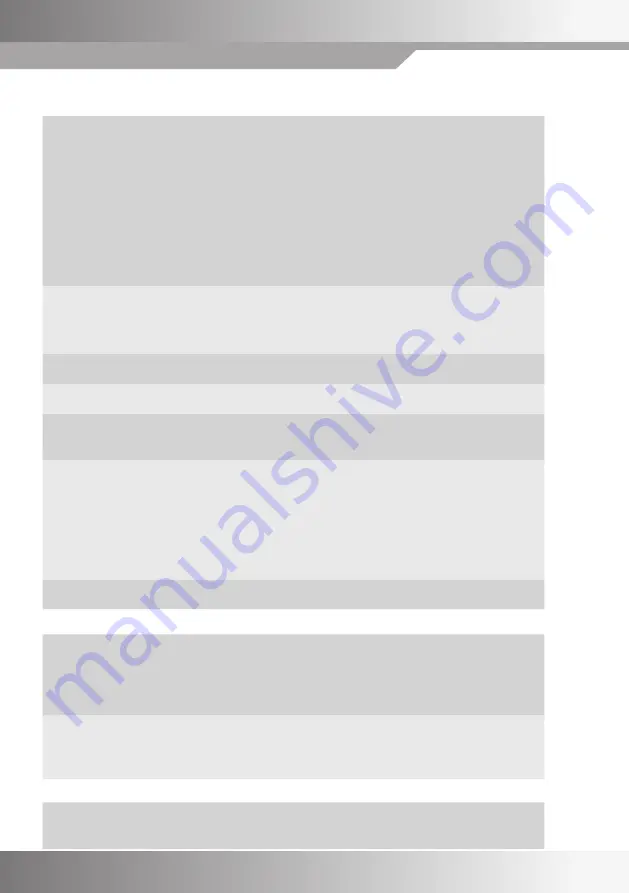
Continued from previous page
Probable fault cause
during installation
Probable fault cause in
operation
- Magnet turned the wrong way
- Magnet transmitter incorrectly connected (wrong polarity),
refer to "connections" on page 9
- Gap too wide between the magnetic sensor and magnet; max 15 mm
- Broken belt
- Belt slipping
- Stuck rotor
- Magnetic sensor or magnet not intact
Motor temperature
Alarms and trips if motor winding temperature is too high. The
temperature switch in the motor reverts to normal mode when the
temperature drops.
Excess voltage
Alarms and trips if the input voltage exceeds 265 V.
Under-voltage
Alarms and trips if the input voltage falls below 190 V.
Excessive /under-
temperature
Alarms and trips if the temperature in the control unit goes above/below
safe temperature level (+85 - -30
O
C).
Short circuit
Probable cause
Alarms and trips in the event of short circuit phase-phase or phase-earth.
- Short circuit between phases in cable or motor
- Short circuit between phase-earth in cable or motor
- Interruption to one phase in cable or motor
Measure motor resistance; it should be identical on all coils.
Internal fault
Alarms and trips if an internal fault in the control system has occurred.
SETTINGS VIA POTENTIOMETER
Manual speed
By closing A1-A2 the speed is controlled via the potentiometer marked
"Manual speed". Can be regulated between 1 and 350 rpm.
The rotor rotates at the set speed, whatever the value of the input signal.
Factory setting: 1 rpm on motor shaft.
Max speed
Potentiometer for adjusting max. speed.
Regulates between 50 and 400 rpm.
Factory setting: 50 rpm on motor shaft.
PUSH BUTTON
Reset
Reset button for resetting the control unit. The control unit is also reset in
the event of voltage drop-out and closure between terminals 11 and 12.
9
8