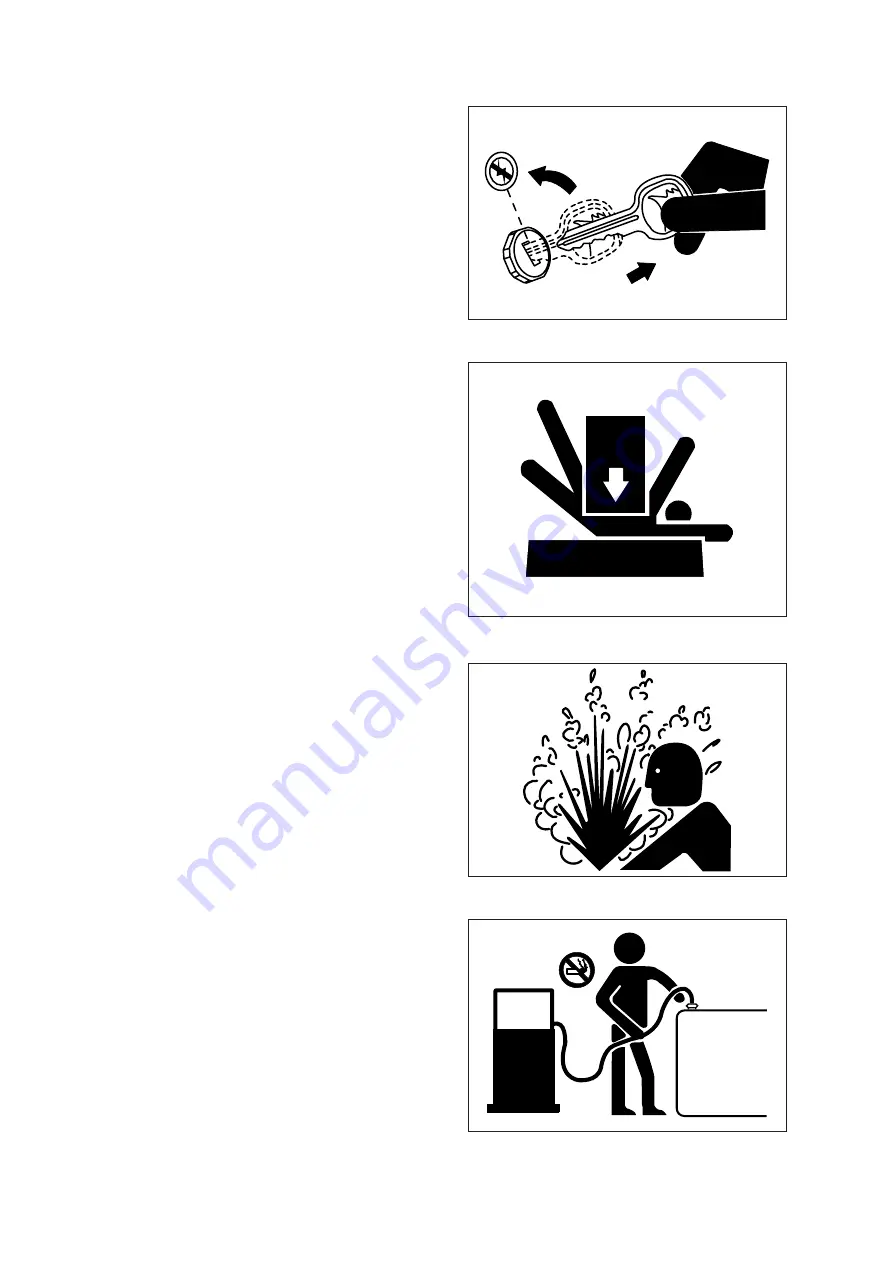
1-3
SUPPORT MACHINE PROPERLY
SUPPORT MACHINE PROPERLY
Always lower the attachment or implement to
the ground before you work on the machine. If
you must work on a lifted machine or attachment,
securely support the machine or attachment.
Do not support the machine on cinder blocks,
hollow tiles, or props that may crumble under
continuous load.
Do not work under a machine that is supported
solely by a jack. Follow recommended
procedures in this manual.
SERVICE COOLING SYSTEM SAFELY
SERVICE COOLING SYSTEM SAFELY
Explosive release of fluids from pressurized
cooling system can cause serious burns.
Shut off engine. Only remove filler cap when
cool enough to touch with bare hands.
HANDLE FLUIDS SAFELY-AVOID FIRES
HANDLE FLUIDS SAFELY-AVOID FIRES
Handle fuel with care; It is highly flammable.
Do not refuel the machine while smoking or
when near open flame or sparks. Always stop
engine before refueling machine.
Fill fuel tank outdoors.
PARK MACHINE SAFELY
PARK MACHINE SAFELY
Before working on the machine:
Park machine on a level surface.
Lower bucket to the ground.
Turn key switch to OFF to stop engine.
Remove key from switch.
Press down to switch off safety switch.
Allow engine to cool.
Â
Â
Â
Â
Â
73031GE23
73031GE06
73031GE07
73031GE08