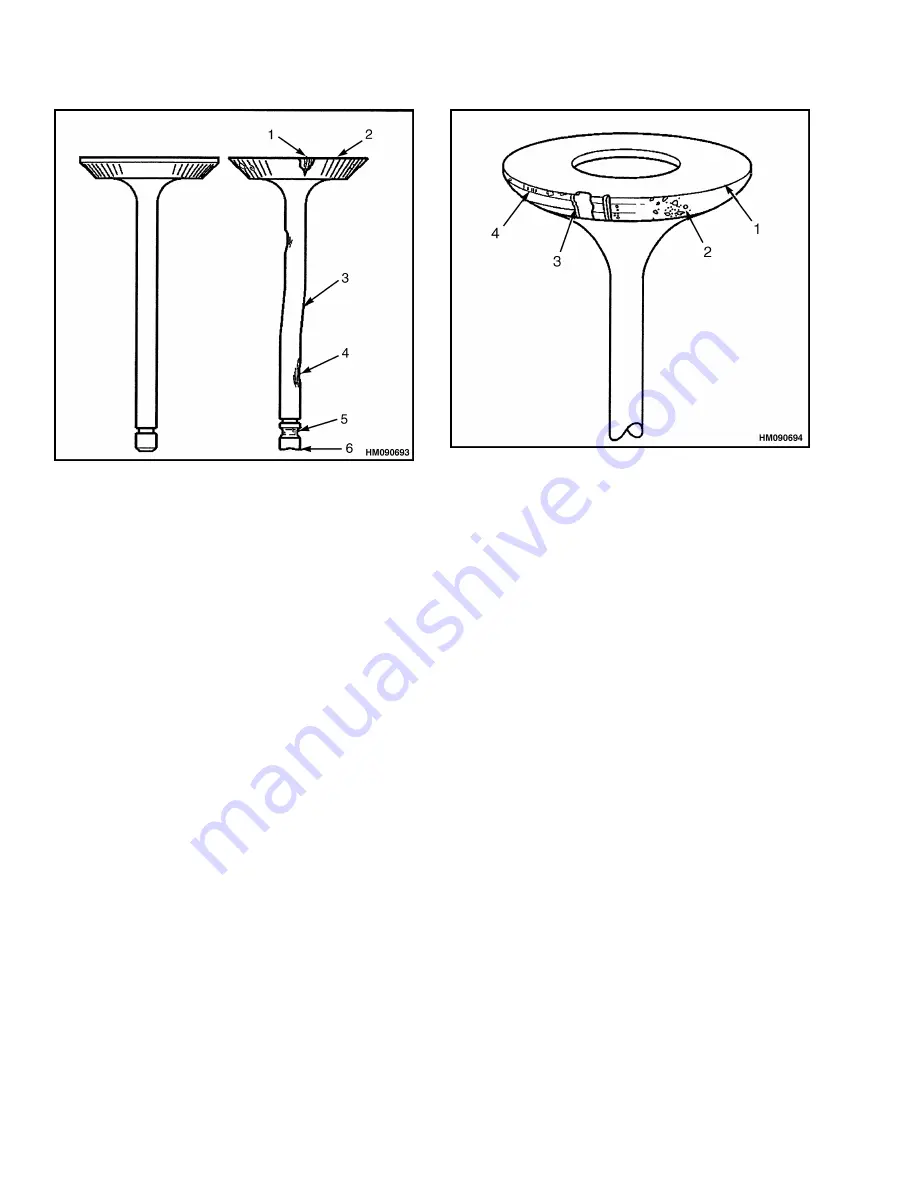
1. BURNT OR DAMAGED AREAS
2. UNDERSIZED MARGIN
3. BENT STEM
4. SCORING/DAMAGE TO THE STEM
5. WORN KEY GROOVE
6. WORN STEM TIP
Figure 7. Valve Inspection
Valve stems with excessive guide clearance must
be repaired or replaced. Refer to Engine Specifi-
cations.
8.
Inspect valve contact surface for the following:
• Undersized margin
• Pitted surface
• Burnt or eroded areas
• Acceptable edge margin
Valves with excessive damage must be replaced.
Minor imperfections of valve or valve seat may
be repaired. Refer to Valve Guides and Seats,
Repairs or Valves, Repair.
VALVE OIL SEALS
The following procedure addresses replacement of
valve oil seals. If ONLY valve oil seals are being re-
placed, it is not necessary to remove the cylinder
head.
1. UNDERSIZED MARGIN
2. PITTED SURFACE
3. BURNT OR ERODED AREAS
4. ACCEPTABLE EDGE MARGIN
Figure 8. Valve Contact Surface Inspection
Remove and Disassemble
1.
Remove spark plug wires from spark plugs and
position spark plug wires out of way.
2.
Remove each spark plug and spark plug wire
shield.
NOTE:
If spark plugs are not being replaced label
each spark plug to its corresponding cylinder.
3.
Remove rocker cover bolts and grommets. Dis-
card grommets. Repeat for other rocker cover.
4.
Remove rocker covers. Disconnect the Positive
Crankcase Ventilation valve from the air inlet
hose.
5.
Perform cylinder leak down test for each cylin-
der. See Cylinder Leak Down Test.
6.
Remove valve rocker arms. Organize rocker
arms so they can be installed in their original
positions. Repeat for other side.
Cylinder Head Repair
0600 SRM 1251
6