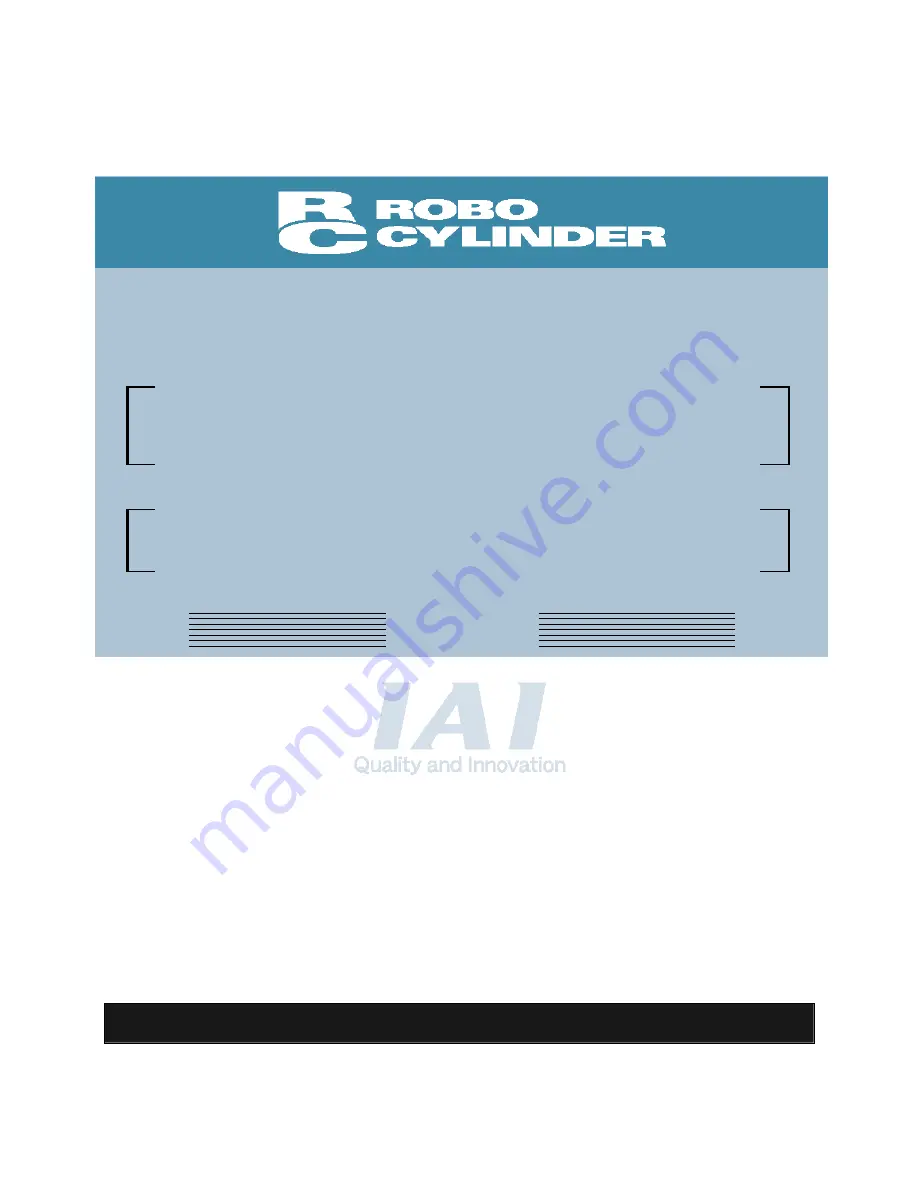
IAI America, Inc.
ROBO Cylinder
Slider Type
Fourth Edition
Motor Straight Type (Coupling Type): SA4C, SA5C SA6C, SA7C, SS7C and SS8C
Motor Straight Type (Built-in Type):
SA4D, SA5D and SA6D
Motor Reversing Type:
SA4R, SA5R, SA6R, SA7R, SS7R and SS8R
RCS2 Actuators
Motor Straight Type (Coupling Type): SA4C, SA5C, SA6C, SA7C, SS7C and SS8C
Motor Straight Type (Built-in Type):
SA5D and SA 6D
RCS2CR Actuators, Cleanroom Specification
Operating Manual