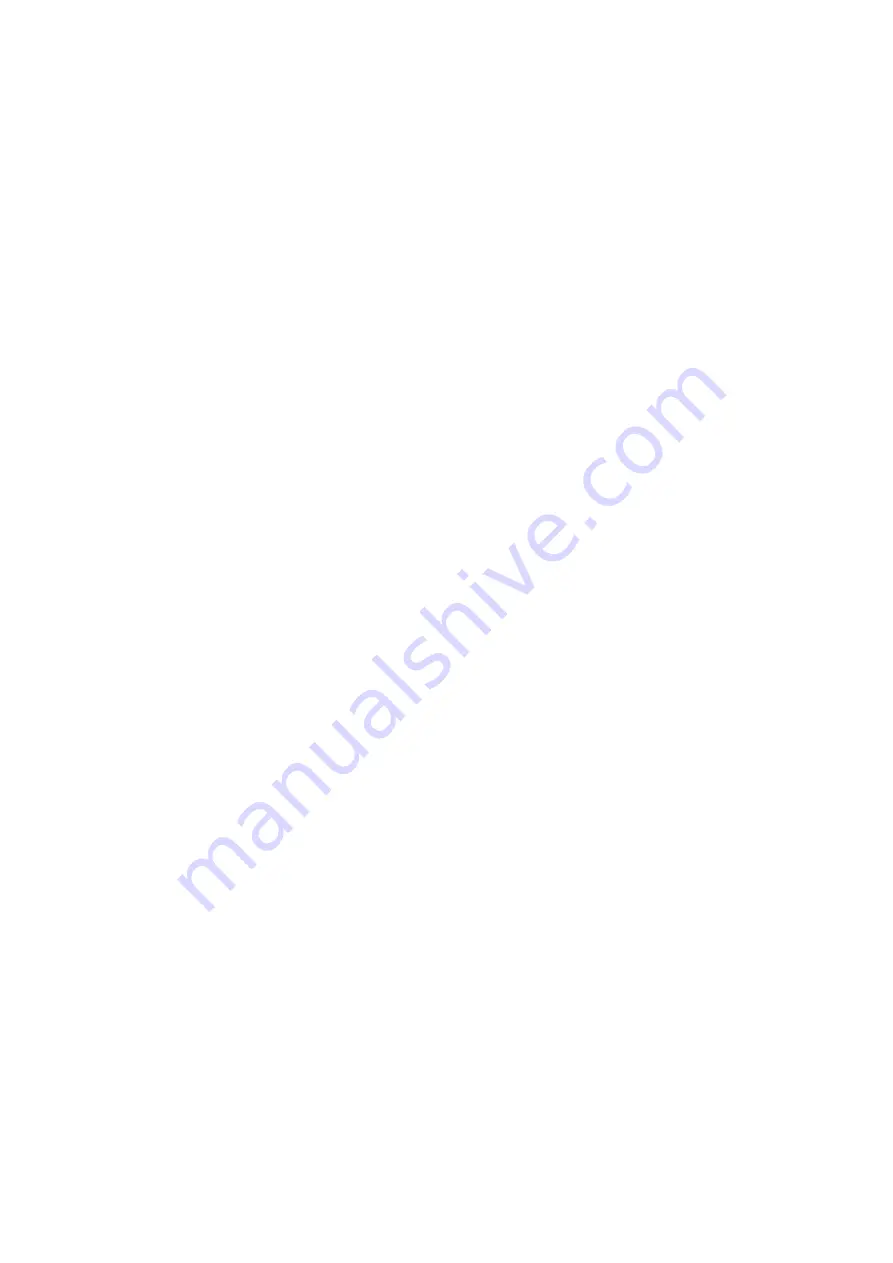
Boiler welding
22
SYSTEM FILLING AND EMPTYING
FILLING
–
Before filling the system, disconnect the power supply by positioning the system main switch to “
OFF
” and check that the
drain valve of the boiler is closed
–
open the filling valve of the boiler and the shut-off valve of the water system and allow the water to enter slowly, in quantities
proportional to the venting capacity of the automatic or manual air separators, and until the expansion vessel pre-filling static
pressure value can be read on the manometer
–
close the previously opened boiler filling valve and the water system filling valve
–
heat the water for the first time until reaching the system maximum permitted temperature. During this operation, the air
contained in the water is vented through the system’s automatic or manual air separators
–
once the air has been expelled, bring the pressure back to the preset value and close the manual and/or automatic supply tap.
–
After the initial filling, it is necessary to prevent oxygen and untreated water from entering the system.
–
The entry of oxygen causes corrosion, while untreated water causes the formation of limestone.
–
Both conditions must be avoided.
NOTE
The system venting will be completed, if necessary, upon the first commissioning of the boiler.
EMPTYING
–
Before starting to empty the system, disconnect the power supply by positioning the system main switch to “
OFF
”
–
check that the hydraulic system shut-off valve is closed
–
connect a rubber hose to the drain valve of the boiler and convey it towards a drain pocket
–
close the shut-off devices of the thermal system parts which must not be emptied
–
slowly open the boiler drain valve. To facilitate the draining, open the air separators on the system
–
once the operation is complete, close the previously opened air separators and the drain valve.
Cooke Industries - Phone: +64 9 579 2185 Email: [email protected] Web: www.cookeindustries.co.nz