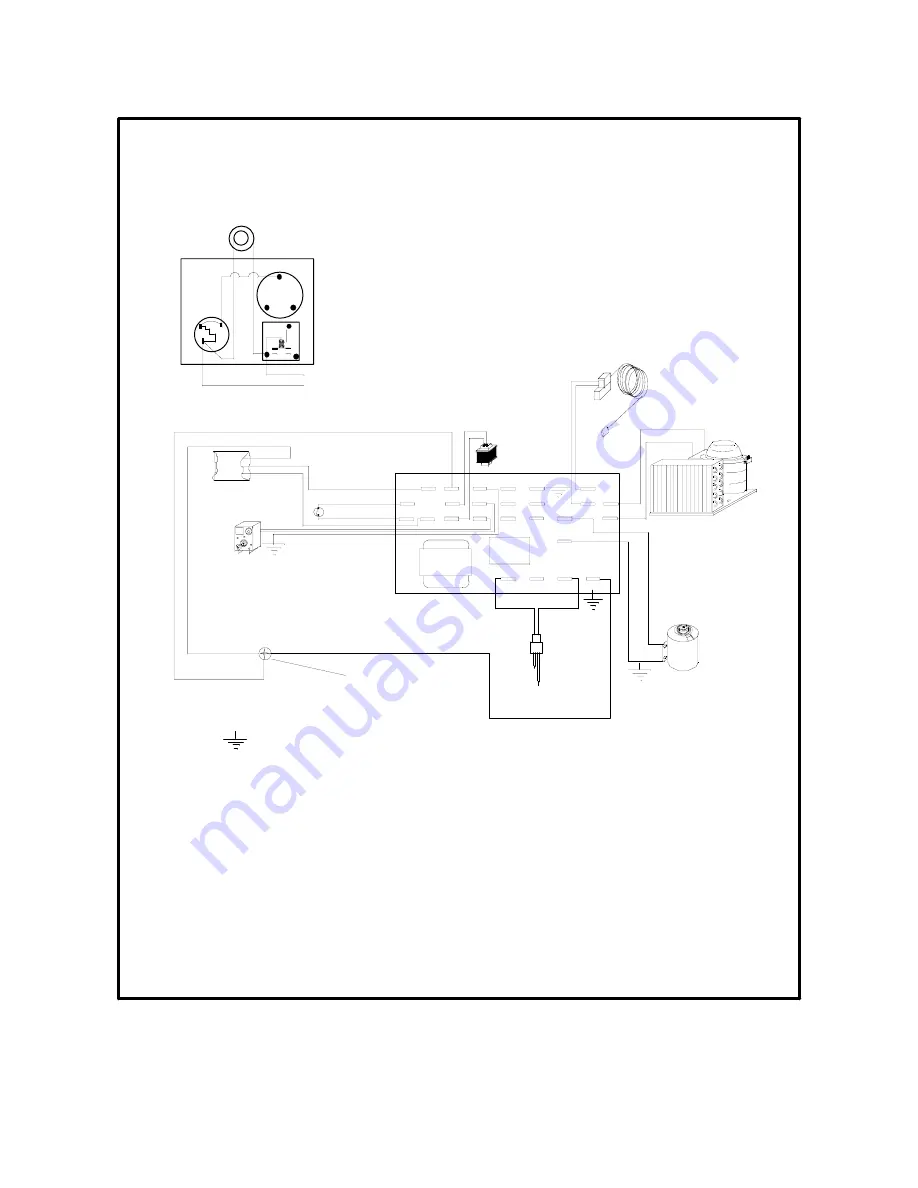
INTERNATIONAL CARBONIC INC.
ON/OFF
POWER
G1
G2
G3
G4
IBC1
IBC2 CU1
CU2
B1
B2
B3
B4
B5
MOTOR1
MOTOR2
SHORT
LONG GND
ON/OFF
A2
A3
A4
A5
S
-68-B
GREEN
BLACK
WHITE
ON/OFF
TRANSFORMER
CARB
MOTOR/PUMP
CONDENSING
UNIT
AGITATOR PUMP
ELECTRODE
WHITE
BLACK
BLACK
WHITE
Note: Ground Terminals, Carbonator Tank
and Water Bath Must be
Commonly Grounded
120 VAC
GREEN
GREEN
GREEN
GREEN
GREEN
ELECTRICAL SCHEMATIC 120 VOLT
NOTE: IF USING EXTRA 120V. ACCESSORIES SUCH AS RECIRCULATING MOTOR, ILLUMINATION
ETC., MAKE CONNECTIONS AT TERMINAL A4, A5 FOR POWER/BLACK LEG. TERMINALS B4, B5,
FOR NEUTRAL/WHITE LEG AND GROUND AT BOX OR ANY GROUND TERMINAL NOT IN USE.
TERMINALS
ICE BANK CONTROL
GROUND TERMINALS ARE G1, G2, G3, G4.
S-68-B
GROUND TERMINAL SCREW IN
CONTROL BOX
S
C
R
M
S
1
3
1
FAN MOTOR
COMPRESSOR
FIGURE 1-5
1-8