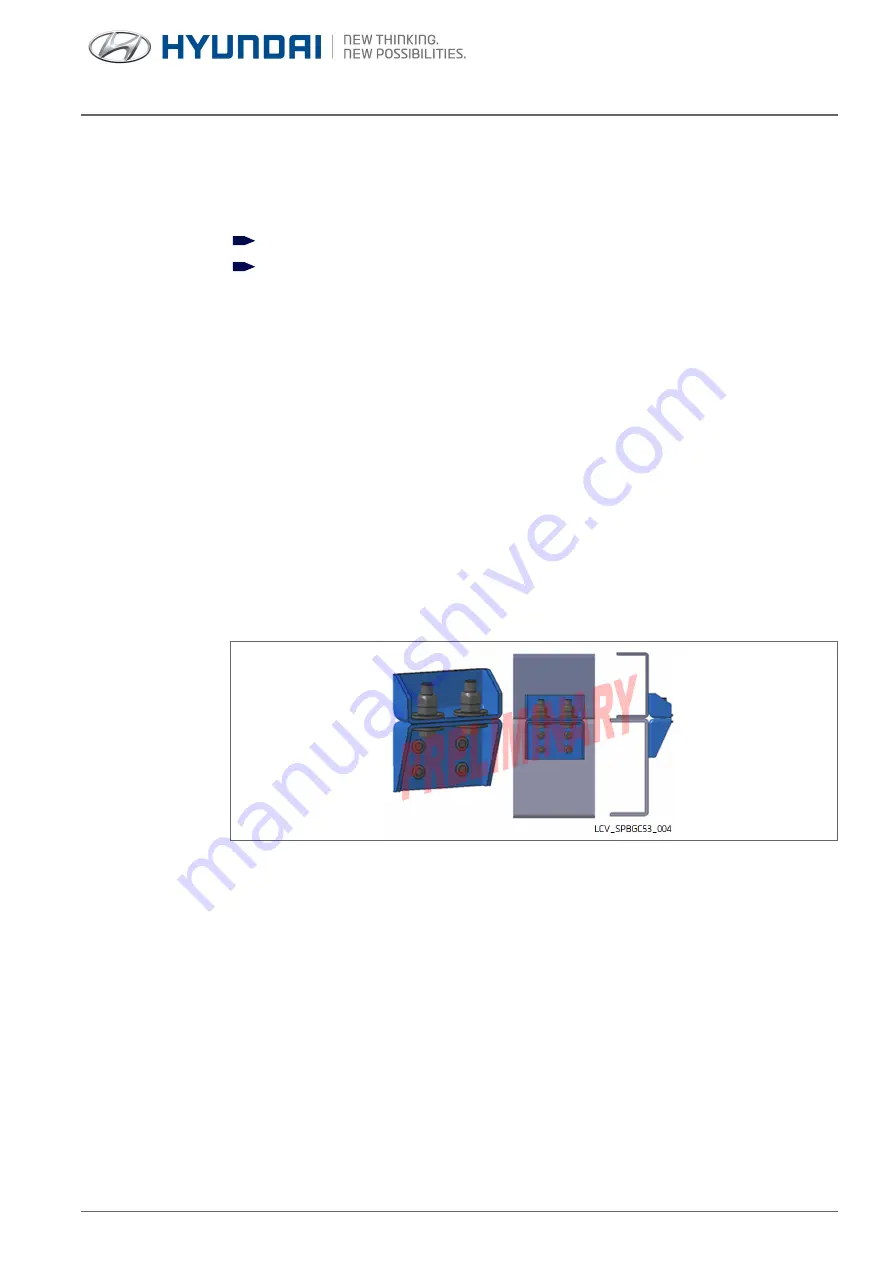
INTRODUCTION
PRELIMINAR STUDIES AND CONSIDERATIONS
MAINTENANCE AND DAMAGE PREVENTION
WORK ON BASIC VEHICLE
MOUNTING AND CONSTRUCTION
POWER TAKE-OFF
ELECTRIC AND ELECTRONIC SYSTEMS
APPENDIX
V1.0, February 2015
Body Builder Manual Part II, Specific Book LCV
157
Usually, attachments are divided into rigid and flexible connections. Depending on
their design and characteristics, the connections provide a larger or smaller
number of degrees of freedom of movement, and provide varying degrees of stiff
-
ness to the group formed by chassis frame and subframe.
See chapter 5.3.2 "Flexible connection".
See chapter 5.3.3 "Rigid connection".
5.3.2
Flexible connection
These connections offer little resistance to torsional stresses, allowing a relative
movement between the chassis frame and the subframe. On irregular road surfaces,
these connections enable both elements to be harmonised with each other, making
it possible to achieve a good balance between vehicle stability and a high level of
comfort while driving.
According to the freedom of movement provided by the connection and the rigidity
offered, these will be considered more or less flexible (semi-flexible), i.e. they pro
-
vide a degree of resistance to higher or lower torsional stresses.
Therefore, HMC recommends the use of different types of flexible connections,
with varying degrees of flexibility, depending on requirements.
In most of cases, a connection with a lower degree of flexibilityis recommended.
This is type F_1.
Fig. 5-113 SPBGC53_004 F_1-type subframe connection
The torsional forces and lateral movements are generally higher behind the cab, in
the wheelbase area, where the maximum deformations are caused. The loads grad
-
ually decrease along the vehicle frame towards the rear, where, thanks to the rear
axles, the suspension and its reinforcements, the rigidity of the structure increases,
and this reduces any deformation of the chassis.