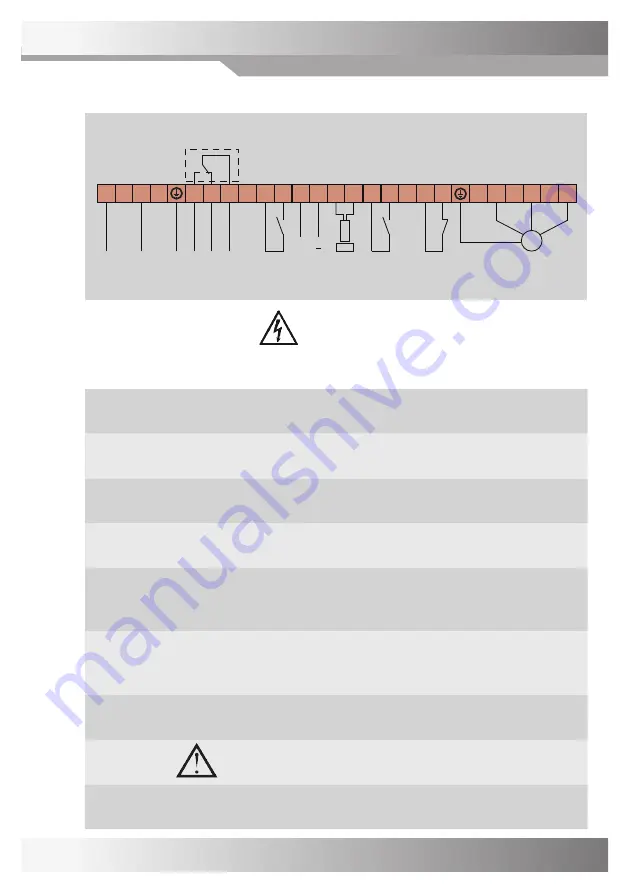
CONNECTIONS
The voltage must be switched off before undertaking any work on the equipment.
Recommended torque 0,5 Nm, max. torque 0,8 Nm.
Connected power supply
(L-N-PE)
1x230-240 V +/-15 %, 50/60 Hz.
NOTE! Protective earth must always be connected.
Alarm relay
(13-14-15)
Closes between 14-15 in the event of an alarm or voltage drop-out.
Max 2 A resistive load / 50 V AC.
Manual speed
(A1-A2)
Produces set rotation speed on connection.
Input signal
(2-3)
0-10 V.
Plus connected to terminal 2, minus to terminal 3.
Rotation monitor
(9-10)
White cable connected to terminal 9, brown to terminal 10.
The magnet is installed with south side (S) towards the sensor.
Max. gap 15 mm.
12 V output
(3-11)
Output for 12 V DC. Terminal connection 3 is minus (-),
terminal connection 11 is plus (+).
Max 50 mA.
Reset
(11-12)
Remote reset in the event of alarm.
The control unit is reset automatically in the event of voltage drop-out.
Thermal contact
(T-T)
This must be connected to protect the motor against overheating.
Motor
(U-V-W)
VariMax-motor50 must be used.
Direction of rotation is changed by switching two of the phases.
CONNECTION DIAGRAM
N
14 15
1 x 230 V
M
13
(Max 2 A / 50 V AC)
Alarm relay
2 3
+
9 10
v
A1 A2
S
br
Manual
speed
Rotation
monitor
11 12
T T
U
V
W
Reset
Thermal
contact
Stepping motor 3-phase
4
5
1
2
3
L
B C
A
Modbus
D+ D+ Com
Input
signal
0 - 10 V
9