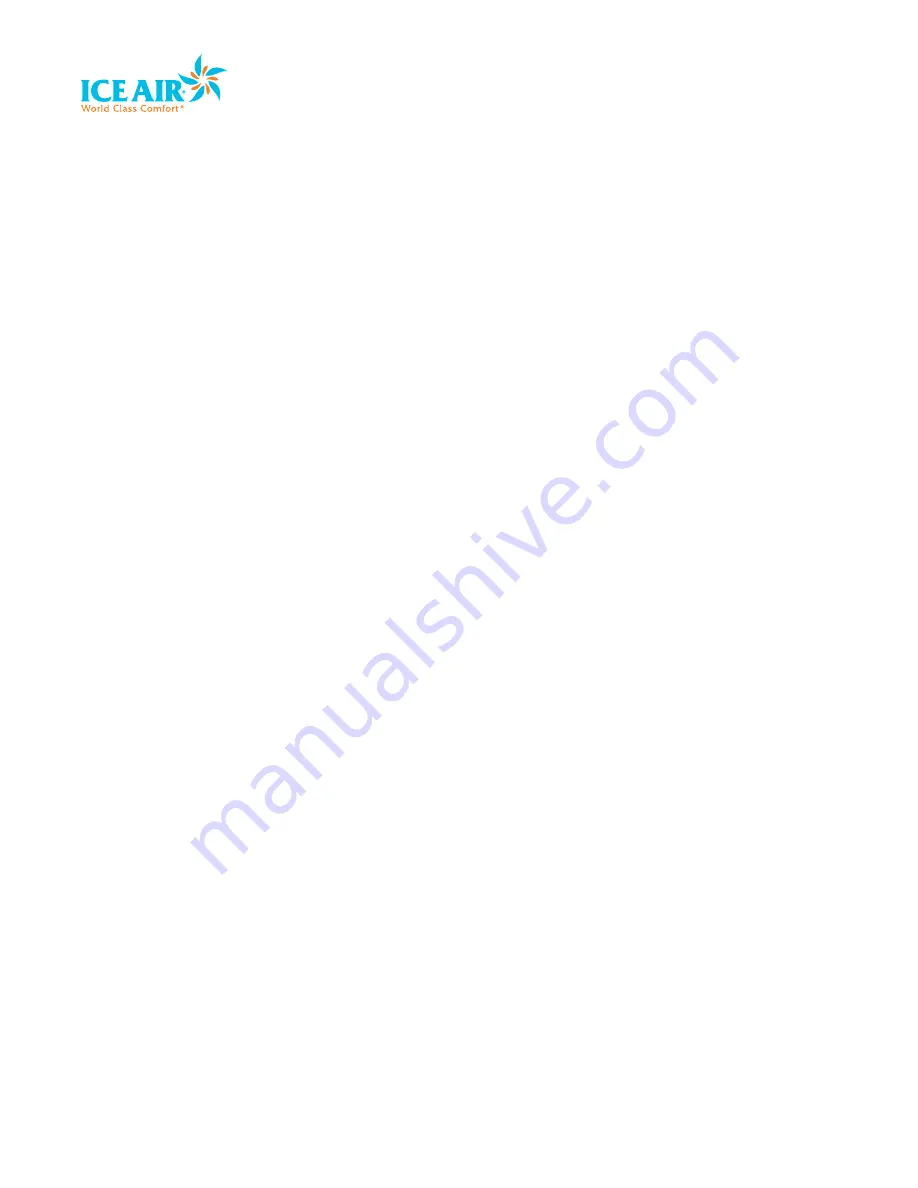
Due to Ice Air’s ongoing product development programs, the information in this document is subject to change without notice.
8
Riser Sizing and Insulation
Riser sizing is generally based on the water flow requirements of
each unit and will vary depending on unit location within the building
(units on higher and lower floors that tie into the same riser column
may require different size risers, depending on the piping system
chosen). The riser material, diameter, length and insulation thickness
must be determined for each unit based on its positioning within the
building and the overall system requirements.
IMPORTANT:
Please consult an engineer before proceeding with
riser installation.
Riser Expansion
Generally, in medium to high-rise buildings, allowances must be
made for pipe expansion. In applications supplemented with factory-
or field-supplied between floor riser extensions, assemble and install
extensions before installing the unit cabinet.
NOTES: Riser assemblies are designed to accommodate a maximum
of 1-1/8” expansion and contraction up to a total movement of
2-1/4”. If the total calculated rise expansion exceeds 2-1/4”,
expansion devices must be used (field provided).
All riser modification necessitated by variations in floor-to-floor
dimensions, including cutting off or extending risers, or providing
extensions, are the sole responsibility of the installing contractor.
In cases where piping movement is expected to exceed the factory
allowances, additional expansion compensation must be made to
the riser system in the field. The graph below displays the expansion
characteristics of risers compared to water temperature differential.
Assuming a minimum water temperature of 20°F and a maximum
water temperature of 120°F, the temperature difference of 100°F
indicates 90 feet of riser will expand or contract 1”. To eliminate
stress, a riser system must be anchored at least once to the building
structure. Technical information on pipe expansion, contraction and
anchoring can be found in the
ASHRAE HVAC Systems and Equip-
ment Handbook
. Riser expansion and the anchoring of both the riser
system and each unit is the responsibility of the design engineer and
installing contractor.
Riser Connection
Install cabinet with risers as follows:
1. Move cabinet into position. CAUTION: Keep risers off the floor
while moving the cabinet.
2. Be sure that all the copper fittings are clean and free of dirt.
3. Raise the cabinet upright and lower it so the attached risers
fit into the risers from the unit previously installed on the floor
below.
NOTE: The top of each riser is equipped with a 3” deep swaged
connection. There is sufficient extension at the bottom to allow
insertion of approximately 2” of the riser into the swaged top of
the riser below.
4. Center the risers in the pipe chase and shim the unit cabinet to
a level position. Plumb the risers in two planes to assure proper
unit operation and condensate drainage.
5. Attach the cabinet assembly to the floor and to the building
structure on at least two sides using sheet metal angles (field
provided).
NOTE: A field provided base vibration dampening pad can be
used to help eliminate transfer of any vibration from the unit to
the building structure. If vibration dampening pads are used,
some rough-in dimensional changes will need to be considered
before installation due to the type and thickness of the pads.
Additional anchorage can be provided by installing brackets at
the top of the cabinet (field provided).
6. DO NOT attach drywall studs to the equipment cabinet.
7. When all units on a riser are anchored into place, complete riser
joints as follows:
– Verify that all riser joints are vertically aligned and that risers
penetrate at least 1” into the swaged joint of the riser below.
DO NOT let riser joint bottom out.
– Braze riser joints with a high-temperature alloy using proper
Phos-copper or Silfos. Soft solder 50-50, 60-40, 85-15,
95-5 and low temperature alloys are not suitable riser weld
materials.
– Anchor built-in risers to the building structure with at least
one contact point. To accommodate vertical expansion and
contraction DO NOT fasten risers rigidly within the unit.
– Verify that unit shut-off valves are closed. DO NOT OPEN
VALVES until the system has been cleaned and flushed.
– Flush system, refer to “System Cleaning and Flushing” ection
of this manual for more information.
– Install vents in piping loop as required to bleed the system of
air accumulated during installation.