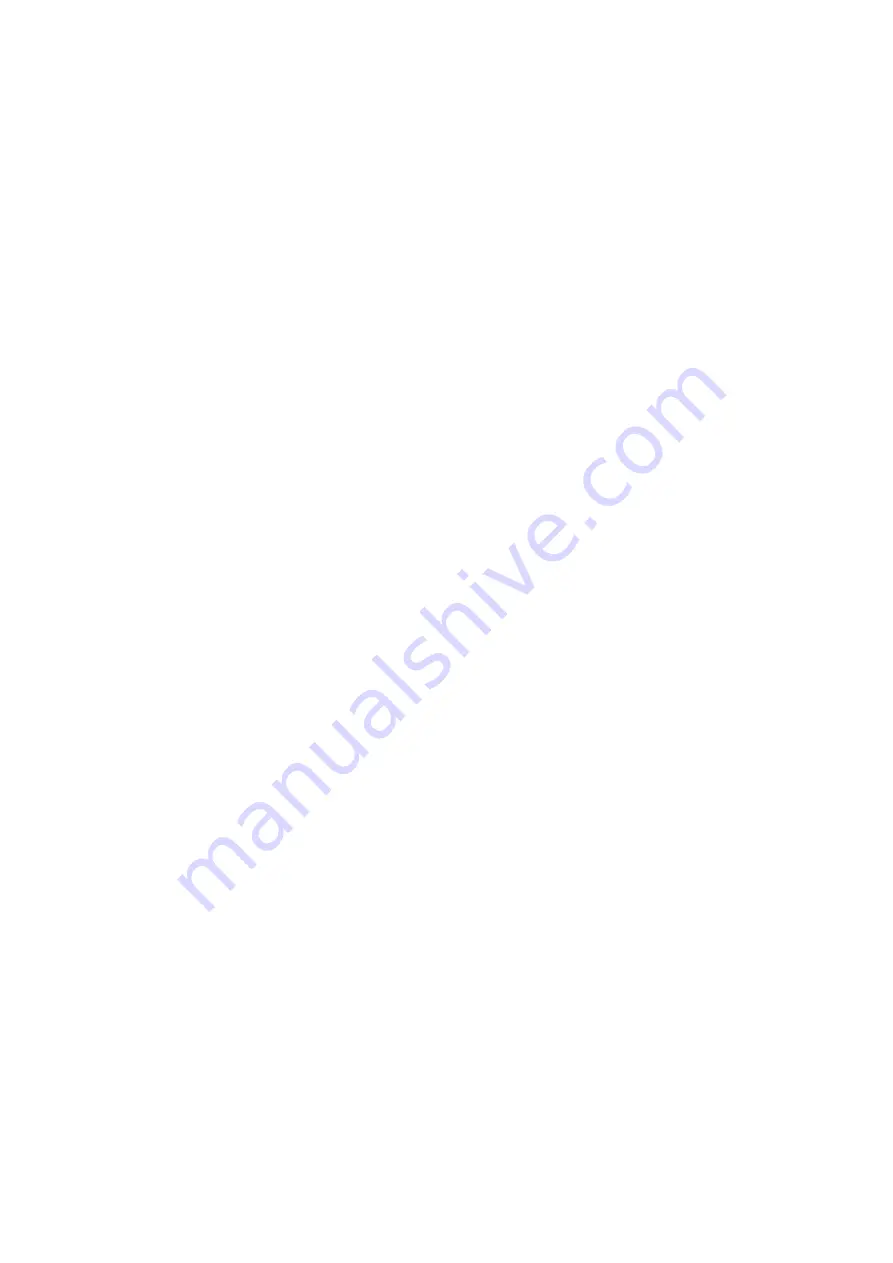
Residual Risk Management
40
5
Residual Risk Management
EXCESSIVE STEAM PRESSURE
–
Make sure the safety valves properly open at the design pressure.
–
It is necessary to check the correct activation of the shut-off pressure switch that eliminates the cause of pressure increase by
stopping the burner.
–
The matching between the boiler maximum flow thermal and the actual burned maximum power must be checked.
ACCESSORY BREAKAGE
–
Check the correct connection of the accessories to the boiler body (gasket seal check).
–
Take special care during handling and installation.
–
Periodically check the condition of the same accessories (exclusion of fractures).
–
Once installation is completed, check safety valve correct activation through the special lever and/or the pressure increase
above the calibration value.
OVERHEATING DUE TO LOW WATER LEVEL
–
The correct operation of the safety level switch must be checked in accordance with the indications set forth in the technical
manual.
–
It is necessary to check that the operating water conductivity values are within those provided in the supplied technical
manual.(EN 12953-10)
–
Make sure the water loading pump is working properly as described in the technical manual provided with the boiler (pump
wear, hydrostatic head in suction, water supply temperature, pump connection/disconnection from the level control probes).
OVERHEATING DUE TO THERMAL INERTIA
–
Position of water minimum level 100 mm above the highest point of the heated surface.
–
Calculation ensuring that the evaporation caused by refractory material thermal inertia does not uncover the highest point of
the heated surface.
OVERHEATING DUE TO SCALE BUILD-UPS
–
Analyse water at the required frequency intervals, making sure that the values are within the limits specified in the technical
manual and performing the suitable treatments.(EN 12953-10)
WATER CONDUCTIVITY
–
Water delivery has to be checked and kept within the limit values declared in the instruction manual and prescribed by EN
12953-10, according to a suitable treatment with filtering, softening and conditioning processes of the mains water (specified
on the user's manual and under the user's responsibility).
–
Carry out operational tests of the safety devices at the times and with methods specified in the manuals.
CAUSTIC EMBRITTLEMENT
–
Carry out water analysis at the necessary time intervals (refer to user's manual).
–
Perform water treatments in order to bring the characteristic values back within the limits specified in the use and
maintenance manual.
–
Blowdown by working on the drain valves present on boiler bottom.
Cooke Industries - Phone: +64 9 579 2185 Email: [email protected] Web: www.cookeindustries.co.nz