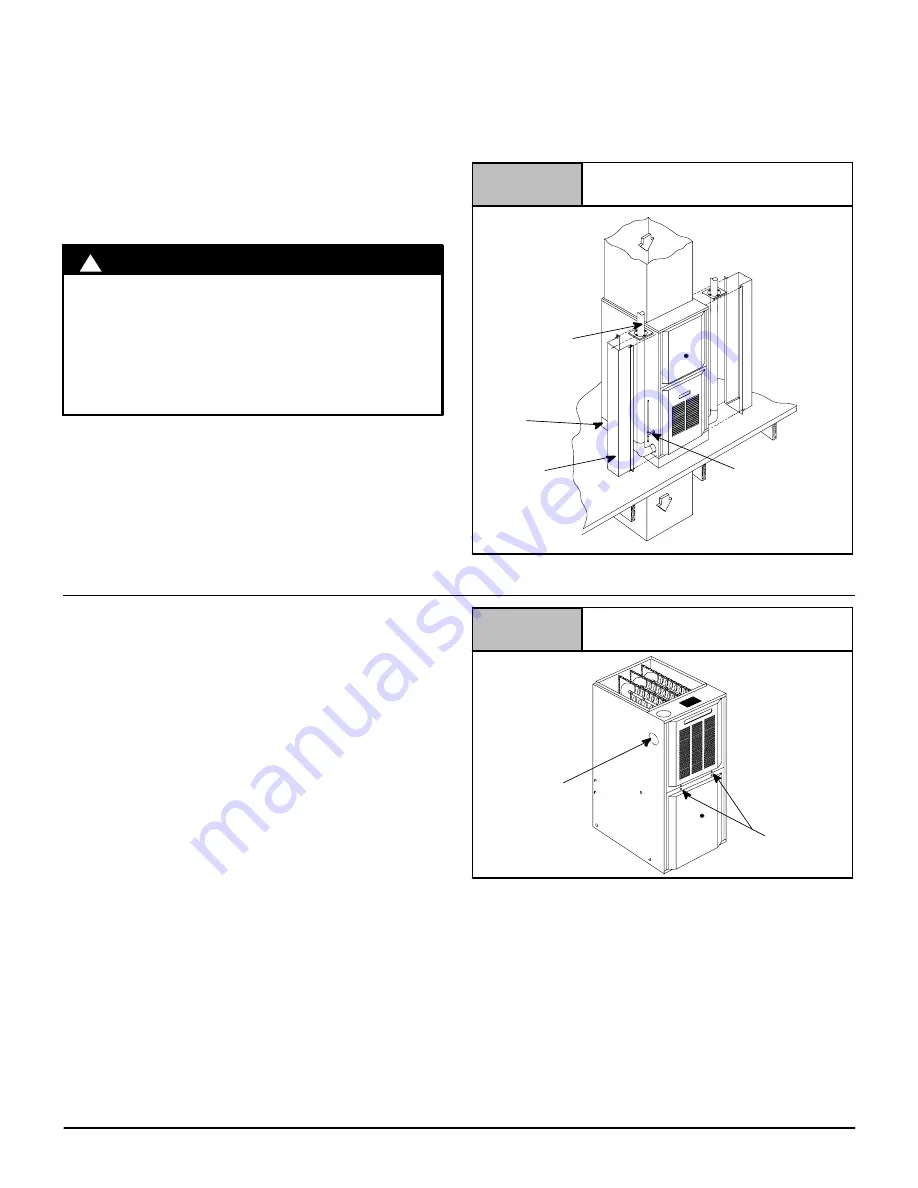
441 01 2613 06
9
Specifications are subject to change without notice.
2. Turn the logo rightside
−
up, and install the logo retainer pins
into holes in burner compartment door.
3. New labels for rightside
−
up application on outside of blower
compartment door may be purchased in a kit from your
distributor to cover upside
−
down labels.
Downflow Venting:
The combustion venter
MUST
be rotated to
vent out the side for all downflow installations, (see
Figure 5
)
.
Bottom venting is not permitted. See “
Side venting”
for
instructions to rotate the vent to the side. In addition to rotating the
vent to the side a
Vent Pipe Shield (NAHA002VC)
is required to
shield the hot vent pipe.
!
BURN HAZARD
Failure to follow this warning could result in
personal injury and/or property damage.
Vent pipe is HOT and could cause personal injury.
Hot vent pipe is in reach of small children when
installed in downflow position.
Install vent pipe shield NAHA002VC.
WARNING
Pressure Switch Relocation
If the furnace is installed in the upflow position, the pressure switch
will remain in the same position as installed by the factory unless
the inducer is rotated. If the furnace is installed in an orientation
that places the pressure switch below the pressure tap on the
inducer housing, then the switch
MUST
be relocated. In order to
relocate the switch, locate 2 mounting holes or drill above the
inducer pressure tap. When drilling the 2 holes make sure to keep
the switch and tubing far enough away from the burners or hot
surfaces as to not melt the hose, switch, or wires. To prevent
possible kinking of the pressure switch hose, trim the hose to
remove excess length.
Note: When drilling new holes make sure metal shavings do not fall
on or in components, as this can shorten the life of the furnace.
See side venting
for venter rotation
Typical Downflow Installation
Figure 5
VENT
GAS SUPPLY
MUST BE OPPOSITE
VENT DISCHARGE
SIDE
SUPPLY
AIR
RETURN
AIR
OPTIONAL
VENT
25
−
23
−
19
Combustible floor
base outlet flange
adapter
Vent Shield
Kit
3. Side Venting
This furnace is shipped from the factory with the venter assembly
in an upflow configurations (top vent). The venter assembly can
easily be rotated to a side vent configuration for use in upflow,
horizontal
−
flow, or downflow application.
When using a side vent configuration (side outlet instead of top
outlet), it may be necessary to relocate the pressure switch to the
alternate position on the opposite side of the top panel. Two screw
holes are provided at the alternate position. Route the pressure
switch tubing so the tubing is not kinked and not touching the hot
collector box, venter housing, or motor. It may be necessary to
shorten the length of the tubing to properly route the tubing and
eliminate kinks.
Rotating the Venter Assembly
1. If gas and electrical power have already been connected to
unit shut off gas and remove power from unit. Unscrew screws
on burner compartment door and remove burner compartment
door. (see
Figure 6
)
.
2. Disconnect power leads to the venter motor and hose to
pressure switch. Remove three (3) or four (4) screws which
secure the venter to the collector box, (see
Figure 7
).
3. Cut webbing with a pair of snips holding the vent plate to the
cabinet on either the left or right side of unit depending on right
or left venting as desired. Discard vent plate, (see
Figure 6
).
4. Replace venter gasket (part # 1013540, if needed) to venter
assembly with adhesive in the same location as the old one.
5. Clip the wire tie for the venter wires, if needed.
6. Rotate venter assembly 90
°
right or left from original location
depending on venting configurations.
Figure 6
25
−
23
−
45
Screws (2)
Furnace with Screws
Vent Plate