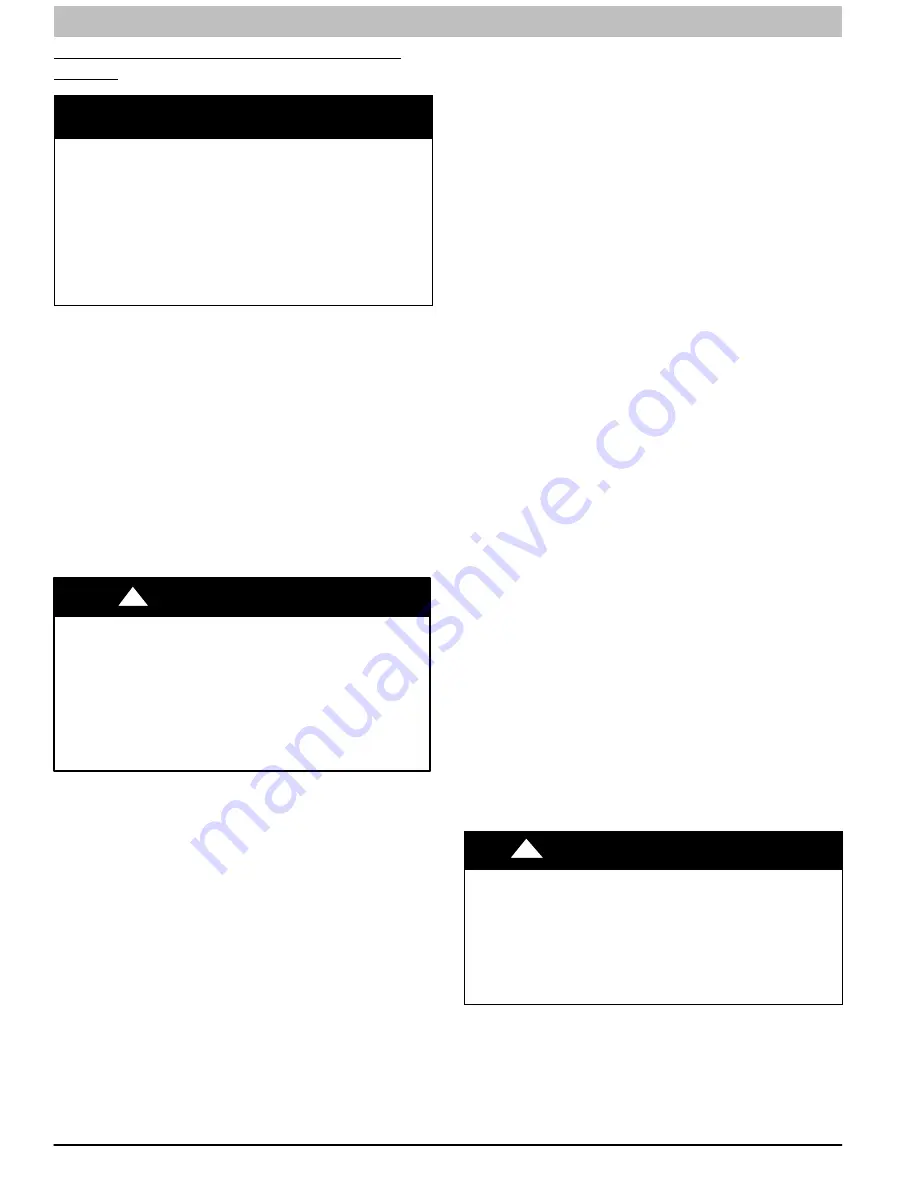
SERVICE AND TECHNICAL SUPPORT MANUAL
Gas Furnace: (F/G)9MVE
Specifications subject to change without notice.
4
440 04 4801 03
START
−
UP, ADJUSTMENT, AND SAFETY
CHECK
NOTICE
IMPORTANT INSTALLATION AND START
−
UP
PROCEDURES
Failure to follow this procedure may result in a nuisance smoke
or odor complaint.
The manifold pressure, gas rate by meter clocking, temperature
rise and operation must be checked after installation. Minor
smoke and odor may be present temporarily after start
−
up from
the manufacturing process. Some occupants are more
sensitive to this minor smoke and odor. It is recommended that
doors and windows be open during the first heat cycle.
General
1. Furnace must have a 115-v power supply properly
connected and grounded.
NOTE
: Proper polarity must be maintained for 115-v wiring.
Control status indicator light flashes code 10 and furnace does
not operate if polarity is incorrect or if the furnace is not
grounded.
2. Thermostat wire connections at terminals R, W/W1, G,
and Y/Y2 must be made at 24-v terminal block on
furnace control.
3. Natural gas service pressure must not exceed 0.5 psig
(14- in. w.c., 350 Pa), but must be no less than 0.16 psig
(4.5-in. w.c., 1125 Pa).
4. Blower door must be in place to complete 115-v electrical
circuit and supply power to furnace components.
UNIT OPERATION HAZARD
Failure to follow this caution may result in intermittent unit
operation or performance satisfaction.
These furnaces are equipped with a manual reset limit
switch in burner assembly. This switch opens and shuts
off power to the gas valve if an overheat condition (flame
rollout) occurs in burner assembly. Correct inadequate
combustion
−
air supply or improper venting condition
before resetting switch. DO NOT jumper this switch.
CAUTION
!
Before operating furnace, check flame rollout manual reset
switch for continuity. If necessary, press button to reset switch.
EAC-1 terminal is energized whenever blower operates. HUM
terminal is only energized when blower is energized in heating.
Setup Switches
There are four sets of setup switches on the furnace control
board. These switches configure the furnace for correct
application requirement. They also select the airflow settings for
Air Conditioning and Continuous Fan CFM.
The Setup Switch locations are shown and described on
,
.
The setup switches are also
shown on the unit wiring label.
Setup Switches (SW1)
The furnace control has 8 setup switches that may be set to
meet the application requirements. To set these setup switches
for the appropriate requirement:
1. Remove blower door.
2. Locate setup switches on furnace control.
3. Configure the set-up switches as necessary for the
application.
4. Replace blower door.
NOTE
: If a bypass humidifier is used, setup switch SW1-3
(Low Heat Rise Adjust) should be in ON position. This
compensates for the increased temperature in return air
resulting from bypass.
Setup Switch (SW2)
Setup switches SW2 are used for applications used for
Twinning two furnaces of the same model and BTU’s and to
adjust airflow. SW2
−
2 is used to adjust airflow. Refer to the
Adjustments section for set up switch configurations. Refer to
for configuration of SW2 airflow options.
1. Remove blower door.
2. Locate setup switch SW2 on furnace control.
3. Configure the switches as necessary for the application.
4. Replace blower door.
Continuous Fan (CF) Setup Switches (SW2
−
5,
SW2
−
4, SW2
−
3)
The CF setup switches are used to select desired airflow when
thermostat is in continuous fan mode or to select low-cooling
airflow for two-speed cooling units. Refer to the Adjustments
section for set up switch configurations.
To set the desired cooling airflow:
1. Remove blower door.
2. Locate CF setup switches on furnace control.
3. Determine air conditioning tonnage used for low cooling
(when used) or desired continuous fan airflow.
4. Configure the switches for the required airflow.
5. Replace blower door.
Air Conditioning (A/C) Setup Switches (SW2
−
6,
SW2
−
7, SW2
−
8)
The air conditioning setup switches are used to match furnace
airflow to required cooling airflow or high stage cooling airflow
when a two
−
stage outdoor unit is used. Refer to the
Adjustments section for set up switch configurations.
To set the desired cooling airflow:
1. Remove blower door.
2. Locate A/C setup switches on furnace control.
3. Determine air conditioning tonnage used.
4. Configure the switches for the required cooling airflow.
5. Replace blower door.
NOTE
: Incorrect airflow caused by improper A/C switch setup
may cause condensate blow-off or frozen indoor coil in the
cooling mode.
Prime Condensate Trap with Water
!
WARNING
CARBON MONOXIDE POISONING HAZARD
Failure to follow these warnings could result in personal injury
or death.
Failure to use a properly configured trap or NOT
water-priming trap before operating furnace may allow
positive pressure vent gases to enter the structure through
drain tube. Vent gases contain carbon monoxide which is
tasteless and odorless.