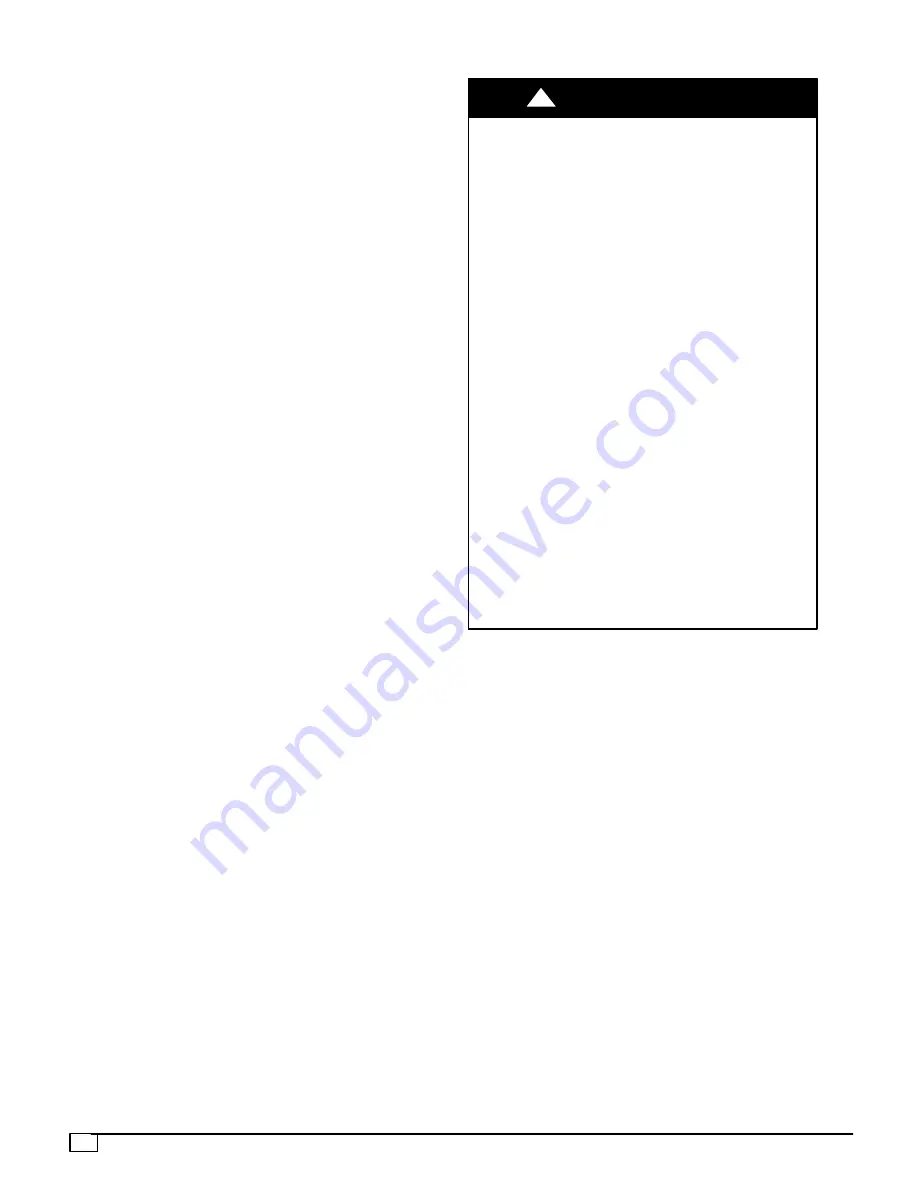
12
Run the low--voltage leads from the thermostat, through the
inlet hole, and into unit low--voltage splice box.
Locate five 18--gage wires leaving control box. These
low--voltage connection leads can be identified by the
colors red, green, yellow, brown, and white (See Fig. 10).
Ensure the leads are long enough to be routed into the
low--voltage splice box (located below right side of control
box). Route leads through hole in bottom of control box and
make low--voltage connections (See Fig. 10). Secure all cut
wires, so that they do not interfere with operation of unit.
HEAT ANTICIPATOR SETTING
The room thermostat heat anticipator must be properly
adjusted to ensure proper heating performance. Set the
heat anticipator, using an ammeter between the W and R
terminals to determine the exact required setting.
NOTE
: For thermostat selection purposes, use 0.18 amp
for the approximate required setting. Failure to make a
proper heat anticipator adjustment will result in improper
operation, discomfort to the occupants of the conditioned
space, and inefficient energy utilization; however, the
required setting may be changed slightly to provide a
greater degree of comfort for a particular installation.
TRANSFORMER PROTECTION
The transformer is of the energy--limiting type. It is set to
withstand a 30--sec. overload or shorted secondary
condition. If an overload or short is present, correct
overload condition and check for blown fuse on gas control
board. Replace fuse as required with correct size.
PRE--START--UP
FIRE, EXPLOSION, ELECTRICAL SHOCK HAZARD
Failure to follow this warning could result in personal
injury or death.
1. Follow recognized safety practices and wear
protective goggles when checking or servicing
refrigerant system.
2. Do not operate compressor or provide any electric
power to unit unless compressor terminal cover is in
place and secured.
3. Do not remove compressor terminal cover until all
electrical sources are disconnected and tagged.
4. Relieve and recover all refrigerant from system
before touching or disturbing anything inside
terminal box if refrigerant leak is suspected around
compressor terminals.
5. Never attempt to repair soldered connection while
refrigerant system is under pressure.
6. Do not use torch to remove any component. System
contains oil and refrigerant under pressure.
To remove a component, wear protective goggles
and proceed as follows:
a. Shut off electrical power to unit and install
lockout tag.
b. Relieve and reclaim all refrigerant from
system using both high-- and low--pressure
ports.
c. Cut component connecting tubing with tubing
cutter and remove component from unit.
d. Carefully unsweat remaining tubing stubs
when necessary. Oil can ignite when exposed
to torch flame.
!
WARNING
Use the Start--Up Checklist supplied at the end of this book
and proceed as follows to inspect and prepare the unit for
initial start--up:
1. Remove access panel.
2. Read and follow instructions on all DANGER,
WARNING, CAUTION, and INFORMATION labels
attached to, or shipped with unit.
3. Make the following inspections:
a.
Inspect for shipping and handling damage, such as
broken lines, loose parts, disconnected wires, etc.
b.
Inspect for oil at all refrigerant tubing connections
and on unit base. Detecting oil generally indicates
a refrigerant leak.
c.
Leak--test all refrigerant tubing connections using
electronic leak detector, or liquid--soap solution. If
a refrigerant leak is detected, see following Check
for Refrigerant Leaks section.
d.
Inspect all field-- and factory--wiring connections.
Be sure that connections are completed and tight.
e.
Ensure wires do not touch refrigerant tubing or
sharp sheet metal edges.
f.
Inspect coil fins. If damaged during shipping and
handling, carefully straighten fins with a fin comb.