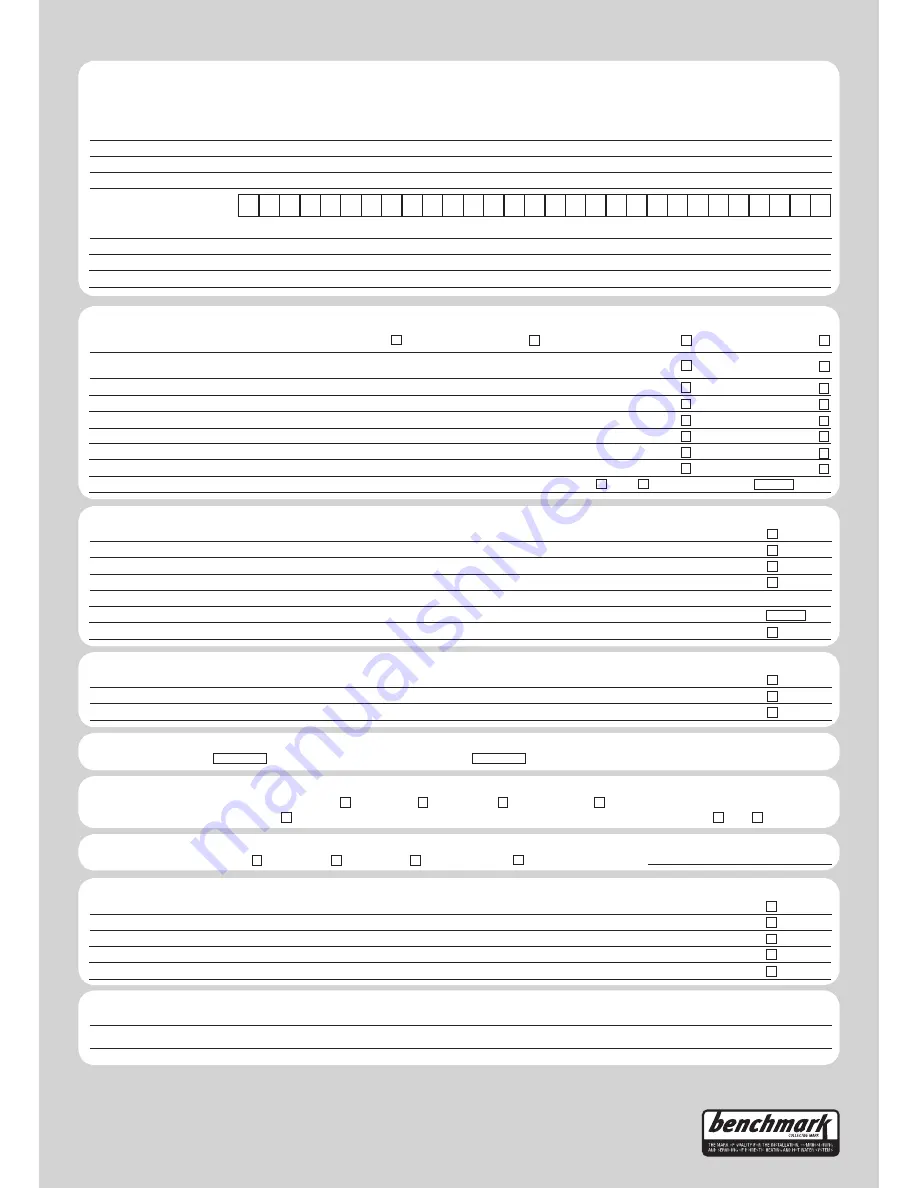
34
Ideal airtherm - Air Source Heat Pump -
Installation
Notes: [1] Installers should be members of an appropriate Competent Persons Scheme. [2] All installations in England and Wales must be
notified to Local Area Building Control (LABC) either directly or through a Competent Persons Scheme. A Building Regulations Compliance
Certificate will then be issued to the customer. [3] May be required for systems covered by G3 Regulations
© Heating and Hotwater Industry Council (HHIC)
www.centralheating.co.uk
AIR TO WATER HEAT PUMP COMMISSIONING CHECKLIST
This Commissioning Checklist is to be completed in full by the competent person who commissioned the heat pump and associated equipment as a means of
demonstrating compliance with the appropriate Building Regulations and then handed to the customer to keep for future reference.
Failure to install and commission this equipment to the manufacturer’s instructions may invalidate the warranty but does not affect statutory rights.
Customer Name
Address
Telephone Number
Heat Pump Make and Model
Heat Pump Serial Number
Commissioned by (print name)
Certified Operative Reg. No.
[1]
Company Name & Address
Commissioning Date
Telephone No.
Building Regulations Notification Number (if applicable)
[2]
Commissioning Engineer’s Signature
Customer’s Signature
(To confirm demonstration of equipment and receipt of appliance instructions)
ALL INSTALLATIONS
The heating, hot water and ventilation systems complies with the appropriate Building Regulations
Yes
All electrical work complies with the appropriate Regulations
Yes
The heat pump and associated products have been installed and commissioned in accordance with the manufacturer’s instructions
Yes
The operation of the heat pump and system controls have been demonstrated to the customer
Yes
The manufacturer’s literature, including Benchmark Checklist and Service Record, has been explained and left with the customer
Yes
CENTRAL HEATING MODE
Heating Flow Temperature °C Heating Return Temperature °C
ALL SYSTEMS
The heating system has been filled and pressure tested
Yes
Expansion vessel for heating is sized, fitted & charged in accordance with manufacturer’s instructions
Yes
The heat pump is fitted on a solid/stable surface capable of taking its weight
Yes
The system has been flushed and cleaned in accordance with BS7593 and heat pump manufacturer’s instructions
Yes
What system cleaner was used?
What inhibitor was used?
Qty litres
Is the system adequately frost protected?
Yes
OUTDOOR UNIT
Are all external pipeworks insulated?
Yes
Is the fan free from obstacles and operational?
Yes
Has suitable consideration been made for waste water discharge?
Yes
DOMESTIC HOT WATER MODE
Measure and Record
Is the heat pump connected to a hot water cylinder? Unvented Vented Thermal Store Not Connected
Hot water has been checked at all outlets Yes
Have Thermostatic Blending Valves been fitted?
Yes Not required
ADDITIONAL SYSTEM INFORMATON
Additional heat sources connected: Gas Boiler Oil Boiler Electric Heater Solar Thermal Other
CONTROLS - SYSTEM AND HEAT PUMP
Tick the appropriate boxes if applicable
1. Time & Temperature
Room Thermostat &
Programmable
Load/Weather
Optimum Start
Control to Heating
Programmer/Timer
Roomstat
Compensation
Control
2. Time & Temperature
Cylinder Thermostat &
Combined with Heat
Control to Hot Water
Programmer/Timer
pump main controls
3. Heating Zone Valves (including underfloor loops)
Fitted
Not Required
4. Hot Water Zone Valves
Fitted
Not Required
5. Thermostatic Radiator Valves
Fitted
Not Required
6. Heat Pump Safety Interlock
[3]
Built In
Provided
7. Outdoor Sensor
Fitted
Not Required
8. Automatic Bypass System
Fitted
Not Required
9. Buffer Vessel Fitted
Yes
No If YES, Volume Litres