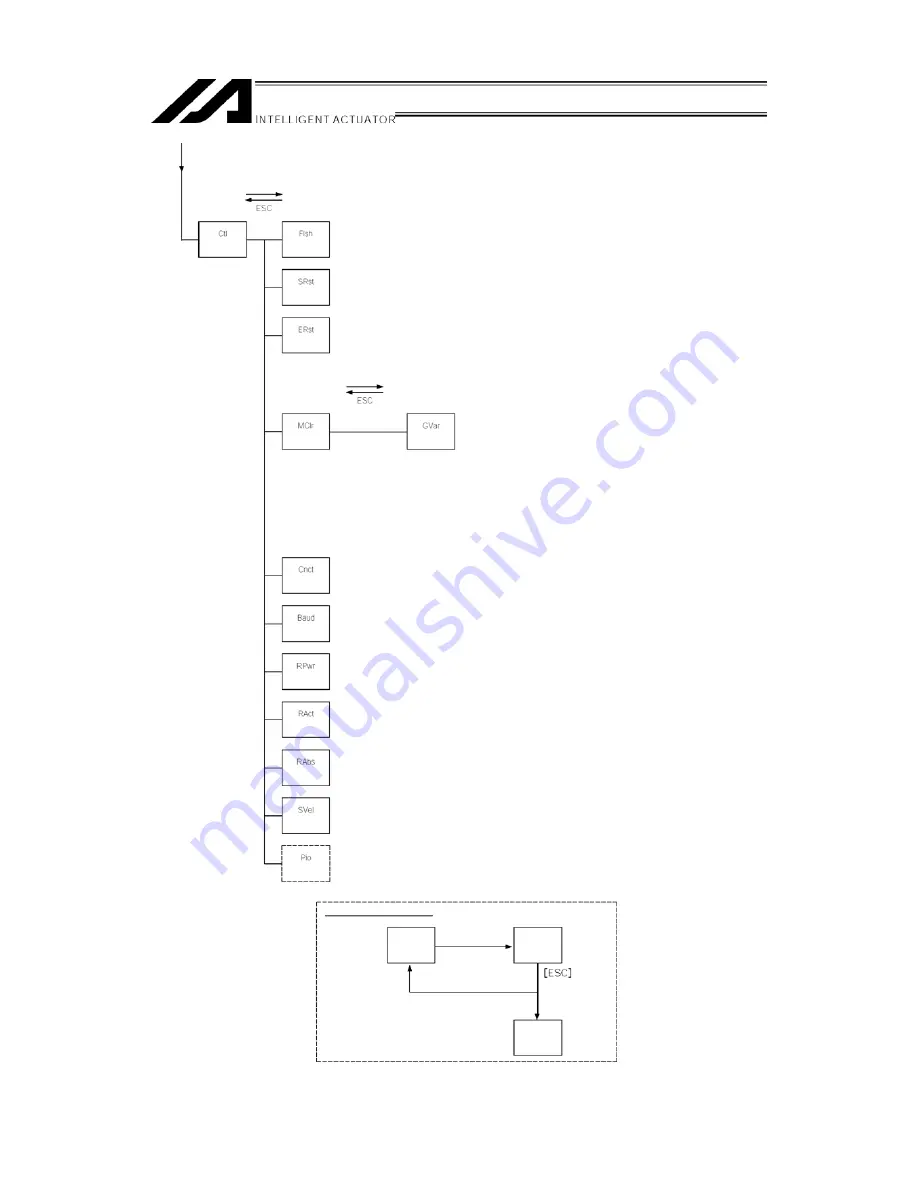
Function key
(Flash ROM
writing)
(Controller)
(Software
reset)
(Error reset)
Function key
(Memory
clear)
(Global
variable)
(Re-connect)
(Baud rate
change)
(Driver power
recovery request)
(Action pause
release request)
(Absolute
reset)
* You need to input the password to change setting, when manual operation classification
parameter=edit/start up selection (with password).
(Velocity effect
select)
* Displayed only when manual operation classification parameter=edit/start up selection (with
password).
* You will need to input the password to change setting.
(Refer to the Supplement and section 8 “Manual Operation” in the X-SEL Controller Instruction
Manual.)
(PIO start
prohibit select)
▪
Flow at Error Occurrence
Error occurs
Mode under
operation
Message
display
Serious error
Minor error
Re-connection
mode
15