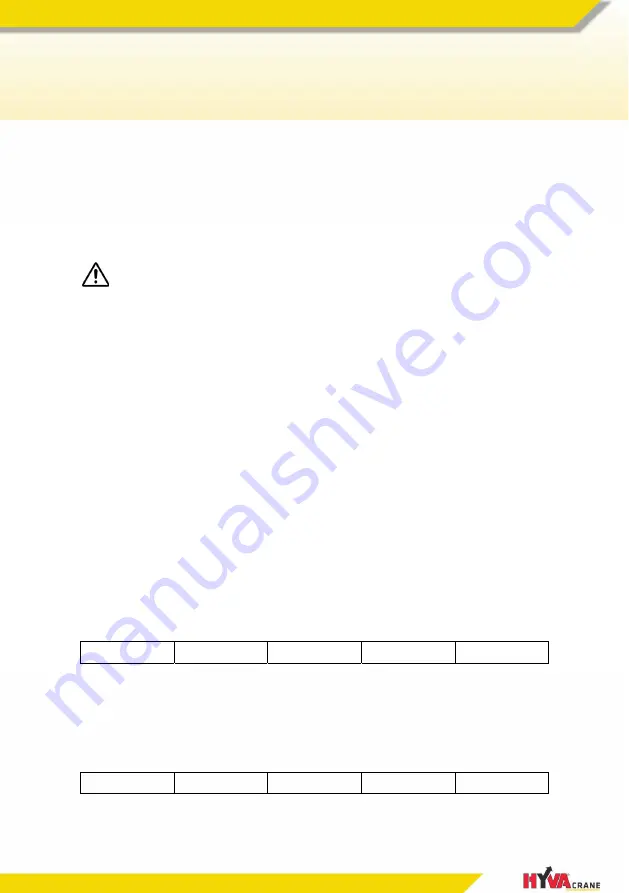
USER
MANUAL
HC1151
M
AINTENANCE
C.1
7845436-01 11/18
subject to change without notice
C MAINTENANCE
C.1 WARRANTY
TERMS
The manufacturer declines all responsibility for damage to the crane caused by failed maintenance
or lubrication. Preventive routine maintenance refers to machine use in non-abrasive and non-
corrosive environments. Failure to abide by this stipulation shall result in all guarantees for faults
being declared null and void.
All repairs, modifications and maintenance (excluding routine) must be performed by an
authorised assistance centre. All repair reports drafted by authorised assistance centres following
routine and extraordinary maintenance must be recorded and archived by the owner of the crane.
C.2 ORDINARY
MAINTENANCE
The following routine maintenance shall be performed by the operator to ensure machine efficiency:
- greasing
- filling up the oil tank
- crane cleaning
- wire rope inspection (if present)
Check the following before performing any maintenance operation:
- The vehicle must be switched OFF and the brake applied
- The power supply to the crane must be switched OFF
C.2.1 GREASING
Grease the machine at regular intervals to improve crane functioning and avoid extraordinary
maintenance. Use always new grease. Do NOT mix greases of different types.
Greasing is performed in the following ways: manual, under pressure, automated.
MANUAL GREASING
Remove grease from telescopic extensions using a soft spatula (plastic or wood).
Use a brush to spread a new layer of grease on the contact surface.
Use a type of grease compatible with that indicated in the following table.
Recommended greases (NLGI 2 - DIN 51818)
TOTAL MOBIL ESSO AGIP
IP
MULTIS MS 2
MOBILGREASE MP
BEACON EP 2
GR MU EP 2
ATHESIA EP GR 2
PRESSURE GREASING
Carefully clean the grease nipple.
Inject new grease until absolutely clean grease comes out of the joints.
Then remove any excess grease.
Use a type of grease compatible with that indicated in the following table.
Recommended greases (NLGI 2 - DIN 51818)
TOTAL MOBIL ESSO AGIP
IP
MULTIS MS 2
MOBILGREASE MP
BEACON EP 2
GR MU EP 2
ATHESIA EP GR 2