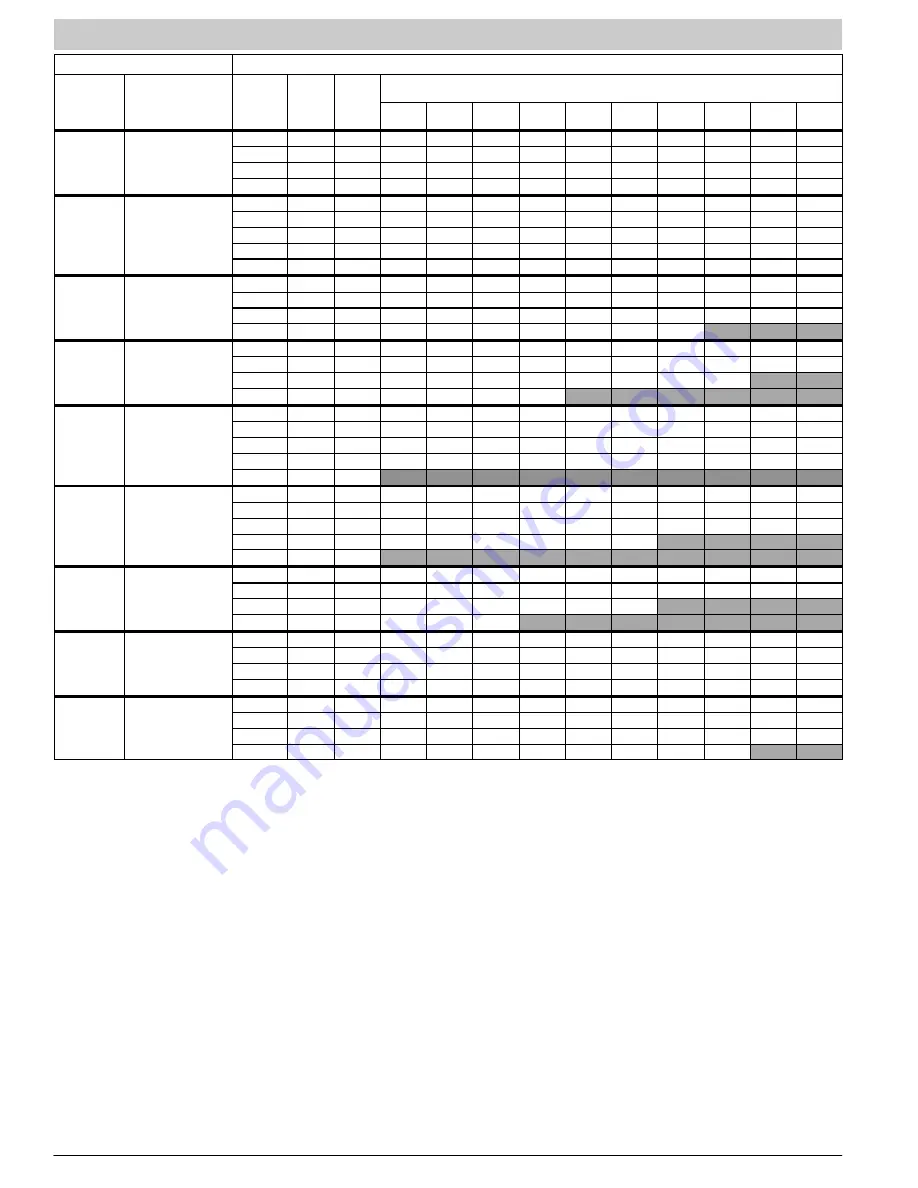
SERVICE AND TECHNICAL SUPPORT MANUAL
Gas Furnace: N9MSB
Specifications subject to change without notice.
14
440 04 4413 03
Table 5
COOLING AIR DELIVERY - CFM (with filter
1
)
SIZE
RETURN
AIR
CONNECTION
WIRE
LEAD
COLOR
COOL
-
ING
TONS
CFM
/TON
TEST
AIRFLOW
DELIVERY
@
VARIOUS
EXTERNAL
STATIC
PRESSURES
0.1
0.2
0.3
0.4
0.5
0.6
0.7
0.8
0.9
1
401410
SIDE/BOTTOM
Black
2.5
388
1145
1100
1060
1015
970
920
860
785
680
615
Blue
2.0
413
970
940
905
870
825
775
730
675
570
505
Yellow
2.0
385
910
880
845
810
770
725
675
600
535
475
Red
1.5
397
725
695
665
635
595
555
510
460
390
340
401712
SIDE/BOTTOM
Black
3.0
380
1365
1310
1255
1200
1140
1080
1015
950
860
795
Yellow
2.5
418
1245
1200
1150
1100
1045
990
930
855
790
730
Orange
2.5
366
1050
1025
985
950
915
870
820
760
705
655
Blue
2.0
435
980
955
935
905
870
830
780
725
675
625
Red
1.5
437
720
705
690
675
655
625
590
555
525
485
601412
SIDE/BOTTOM
Black
3.0
385
1215
1205
1205
1195
1155
1100
1045
975
910
805
Blue
2.5
370
980
985
980
955
925
880
835
780
695
585
Yellow
2.0
425
910
920
905
880
850
815
765
695
630
545
Red
3
1.5
430
750
730
705
680
645
605
555
490
435
370
601716
SIDE/BOTTOM
Black
4.0
376
1600
1545
1505
1475
1505
1445
1400
1330
1235
1140
Yellow
3.5
377
1380
1340
1335
1330
1320
1285
1225
1155
1085
1000
Blue
3
3.0
387
1190
1185
1195
1195
1160
1125
1075
1015
950
885
Red
3
2.5
394
1030
1025
1030
1010
985
940
905
855
805
735
801716
SIDE/BOTTOM
Black
4.0
408
1800
1770
1735
1685
1630
1570
1495
1415
1330
1230
Yellow
3.5
386
1445
1430
1410
1385
1350
1305
1255
1195
1120
1045
Orange
3.0
390
1250
1240
1225
1200
1170
1130
1090
1040
975
910
Blue
2.5
404
1090
1080
1060
1035
1010
970
930
885
835
765
Red
3
2.0
390
880
860
835
810
780
750
710
665
615
560
802120
BOTTOM or
TWO
−
SIDES
4,5
Black
5.0
377
2225
2160
2070
1980
1885
1790
1690
1575
1460
1345
Yellow
4.0
386
1690
1665
1640
1595
1545
1485
1410
1330
1235
1135
Orange
3.5
397
1485
1470
1455
1430
1390
1340
1280
1205
1120
1035
Blue
3
2.5
426
1120
1110
1100
1090
1065
1035
990
935
870
805
Red
3
2.0
433
940
920
910
890
865
830
790
745
690
625
1002116
SIDE/BOTTOM
Black
4.0
373
1715
1660
1610
1555
1490
1420
1340
1245
1150
1065
Yellow
3
3.5
379
1535
1480
1435
1380
1325
1260
1180
1095
1010
910
Blue
3
3.0
367
1300
1255
1205
1160
1100
1035
970
905
810
730
Red
3
2.0
445
1110
1055
1005
955
890
835
770
690
610
535
1002120
BOTTOM or
TWO
−
SIDES
4,5
Black
5.0
394
2270
2205
2130
2055
1970
1880
1780
1670
1555
1425
Yellow
5.0
367
2090
2040
1980
1910
1835
1755
1670
1570
1460
1340
Blue
4.0
416
1850
1815
1775
1725
1665
1600
1525
1435
1335
1225
Red
3.5
421
1580
1550
1540
1515
1475
1420
1355
1280
1190
1100
1202420
BOTTOM or
TWO
−
SIDES
4,5
Black
5.0
410
2385
2310
2230
2150
2050
1920
1780
1650
1540
1415
Yellow
5.0
369
2130
2070
2010
1940
1845
1740
1630
1525
1420
1305
Blue
4.0
416
1875
1840
1795
1735
1665
1580
1495
1410
1310
1205
Red
3
3.5
414
1610
1585
1555
1515
1450
1395
1325
1250
1160
1080
NOTES:
1. A filter is required for each return
−
air inlet. Airflow performance includes a 3/4 in. (19 mm) washable filter media such as contained in factory
−
authorized accessory filter rack. See accessory list. To determine airflow performance without this filter, assume an additional 0.1 in. W.C.
available external static pressure.
2. ADJUST THE BLOWER SPEED TAPS AS NECESSARY FOR THE PROPER AIR TEMPERATURE RISE FOR EACH INSTALLATION.
3. Shaded areas indicate that this airflow range is BELOW THE RANGE ALLOWED FOR HEATING OPERATION. THESE AIRFLOW RANGES
MAY ONLY BE USED FOR COOLING.
4. Airflows over 1800 CFM require bottom return, two
−
side return, or bottom and side return. A minimum filter size of 20” x 25” is required.
5. For upflow applications, air entering from one side into both the side of the furnace and a return air base counts as a side and bottom return.
6. All airflows that are shown in BOLD exceed 0.58 Watts per CFM at the given external static pressure.