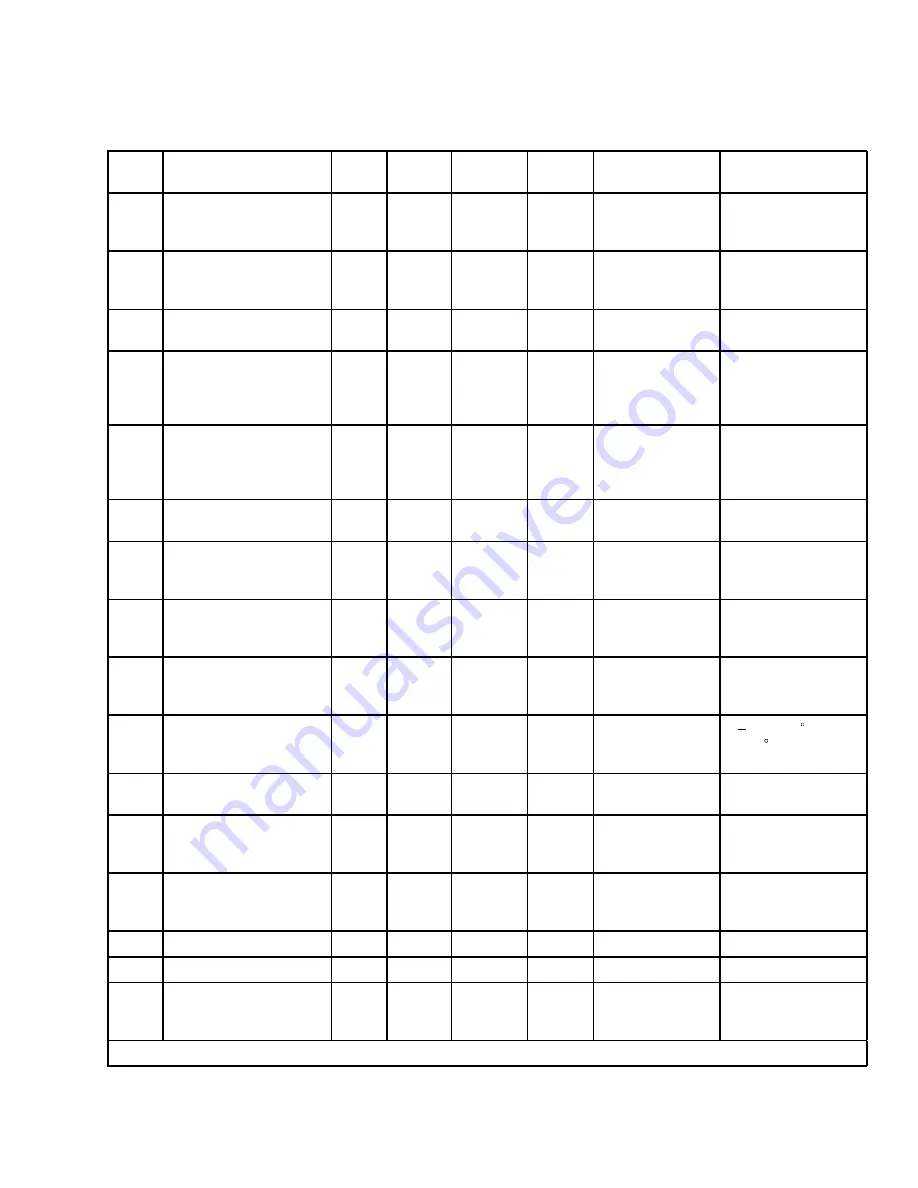
8000 SRM 1226
Maintenance Schedule
Table 1. Maintenance Schedule (Continued)
Item
No.
Item
8 hr/
1 day
500 hr/
3 mo
1000 hr/
6 mo
2000 hr/
1 yr
Procedure or
Quantity
Specification
11
Lift Chains
L
Remove Lift
Chains to Clean
and Lubricate
Engine Oil
12
Forks
X
X
X
Check Condition
and Replace if
Necessary
13
Intergral Sideshift
Carriage
L
4 Fittings
Multipurpose Grease
See NOTE 1
13
Integral Sideshift
Carriage
(Upper/Lower
Bear-
ings)
X
Check Wear
4 Bearings
2.5 mm (0.098 in.)
Minimum Thickness
13
Integral Sideshift
Carriage
(Upper/Lower
Bear-
ings)
C
Replace Bearings
4 Bearings
14
Fork Pins and Guides
L
Lubricate as
Necessary
Engine Oil
15
Direction and Speed
Control Pedals
X
Check Operation
Lubricate as
Necessary
See NOTE 1
16
Hydraulic Filter
C
1 Filter
See NOTE 2
and NOTE 6
See Parts Manual
17
Hydraulic Oil
(FULL Mark)
X
Check Oil Level
17
Hydraulic Oil
(FULL Mark)
C
27.4 liter (29.0 qt)
18 to 38 C (0 to
100
F)
ISO-VG46
18
Hydraulic Tank Breather
C
Replace
See NOTE 2
See Parts Manual
19
Steering Axle Spindles
King Pins
L
2 Fittings
See NOTE 2 and
Multipurpose Grease
See NOTE 1
19
Steering
Tie Rods
L
4 Fittings
See NOTE 4
Multipurpose Grease
See NOTE 1
20
Contactors
X
Check Condition
See Parts Manual
Horn, Lights, and Alarm
X
Check Operation
Hinges, Levers, Linkage,
Pedals, and Seat Rails
L
As Required
Multipurpose Grease
See NOTE 1 and
X=Check C=Change L=Lubricate CIL=Check Indicator Light during operation
5