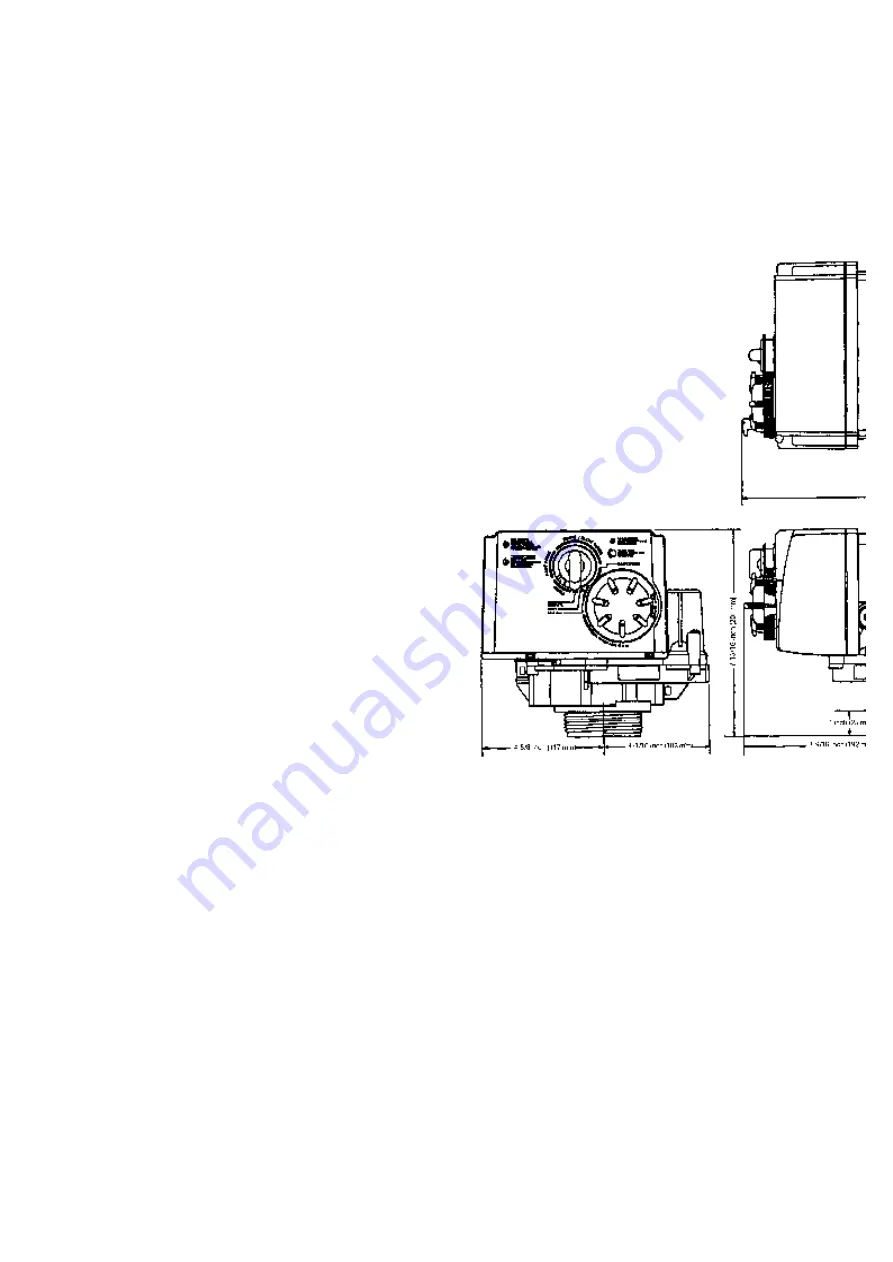
AST1052T-940
Page
18
10. Slowly open the water supply valve or return the
bypass valve(s) to the not in bypass" position.
11. Reconnect electric power, and reset the time of
day.
Hydrostatic Test Pressure ……………………………………………………………………………. 300 psi
(2069kPa)
Working Pressure ………………………………………….. 20 to 127 psi (138 to 876 kPa), 100 psi max in
Canada
Voltage ……………………………….. 24V 50 Hz, 24V 60 Hz, 100V 50 Hz, 100V 60 Hz, 230V 50 Hz, 115V 60
Hz
Current ……………………………………………………………………………………………………………….. 50
mA
Operating Temperature …………………………………………………………………..… 34°F (1°C) to 120°F
(49°C)
Humidity ………………………………………………………………...…………….10% to 100%, condensing
allowed
Pressure Tank Thread ………………………………………………………………………………… 2 1/2 in - 8
NPSM
Brine Line Thread ………………………………………………………………………………………... 1/4 in NPT
male
Distributor Tube Diameter Required …………………………………………………………. 13/16 in O.D. (20.6
mm)
Summary of Contents for AST1052T-940
Page 20: ...AST1052T 940 Page 20 Control Valving Identification Valve Disc Operation ...
Page 21: ...AST1052T 940 Page 21 Flow Diagrams ...
Page 22: ...AST1052T 940 Page 22 ...
Page 24: ...AST1052T 940 Page 24 ...
Page 25: ...AST1052T 940 Page 25 Valve Body and Tank Adaptor Module ...
Page 29: ...AST1052T 940 Page 29 ...