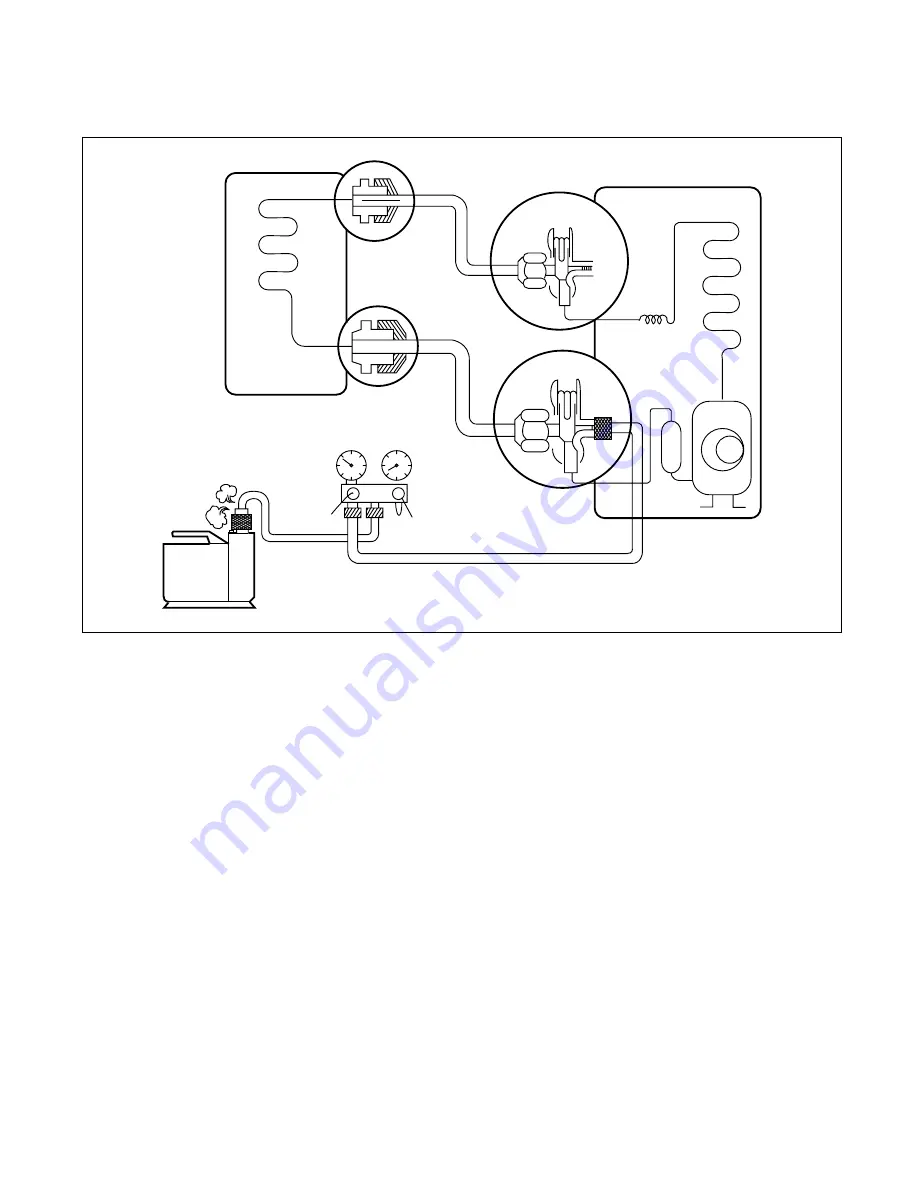
- 46 -
2. Evacuation
(All amount of refrigerant leaked)
• Procedure
(1) Connect the vacuum pump to the center hose
of charge set center hose
(2) Evacuation for approximately one hour.
– Confirm that the gauge needle has moved
toward -76 cmHg (vacuum of 4 mmHg or less).
(3) Close the valve (Lo side) on the charge set,
turn off the vacuum pump, and confirm that
the gauge needle does not move (approxima-
tely 5 minutes after turning off the vacuum
pump).
(4) Disconnect the charge hose from the vacuum
pump.
– Vacuum pump oil.
If the vacuum pump oil becomes dirty or
depleted, replenish as needed.
Lo
Open
Open
Vacuum pump
3-Way
valve
Outdoor unit
Liquid side
Indoor unit
Gas side
3-Way
valve
CLOSE
OPEN
Summary of Contents for HMC030KD1
Page 55: ...55 Electronic Control Device 1 INDOOR UNIT P W B ASSEMBLY P No 6871A10153 PCB ASSEMBLY MAIN...
Page 56: ...56 TOP VIEW BOTTOM VIEW 2 OUTDOOR UNIT P W B ASSEMBLY...
Page 57: ...57 3 DISPLAY P W B ASM Model HMC030KD1 HMH030KD1...
Page 58: ...58 Schematic Diagram 1 Heat Pump Cooling Only Series Indoor Unit...